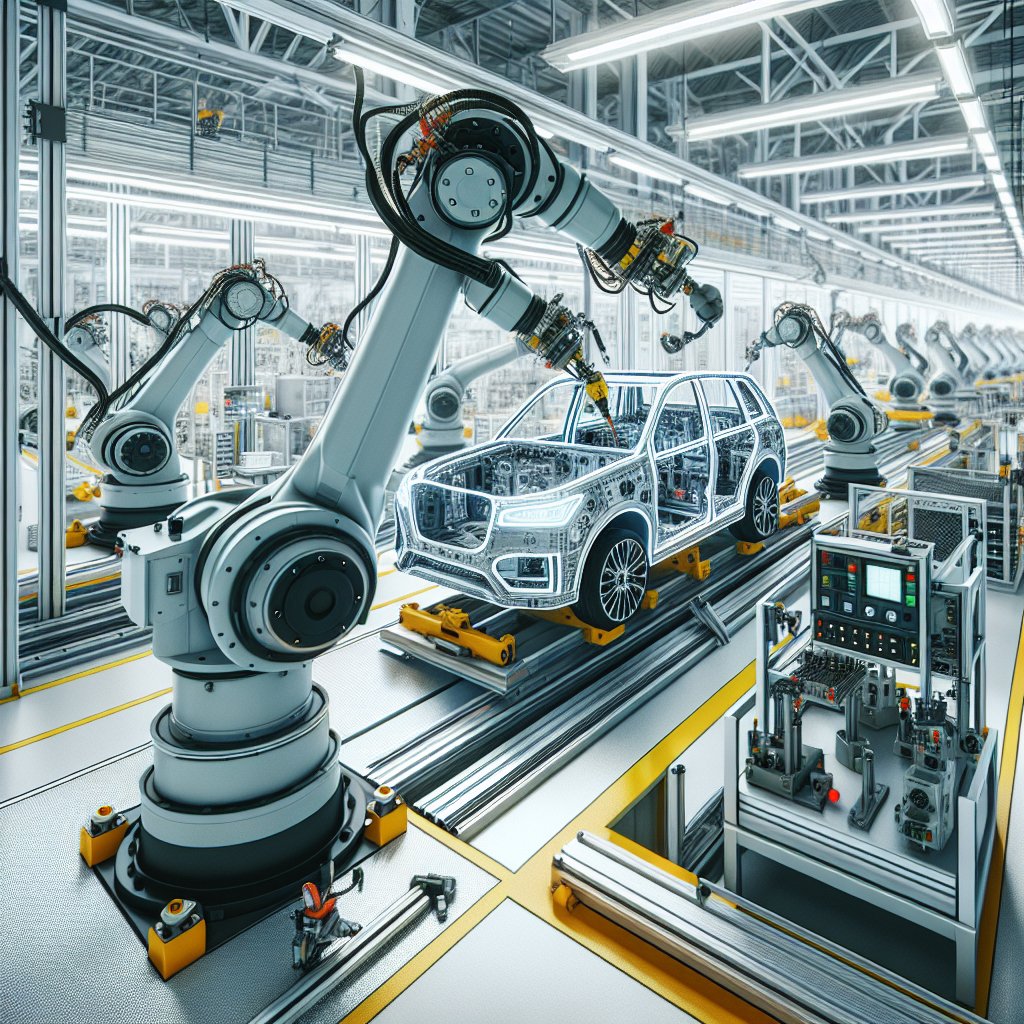
Industrial robots have become a cornerstone in the automotive industry, revolutionizing the way vehicles are manufactured and assembled. These advanced machines have not only increased efficiency and precision but have also significantly impacted the industry’s economic and labor dynamics. This article delves into the multifaceted role of industrial robots in the automotive sector, exploring their contributions to production processes, quality control, and the future of automotive manufacturing.
The Evolution of Industrial Robots in Automotive Manufacturing
The integration of industrial robots into the automotive industry dates back to the 1960s, with the introduction of the Unimate, the first industrial robot used by General Motors. This marked the beginning of a technological transformation that would reshape the manufacturing landscape. Over the decades, the capabilities of industrial robots have evolved dramatically, driven by advancements in technology and the increasing demand for efficiency and precision in automotive production.
Initially, robots were primarily used for tasks such as welding and painting, which required repetitive precision and posed safety risks to human workers. As technology advanced, so did the versatility of these machines. Modern industrial robots are now capable of performing a wide range of tasks, from assembly and material handling to quality inspection and testing. This evolution has been facilitated by improvements in robotics technology, including enhanced sensors, artificial intelligence, and machine learning algorithms, which have expanded the scope of tasks that robots can perform autonomously.
