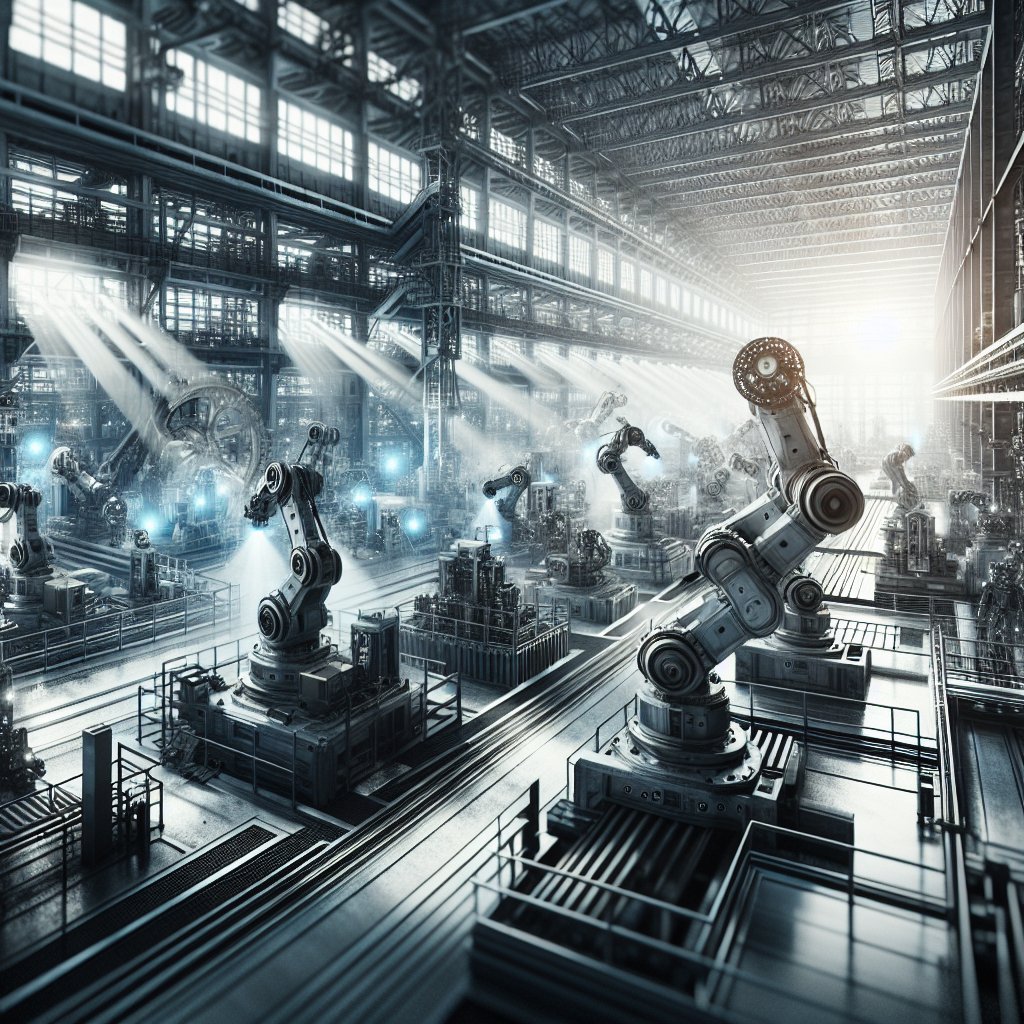
Industrial robots have become a cornerstone in enhancing efficiency within the heavy industry sector. As technology continues to advance, these robotic systems are increasingly being integrated into various industrial processes, offering numerous benefits such as improved precision, reduced labor costs, and enhanced safety. This article delves into the multifaceted role of industrial robots in heavy industry, exploring their impact on productivity and the future of industrial operations.
Understanding Industrial Robots
Industrial robots are automated, programmable machines capable of performing a wide range of tasks with high precision and consistency. These robots are designed to handle repetitive and labor-intensive tasks, which are often hazardous or unsuitable for human workers. In heavy industries such as automotive, aerospace, and metal manufacturing, industrial robots are employed to perform tasks like welding, painting, assembly, and material handling.
