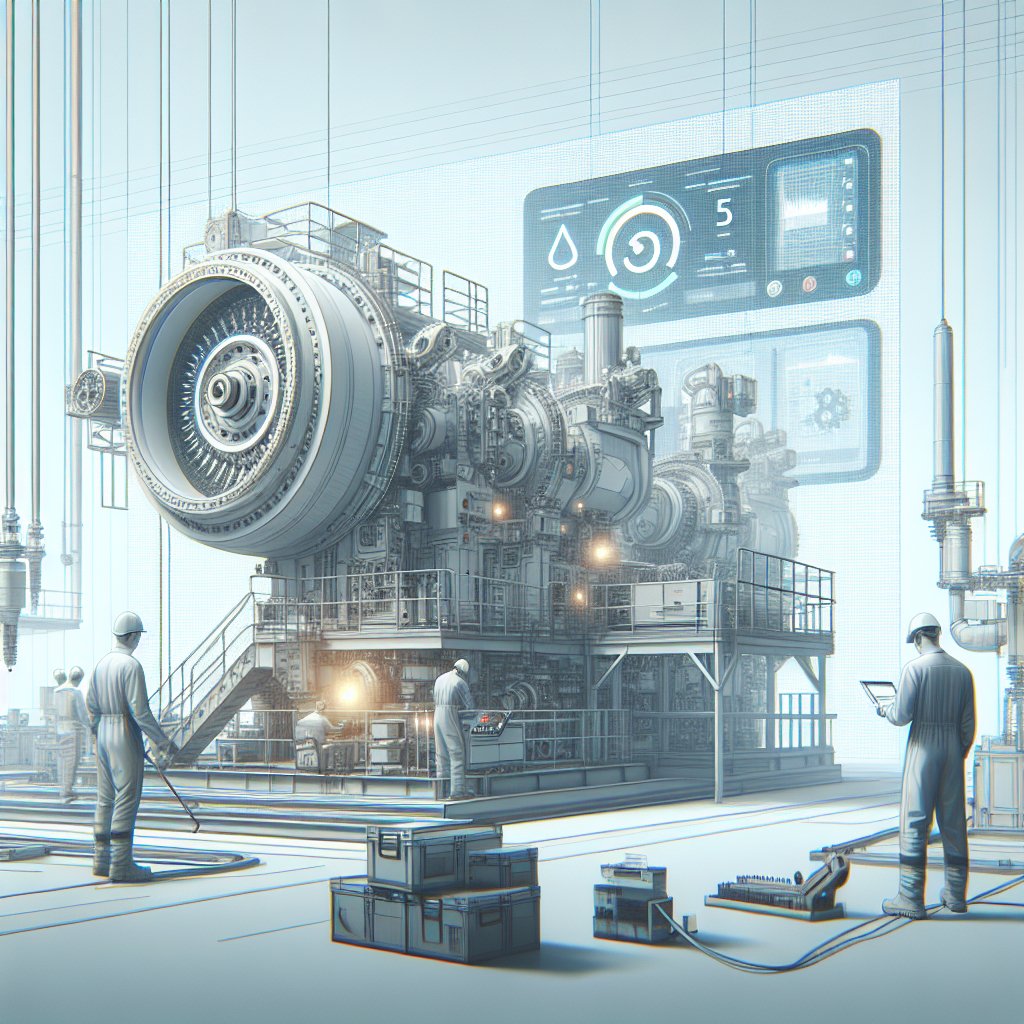
Vibration monitoring has become an essential component in the predictive maintenance of industrial machines, offering a proactive approach to identifying potential issues before they lead to costly downtime. By analyzing the vibrational patterns of machinery, maintenance teams can detect anomalies that may indicate wear, imbalance, or misalignment, allowing for timely interventions. This article delves into the significance of vibration monitoring, its methodologies, and its impact on the efficiency and longevity of industrial equipment.
Understanding Vibration Monitoring
Vibration monitoring is a technique used to measure the oscillations of machinery components. These oscillations, or vibrations, can provide critical insights into the health and performance of industrial machines. By capturing and analyzing vibration data, maintenance teams can identify deviations from normal operating conditions, which may signal the onset of mechanical issues.