Key Milestones in Robotics Integration
- 1960s: Introduction of the Unimate robot for welding tasks at General Motors.
- 1980s: Expansion of robotic applications to include painting and assembly tasks.
- 2000s: Integration of advanced sensors and AI, enabling more complex and precise operations.
- 2010s: Adoption of collaborative robots (cobots) that work alongside human workers.
These milestones highlight the progressive integration of robotics into automotive manufacturing, underscoring the industry’s commitment to innovation and efficiency.
Impact on Production Efficiency and Quality
The deployment of industrial robots in the automotive industry has led to significant improvements in production efficiency and product quality. Robots are capable of operating 24/7 without fatigue, which allows for continuous production and increased output. This capability is particularly beneficial in meeting the high demand for vehicles in global markets.
Moreover, robots excel in performing tasks with high precision and consistency, reducing the likelihood of errors and defects. This precision is crucial in the automotive industry, where even minor defects can lead to significant safety concerns and financial losses. By minimizing human error and ensuring consistent quality, robots contribute to the production of safer and more reliable vehicles.
Enhancing Quality Control
In addition to improving production efficiency, industrial robots play a vital role in quality control processes. Equipped with advanced sensors and imaging technologies, robots can perform detailed inspections of components and assemblies, identifying defects that may be invisible to the human eye. This capability ensures that only components meeting the highest quality standards are used in vehicle assembly, further enhancing the overall quality and safety of the final product.
Furthermore, the data collected by robots during inspections can be analyzed to identify patterns and trends, enabling manufacturers to address potential quality issues proactively. This data-driven approach to quality control not only improves product quality but also reduces waste and lowers production costs.
The Economic and Labor Implications
The widespread adoption of industrial robots in the automotive industry has significant economic and labor implications. On the one hand, robots have contributed to increased productivity and competitiveness, enabling manufacturers to produce vehicles more efficiently and at a lower cost. This increased efficiency has allowed automotive companies to remain competitive in a global market characterized by intense competition and rapidly changing consumer preferences.
On the other hand, the integration of robots has raised concerns about the impact on employment in the automotive sector. While robots have replaced some manual labor tasks, they have also created new opportunities for skilled workers in areas such as robot programming, maintenance, and supervision. The shift towards automation has necessitated a re-skilling of the workforce, with an emphasis on technical skills and expertise in robotics and automation technologies.
Balancing Automation and Employment
To address the challenges posed by automation, many automotive companies are investing in training and development programs to equip their workforce with the skills needed to thrive in an increasingly automated environment. These programs focus on developing technical skills, such as programming and maintenance, as well as soft skills, such as problem-solving and critical thinking, which are essential for working alongside advanced robotic systems.
Moreover, the rise of collaborative robots, or cobots, has opened up new possibilities for human-robot collaboration. Unlike traditional industrial robots, which operate in isolated environments, cobots are designed to work alongside human workers, enhancing productivity and safety. This collaborative approach allows for a more balanced integration of automation and human labor, preserving jobs while leveraging the benefits of robotic technology.
The Future of Robotics in the Automotive Industry
As technology continues to advance, the role of industrial robots in the automotive industry is expected to expand further. Emerging technologies such as artificial intelligence, machine learning, and the Internet of Things (IoT) are poised to enhance the capabilities of robots, enabling them to perform even more complex tasks with greater autonomy and intelligence.
In the future, we can expect to see increased integration of robots in areas such as autonomous vehicle production, where precision and reliability are paramount. Additionally, the development of smart factories, where robots and other automated systems are interconnected and communicate seamlessly, will further enhance production efficiency and flexibility.
Challenges and Opportunities
While the future of robotics in the automotive industry holds great promise, it also presents challenges that must be addressed. Ensuring the security and reliability of interconnected robotic systems is a critical concern, as is the need to address ethical considerations related to automation and employment.
Nevertheless, the continued evolution of robotics technology presents significant opportunities for innovation and growth in the automotive industry. By embracing these advancements, manufacturers can enhance their competitiveness, improve product quality, and contribute to a more sustainable and efficient automotive ecosystem.
In conclusion, industrial robots have become an integral part of the automotive industry, driving improvements in efficiency, quality, and competitiveness. As technology continues to evolve, the role of robots in automotive manufacturing is set to expand, offering new opportunities and challenges for the industry. By embracing these changes and investing in the development of their workforce, automotive companies can position themselves for success in an increasingly automated and interconnected world.