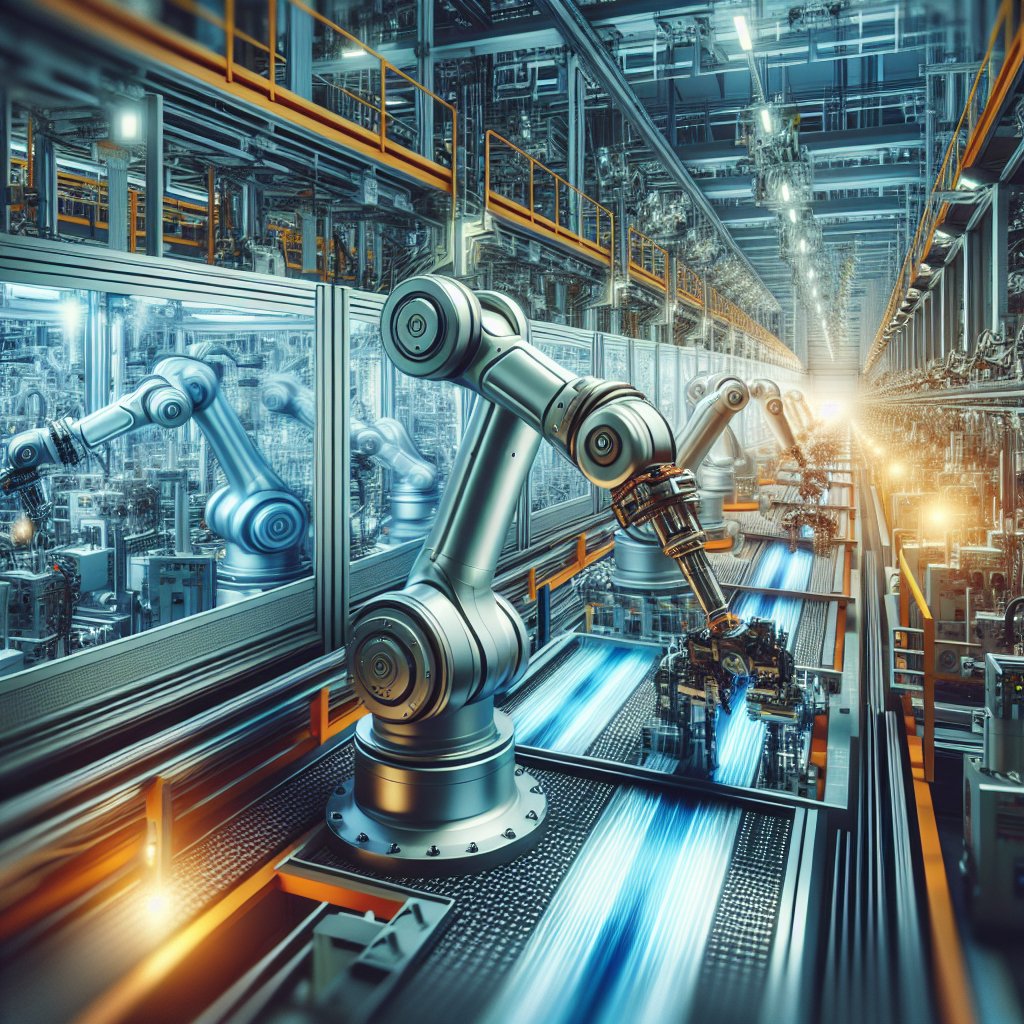
In the ever-evolving landscape of industrial operations, the integration of robotics has emerged as a pivotal strategy for minimizing downtime in machinery. As industries strive for greater efficiency and productivity, the role of robotics in maintaining seamless operations cannot be overstated. This article delves into the multifaceted ways in which robotics is revolutionizing industrial machinery, ensuring that downtime is not just reduced but strategically managed.
Understanding Downtime in Industrial Machinery
Downtime in industrial settings refers to periods when machinery is not operational, leading to potential losses in productivity and revenue. This can be caused by various factors, including equipment failure, maintenance activities, or unexpected breakdowns. The impact of downtime is significant, often resulting in delayed production schedules, increased operational costs, and a ripple effect on supply chains.
Traditionally, industries have relied on preventive maintenance schedules and manual inspections to mitigate downtime. However, these methods are not foolproof and often lead to unnecessary maintenance or missed signs of impending failure. This is where robotics comes into play, offering a more precise and efficient approach to managing industrial machinery.
The Integration of Robotics in Industrial Maintenance
Robotics technology has advanced significantly, providing industries with tools that can perform complex tasks with precision and consistency. In the context of industrial maintenance, robots are being utilized for tasks such as inspection, diagnostics, and even repair. These robotic systems are equipped with sensors and artificial intelligence, enabling them to detect anomalies and predict potential failures before they occur.
One of the key advantages of using robotics in maintenance is the ability to perform tasks without halting production. For instance, robotic arms can inspect machinery components while the equipment is still operational, reducing the need for complete shutdowns. This not only minimizes downtime but also enhances the overall efficiency of maintenance operations.
Predictive Maintenance and Robotics
Predictive maintenance is a proactive approach that uses data analysis and machine learning to predict when equipment is likely to fail. Robotics plays a crucial role in this strategy by collecting real-time data from machinery and analyzing it to identify patterns and trends. This data-driven approach allows industries to schedule maintenance activities at the most opportune times, avoiding unexpected breakdowns and reducing downtime.
Robots equipped with advanced sensors can monitor various parameters such as temperature, vibration, and pressure, providing valuable insights into the health of machinery. By continuously analyzing this data, predictive maintenance systems can alert operators to potential issues, allowing for timely interventions and reducing the risk of catastrophic failures.
Case Studies: Robotics in Action
Several industries have successfully implemented robotics to reduce downtime and improve operational efficiency. In the automotive sector, for example, robotic systems are used for tasks such as welding, painting, and assembly. These robots operate with high precision and speed, ensuring consistent quality and minimizing the need for rework.
In the oil and gas industry, robotics is used for inspecting pipelines and offshore platforms. These environments are often hazardous for human workers, making robots an ideal solution for performing inspections and maintenance tasks. By using robots, companies can reduce the risk of accidents and ensure that maintenance activities are carried out efficiently.
Challenges and Future Prospects
While the benefits of robotics in reducing downtime are clear, there are challenges that industries must address. The initial investment in robotic systems can be significant, and there is a need for skilled personnel to operate and maintain these technologies. Additionally, integrating robotics with existing systems and processes can be complex, requiring careful planning and execution.
Despite these challenges, the future of robotics in industrial maintenance looks promising. Advances in artificial intelligence and machine learning are expected to enhance the capabilities of robotic systems, making them even more effective in reducing downtime. As industries continue to embrace digital transformation, the role of robotics in ensuring seamless operations will only grow in importance.
In conclusion, the integration of robotics in industrial machinery is a game-changer for reducing downtime and enhancing productivity. By leveraging the power of robotics, industries can achieve greater efficiency, reduce operational costs, and maintain a competitive edge in the global market. As technology continues to evolve, the potential for robotics to revolutionize industrial operations is limitless.