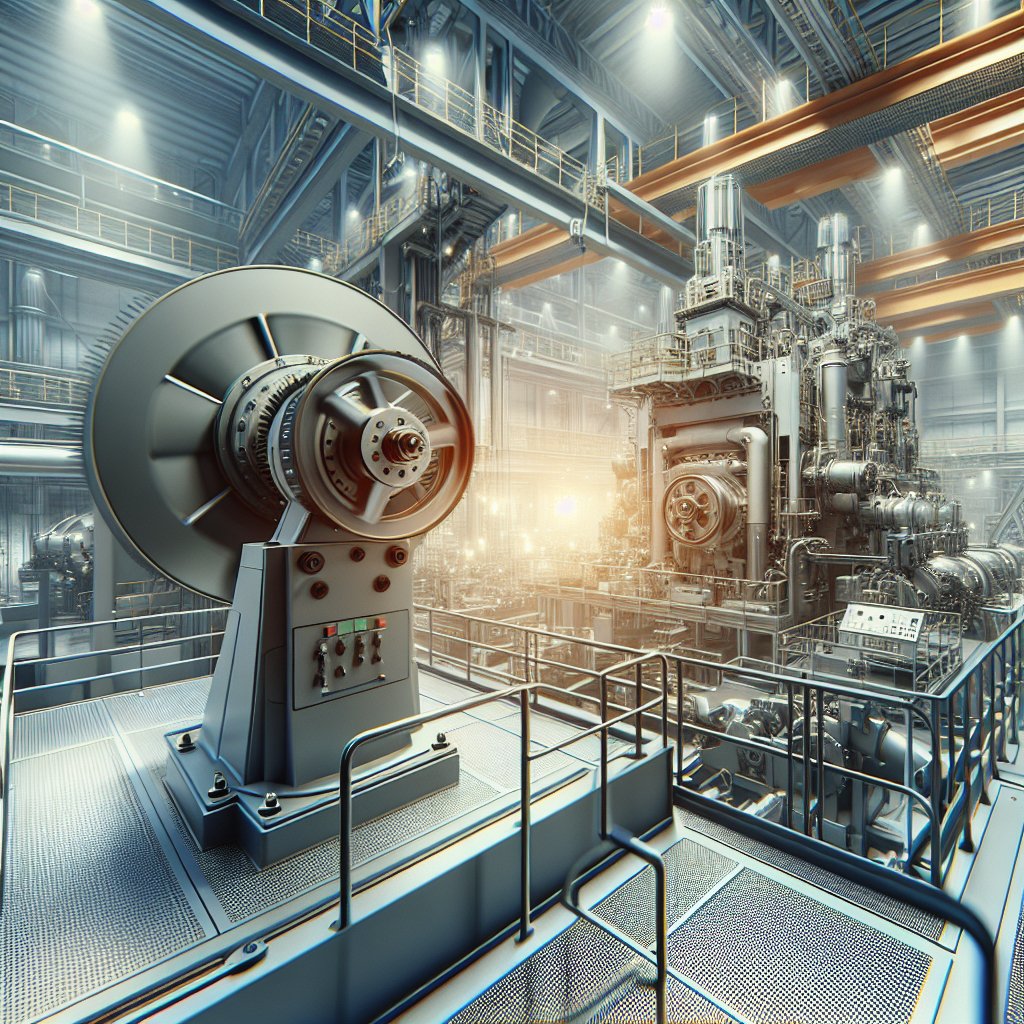
Vibration analysis is a critical component in the maintenance and operation of industrial machinery, offering insights that can prevent costly downtime and extend the lifespan of equipment. By understanding the nuances of vibration patterns, engineers and maintenance teams can diagnose issues before they escalate, ensuring that machinery operates efficiently and safely. This article delves into the importance of vibration analysis, exploring its benefits, methodologies, and applications in various industrial settings.
Understanding Vibration Analysis
Vibration analysis is a technique used to monitor the condition of machinery by measuring the vibrations produced during operation. Every piece of machinery has a unique vibration signature, which can be analyzed to detect abnormalities. These abnormalities often indicate potential issues such as imbalance, misalignment, wear, or mechanical looseness.