The development of industrial robots dates back to the mid-20th century, with the introduction of the first programmable robot, Unimate, in 1961. Since then, the technology has evolved significantly, with modern robots featuring advanced sensors, artificial intelligence, and machine learning capabilities. These advancements have enabled robots to perform complex tasks with minimal human intervention, thereby increasing efficiency and productivity in industrial settings.
Enhancing Efficiency in Heavy Industry
One of the primary benefits of industrial robots in heavy industry is their ability to enhance operational efficiency. By automating repetitive and time-consuming tasks, robots allow human workers to focus on more strategic and value-added activities. This shift not only improves productivity but also leads to better resource allocation and cost savings.
Moreover, industrial robots are capable of operating 24/7 without fatigue, which significantly boosts production rates. In industries where demand fluctuates, robots provide the flexibility to scale operations up or down quickly, ensuring that production meets market needs without incurring additional labor costs. This adaptability is particularly valuable in sectors like automotive manufacturing, where production schedules can change rapidly based on consumer demand.
Improving Quality and Precision
Another critical advantage of industrial robots is their ability to deliver consistent quality and precision in manufacturing processes. Human workers, despite their skills and experience, are prone to errors, especially when performing repetitive tasks over extended periods. In contrast, robots can execute tasks with high accuracy and repeatability, ensuring that products meet stringent quality standards.
For instance, in the aerospace industry, where precision is paramount, robots are used for tasks such as drilling and fastening, which require exact measurements and alignment. By minimizing errors and reducing variability in production, robots help maintain product quality and reduce waste, leading to significant cost savings for manufacturers.
Enhancing Workplace Safety
Safety is a major concern in heavy industries, where workers are often exposed to hazardous environments and tasks. Industrial robots play a crucial role in enhancing workplace safety by taking over dangerous and physically demanding jobs. By reducing the need for human intervention in high-risk areas, robots help prevent workplace accidents and injuries.
For example, in the metal manufacturing industry, robots are used for tasks such as welding and cutting, which involve exposure to high temperatures and harmful fumes. By automating these processes, companies can protect their workers from potential health hazards while maintaining high production standards.
Challenges and Considerations
Despite the numerous benefits of industrial robots, their integration into heavy industry is not without challenges. One of the primary concerns is the high initial cost of acquiring and implementing robotic systems. For small and medium-sized enterprises, this investment can be prohibitive, limiting their ability to adopt automation technologies.
Additionally, the deployment of industrial robots requires significant changes to existing workflows and infrastructure. Companies must invest in training and upskilling their workforce to ensure that employees can effectively operate and maintain robotic systems. This transition can be complex and time-consuming, requiring careful planning and management.
Another consideration is the potential impact on employment. While robots can take over repetitive and hazardous tasks, there is a concern that widespread automation could lead to job displacement. However, many experts argue that robots will create new opportunities for skilled workers, particularly in areas such as robot maintenance, programming, and system integration.
The Future of Industrial Robots in Heavy Industry
As technology continues to evolve, the role of industrial robots in heavy industry is expected to expand further. Advances in artificial intelligence and machine learning are enabling robots to perform increasingly complex tasks, such as quality inspection and predictive maintenance. These capabilities will allow companies to optimize their operations and improve decision-making processes.
Furthermore, the development of collaborative robots, or cobots, is opening new possibilities for human-robot interaction. Unlike traditional industrial robots, which operate in isolated environments, cobots are designed to work alongside human workers, enhancing productivity and efficiency. This collaboration is expected to drive innovation and growth in heavy industries, leading to more agile and responsive manufacturing processes.
In conclusion, industrial robots are playing a pivotal role in transforming heavy industry by increasing efficiency, improving quality, and enhancing safety. While challenges remain, the continued advancement of robotic technologies promises to unlock new opportunities and drive the future of industrial operations. As companies navigate this evolving landscape, the successful integration of robots will be key to maintaining competitiveness and achieving long-term success.