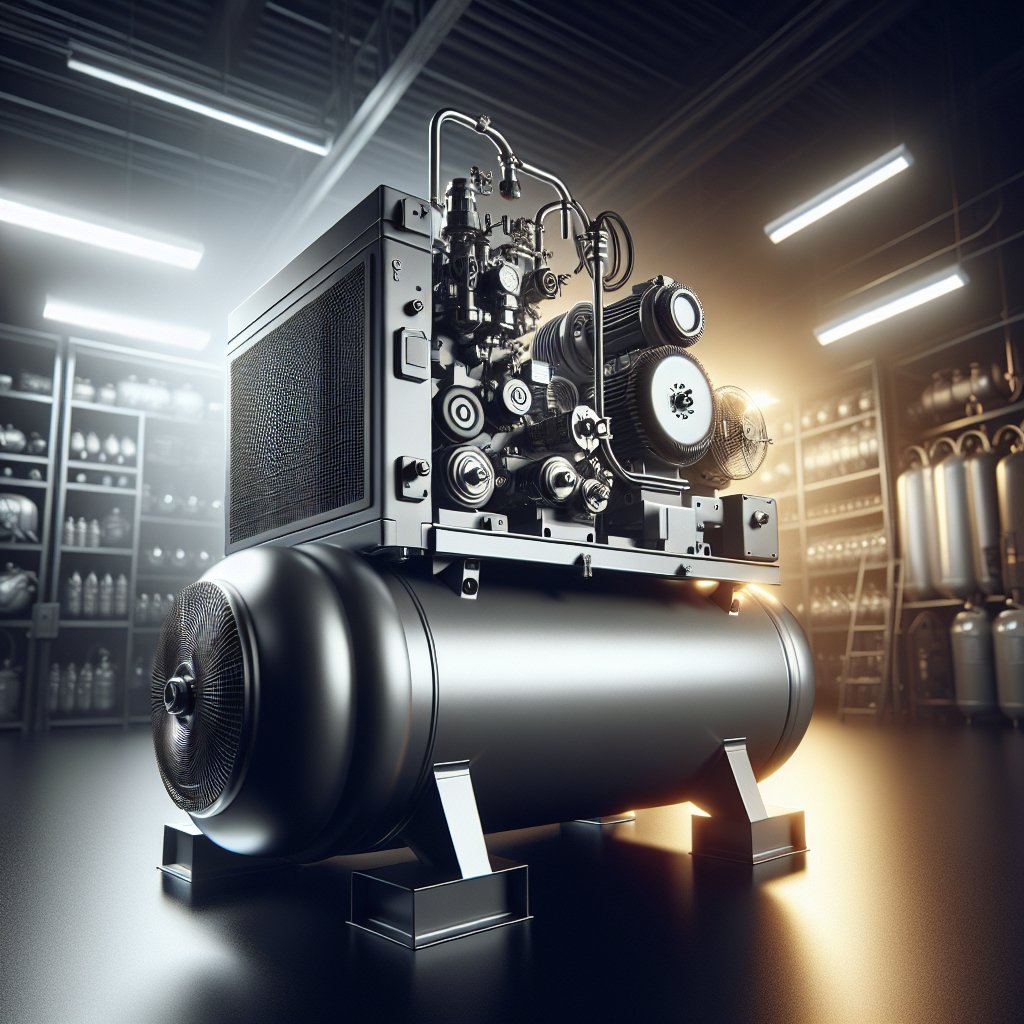
Industrial air compressors are essential tools in various industries, providing the power needed to operate machinery, tools, and other equipment. Understanding the basics of these devices is crucial for anyone involved in industrial operations, as it can lead to more efficient use, better maintenance, and improved safety. This article delves into the fundamental aspects of industrial air compressors, exploring their types, applications, and maintenance requirements.
Types of Industrial Air Compressors
Industrial air compressors come in several types, each designed to meet specific needs and applications. The most common types include reciprocating compressors, rotary screw compressors, and centrifugal compressors. Each type has its unique features, advantages, and limitations, making it suitable for different industrial environments.
Reciprocating Compressors
Reciprocating compressors, also known as piston compressors, are among the oldest and most widely used types of air compressors. They operate by using pistons driven by a crankshaft to deliver high-pressure air. These compressors are typically used in applications requiring high pressure and low flow rates, such as in automotive repair shops and small manufacturing facilities.
The main advantage of reciprocating compressors is their ability to deliver high-pressure air efficiently. However, they tend to be noisy and require regular maintenance due to the many moving parts involved. Proper lubrication and periodic inspection of components are essential to ensure their longevity and performance.