The process typically involves the use of sensors, such as accelerometers, which are strategically placed on machinery to capture vibration data. This data is then processed and analyzed using specialized software to identify patterns and anomalies. The goal is to detect potential problems early, allowing for maintenance to be scheduled at a convenient time, thus minimizing unplanned downtime and extending the life of the equipment.
Types of Vibration Monitoring
There are several types of vibration monitoring techniques, each suited to different applications and machinery types. The most common methods include:
- Overall Vibration Monitoring: This method provides a general overview of the machine’s vibration levels. It is useful for detecting significant changes in vibration that may indicate a problem.
- Frequency Analysis: By analyzing the frequency spectrum of the vibrations, maintenance teams can pinpoint specific issues, such as imbalance or misalignment, based on characteristic frequency patterns.
- Time Waveform Analysis: This technique involves examining the raw vibration signal over time, which can reveal transient events or irregularities that may not be apparent in frequency analysis.
- Envelope Analysis: Particularly useful for detecting bearing faults, this method focuses on the high-frequency components of the vibration signal, which can indicate early-stage defects.
The Benefits of Vibration Monitoring in Predictive Maintenance
Implementing vibration monitoring as part of a predictive maintenance strategy offers numerous benefits to industrial operations. These advantages include improved machine reliability, reduced maintenance costs, and enhanced safety.
Improved Machine Reliability
By continuously monitoring the vibrational behavior of machinery, maintenance teams can identify and address issues before they escalate into major failures. This proactive approach ensures that machines operate within their optimal parameters, reducing the likelihood of unexpected breakdowns and extending the equipment’s operational life.
Cost Reduction
Predictive maintenance, supported by vibration monitoring, can significantly reduce maintenance costs. By identifying issues early, repairs can be scheduled during planned maintenance windows, avoiding the high costs associated with emergency repairs and unplanned downtime. Additionally, by preventing catastrophic failures, companies can avoid the expense of replacing damaged components or entire machines.
Enhanced Safety
Machinery failures can pose significant safety risks to workers. By detecting potential issues early, vibration monitoring helps prevent accidents caused by equipment malfunctions. This not only protects employees but also ensures compliance with safety regulations and reduces the risk of costly legal liabilities.
Implementing Vibration Monitoring Systems
To effectively implement vibration monitoring, companies must consider several factors, including the selection of appropriate sensors, data analysis tools, and integration with existing maintenance systems.
Choosing the Right Sensors
The choice of sensors is critical to the success of a vibration monitoring system. Factors to consider include the type of machinery, the operating environment, and the specific issues being monitored. Accelerometers are the most commonly used sensors, but other options, such as velocity sensors and displacement sensors, may be more suitable for certain applications.
Data Analysis and Interpretation
Once vibration data is collected, it must be analyzed to extract meaningful insights. This requires specialized software capable of processing large volumes of data and identifying patterns indicative of potential issues. The software should also provide intuitive visualizations and reporting tools to aid in decision-making.
Integration with Maintenance Systems
For maximum effectiveness, vibration monitoring should be integrated with existing maintenance management systems. This integration allows for seamless communication between monitoring tools and maintenance teams, ensuring that identified issues are promptly addressed. It also facilitates the tracking of maintenance activities and the evaluation of the effectiveness of predictive maintenance strategies.
Challenges and Considerations
While vibration monitoring offers significant benefits, there are challenges and considerations that companies must address to ensure successful implementation.
Data Overload
The continuous collection of vibration data can result in large volumes of information that must be managed and analyzed. Companies need to invest in robust data management systems and ensure that maintenance teams are trained to interpret the data effectively.
Initial Investment
Implementing a vibration monitoring system requires an initial investment in sensors, software, and training. While the long-term benefits often outweigh these costs, companies must carefully evaluate their budget and resources before proceeding.
Customization and Scalability
Each industrial operation is unique, and vibration monitoring systems must be tailored to meet specific needs. Companies should work with experienced providers to customize their systems and ensure scalability as their operations grow or change.
Conclusion
Vibration monitoring plays a crucial role in the predictive maintenance of industrial machines, offering a proactive approach to identifying and addressing potential issues. By leveraging this technology, companies can improve machine reliability, reduce maintenance costs, and enhance safety. While challenges exist, careful planning and implementation can help organizations realize the full benefits of vibration monitoring, ultimately leading to more efficient and cost-effective operations.