The process involves using sensors and data acquisition systems to capture vibration signals. These signals are then processed and analyzed using specialized software to identify patterns and anomalies. The results can provide valuable insights into the health of the machinery, allowing for timely maintenance and repairs.
The Science Behind Vibration
At its core, vibration is a mechanical phenomenon where oscillations occur about an equilibrium point. In industrial machinery, these oscillations can be caused by various factors, including rotating components, moving parts, and external forces. The frequency, amplitude, and phase of these vibrations can reveal a lot about the condition of the equipment.
For instance, an increase in vibration amplitude might indicate a developing fault, while changes in frequency could suggest a shift in operational conditions. By analyzing these parameters, engineers can pinpoint the root cause of issues and take corrective actions.
Benefits of Vibration Analysis
Implementing vibration analysis in industrial settings offers numerous advantages. One of the primary benefits is the ability to perform predictive maintenance. By identifying potential issues early, maintenance teams can schedule repairs during planned downtime, minimizing disruptions to production.
Additionally, vibration analysis can help extend the lifespan of machinery. By addressing problems before they lead to significant damage, companies can avoid costly replacements and reduce the overall cost of ownership. This proactive approach also enhances safety by preventing catastrophic failures that could pose risks to personnel and equipment.
Cost Savings and Efficiency
Vibration analysis contributes to cost savings by reducing unplanned downtime and optimizing maintenance schedules. Instead of relying on time-based maintenance, which can be inefficient and costly, companies can adopt a condition-based approach. This ensures that maintenance is performed only when necessary, maximizing the use of resources and minimizing waste.
Moreover, by maintaining machinery in optimal condition, companies can improve operational efficiency. Well-maintained equipment operates more smoothly, consuming less energy and producing higher-quality outputs. This not only boosts productivity but also enhances the overall competitiveness of the business.
Methodologies in Vibration Analysis
There are several methodologies used in vibration analysis, each with its own set of tools and techniques. The choice of methodology depends on the specific requirements of the machinery and the goals of the analysis. Some of the most common methods include time-domain analysis, frequency-domain analysis, and modal analysis.
Time-Domain Analysis
Time-domain analysis involves examining the vibration signal as a function of time. This method is useful for identifying transient events and sudden changes in vibration patterns. By analyzing the time waveform, engineers can detect issues such as impacts, rubs, and other short-duration events that might not be apparent in other types of analysis.
Frequency-Domain Analysis
Frequency-domain analysis, on the other hand, focuses on the frequency components of the vibration signal. By transforming the time-domain signal into the frequency domain using techniques like the Fast Fourier Transform (FFT), engineers can identify specific frequencies associated with different types of faults. This method is particularly effective for diagnosing issues related to rotating components, such as imbalance and misalignment.
Modal Analysis
Modal analysis is used to study the dynamic behavior of structures and components. It involves determining the natural frequencies, mode shapes, and damping characteristics of a system. This information is crucial for understanding how a structure will respond to different types of excitations and for designing systems that can withstand operational stresses.
Applications of Vibration Analysis
Vibration analysis is widely used across various industries, from manufacturing and energy to transportation and aerospace. In each of these sectors, the technique plays a vital role in ensuring the reliability and efficiency of machinery.
Manufacturing
In the manufacturing industry, vibration analysis is used to monitor the condition of critical equipment such as motors, pumps, and compressors. By detecting issues early, manufacturers can prevent production delays and maintain high-quality standards.
Energy
In the energy sector, vibration analysis is essential for maintaining the performance of turbines, generators, and other power generation equipment. By ensuring that these machines operate smoothly, energy companies can maximize output and reduce operational costs.
Transportation and Aerospace
In transportation and aerospace, vibration analysis is used to ensure the safety and reliability of vehicles and aircraft. By monitoring the condition of engines, gearboxes, and other critical components, engineers can prevent failures that could lead to accidents or costly repairs.
Conclusion
Vibration analysis is a powerful tool that offers significant benefits to industries reliant on complex machinery. By providing insights into the condition of equipment, it enables companies to adopt a proactive approach to maintenance, reducing costs, enhancing safety, and improving efficiency. As technology continues to advance, the capabilities of vibration analysis will only grow, offering even greater potential for optimizing industrial operations.