Rotary Screw Compressors
Rotary screw compressors are known for their reliability and efficiency, making them a popular choice in many industrial settings. They use two helical screws to compress air, providing a continuous flow of compressed air. This makes them ideal for applications requiring a steady supply of air, such as in large manufacturing plants and construction sites.
One of the key benefits of rotary screw compressors is their ability to operate quietly and with minimal vibration. They also require less maintenance compared to reciprocating compressors, as they have fewer moving parts. However, they are generally more expensive and may not be suitable for applications requiring very high pressure.
Centrifugal Compressors
Centrifugal compressors are used in applications requiring large volumes of air at moderate pressure. They work by using a rotating impeller to increase the velocity of the air, which is then converted into pressure. These compressors are commonly found in industries such as petrochemical, power generation, and HVAC systems.
The main advantage of centrifugal compressors is their ability to handle large volumes of air efficiently. They are also relatively low maintenance, as they have fewer moving parts compared to reciprocating compressors. However, they are typically more expensive and require a higher initial investment.
Applications of Industrial Air Compressors
Industrial air compressors are versatile tools used in a wide range of applications across various industries. Their ability to provide a reliable source of compressed air makes them indispensable in many operations. Some of the most common applications include manufacturing, construction, automotive, and food and beverage industries.
Manufacturing
In the manufacturing industry, air compressors are used to power pneumatic tools, control systems, and machinery. They are essential for processes such as assembly, painting, and packaging. The ability to provide a consistent and reliable source of compressed air is crucial for maintaining productivity and efficiency in manufacturing operations.
Manufacturers often rely on rotary screw compressors due to their ability to deliver a continuous flow of air. This ensures that production lines can operate smoothly without interruptions. Additionally, the use of air compressors in manufacturing helps reduce energy costs and improve overall efficiency.
Construction
Construction sites often require a portable and reliable source of compressed air to power tools and equipment. Air compressors are used to operate jackhammers, nail guns, and other pneumatic tools, making them essential for construction projects. The ability to provide high-pressure air on demand is crucial for completing tasks efficiently and safely.
Portable reciprocating compressors are commonly used in construction due to their ability to deliver high-pressure air in a compact and mobile package. This allows workers to easily transport the compressor to different locations on the site, ensuring that they have access to the power they need.
Automotive
The automotive industry relies heavily on air compressors for various applications, including painting, tire inflation, and powering pneumatic tools. In auto repair shops, air compressors are used to operate impact wrenches, spray guns, and other tools, making them essential for efficient and effective vehicle maintenance and repair.
Reciprocating compressors are often used in automotive applications due to their ability to deliver high-pressure air. This is particularly important for tasks such as tire inflation and operating impact wrenches, where precise control and high pressure are required.
Food and Beverage
In the food and beverage industry, air compressors are used for processes such as packaging, bottling, and conveying products. They provide a clean and reliable source of compressed air, which is essential for maintaining product quality and safety. The use of oil-free compressors is particularly important in this industry to prevent contamination.
Centrifugal compressors are often used in food and beverage applications due to their ability to handle large volumes of air efficiently. This is crucial for processes such as bottling and packaging, where a consistent and reliable source of air is needed to maintain production rates.
Maintenance and Safety Considerations
Proper maintenance and safety practices are essential for ensuring the longevity and performance of industrial air compressors. Regular maintenance helps prevent breakdowns and extends the life of the equipment, while safety practices help protect workers and prevent accidents.
Regular Maintenance
Regular maintenance is crucial for keeping industrial air compressors in optimal condition. This includes tasks such as checking and replacing filters, inspecting hoses and connections, and monitoring oil levels. Proper lubrication is also essential to prevent wear and tear on moving parts.
It’s important to follow the manufacturer’s recommended maintenance schedule and use the appropriate parts and lubricants. Regular inspections can help identify potential issues before they become major problems, reducing downtime and repair costs.
Safety Practices
Safety is a top priority when working with industrial air compressors. Proper training and safety protocols are essential to prevent accidents and injuries. Workers should be trained on how to operate the equipment safely and be aware of potential hazards such as high-pressure air and moving parts.
It’s important to use the appropriate personal protective equipment (PPE) when working with air compressors, such as safety glasses, gloves, and hearing protection. Additionally, safety features such as pressure relief valves and emergency shut-off switches should be regularly inspected and tested to ensure they are functioning properly.
In conclusion, understanding the basics of industrial air compressors is essential for anyone involved in industrial operations. By choosing the right type of compressor for the application, maintaining it properly, and following safety protocols, businesses can ensure efficient and safe operations. Whether in manufacturing, construction, automotive, or food and beverage industries, air compressors play a vital role in powering the tools and equipment needed to get the job done.