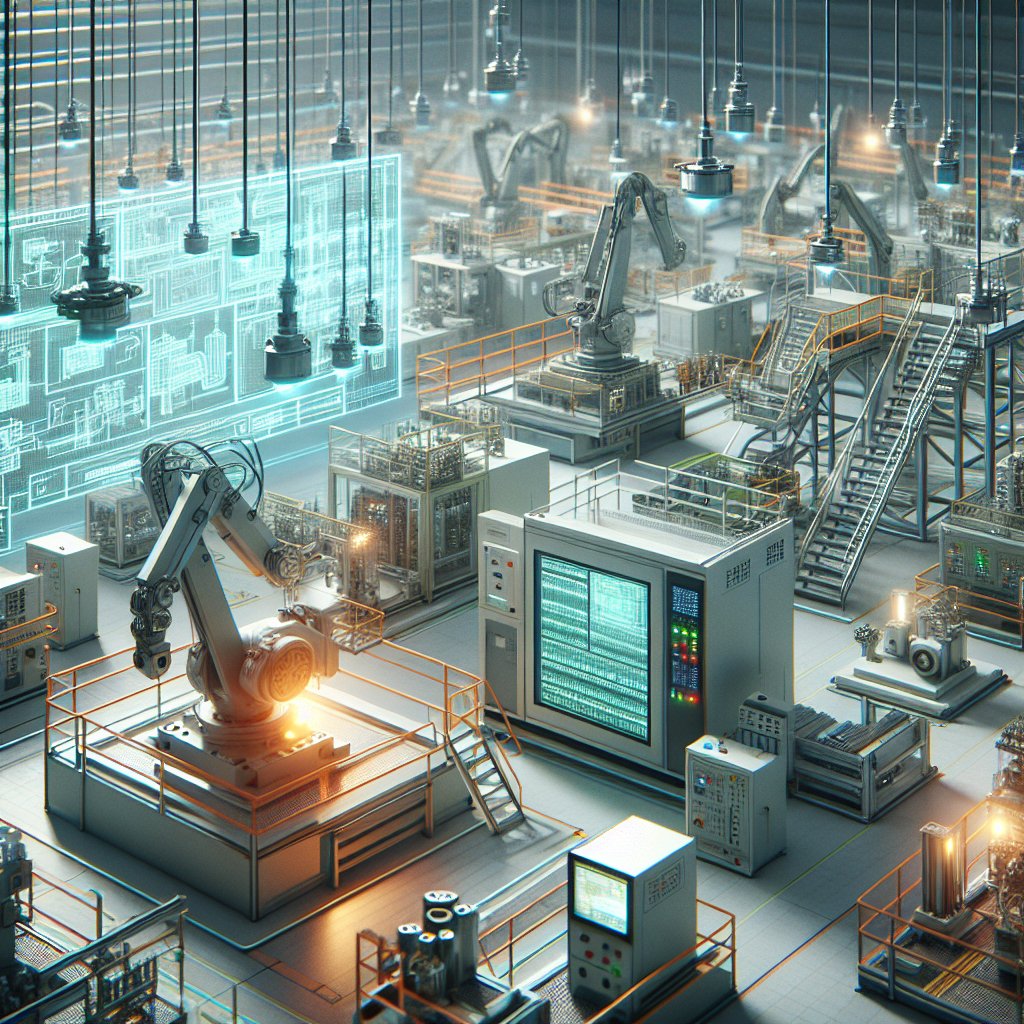
Industrial Programmable Logic Controllers (PLCs) have become a cornerstone in the realm of automated manufacturing systems, revolutionizing the way industries operate by enhancing efficiency, precision, and reliability. As the demand for automation continues to surge, understanding the role of PLCs in this transformation is crucial for businesses aiming to stay competitive in the modern industrial landscape.
Understanding Industrial PLCs
At the heart of automated manufacturing systems lies the Industrial Programmable Logic Controller, a specialized computer designed to manage and control complex industrial processes. Unlike traditional computers, PLCs are built to withstand harsh industrial environments, offering robust performance in conditions that include extreme temperatures, dust, and vibrations. Their primary function is to automate machinery and processes, reducing the need for human intervention and minimizing the risk of errors.
PLCs are equipped with a variety of input and output modules that allow them to interact with sensors and actuators on the factory floor. These modules enable PLCs to receive data from the environment, process it according to pre-programmed instructions, and execute commands that control machinery and equipment. This capability makes PLCs indispensable in industries ranging from automotive manufacturing to food processing, where precision and reliability are paramount.
Components of a PLC
A typical PLC system comprises several key components, each playing a vital role in its operation:
- Central Processing Unit (CPU): The brain of the PLC, responsible for executing control instructions and managing data flow.
- Input/Output Modules: Interfaces that connect the PLC to external devices, allowing it to receive and send signals.
- Power Supply: Provides the necessary electrical power to the PLC and its components.
- Programming Device: Used to write and upload control programs to the PLC.
- Communication Interfaces: Enable the PLC to communicate with other systems and devices, facilitating data exchange and integration.
The Impact of PLCs on Manufacturing Efficiency
The integration of PLCs into manufacturing systems has led to significant improvements in efficiency and productivity. By automating repetitive and complex tasks, PLCs reduce the time and labor required to produce goods, allowing manufacturers to increase output without compromising quality. This automation also leads to more consistent production processes, minimizing variability and ensuring that products meet stringent quality standards.
Moreover, PLCs offer unparalleled flexibility in manufacturing operations. With the ability to quickly reprogram and adapt to new tasks, PLCs enable manufacturers to respond swiftly to changing market demands and production requirements. This adaptability is particularly valuable in industries where product lifecycles are short, and customization is key to maintaining a competitive edge.
Enhancing Safety and Reliability
In addition to boosting efficiency, PLCs play a critical role in enhancing the safety and reliability of manufacturing systems. By continuously monitoring processes and equipment, PLCs can detect anomalies and initiate corrective actions to prevent accidents and equipment failures. This proactive approach to safety not only protects workers and assets but also reduces downtime and maintenance costs.
Furthermore, the reliability of PLCs ensures that manufacturing operations run smoothly and without interruption. With built-in redundancy and fail-safe mechanisms, PLCs can maintain control even in the event of component failures, providing manufacturers with peace of mind and confidence in their production capabilities.
Future Trends in PLC Technology
As technology continues to evolve, so too does the role of PLCs in automated manufacturing systems. Emerging trends such as the Industrial Internet of Things (IIoT), artificial intelligence, and machine learning are poised to further enhance the capabilities of PLCs, enabling even greater levels of automation and efficiency.
The integration of IIoT technologies with PLCs allows for real-time data collection and analysis, providing manufacturers with valuable insights into their operations. This data-driven approach enables predictive maintenance, optimizing equipment performance and reducing the likelihood of unexpected breakdowns. Additionally, the use of AI and machine learning algorithms can enhance the decision-making capabilities of PLCs, allowing them to adapt to changing conditions and optimize processes autonomously.
Challenges and Opportunities
While the future of PLC technology is promising, it also presents challenges that manufacturers must address. The increasing complexity of automated systems requires skilled personnel to design, program, and maintain PLCs, highlighting the need for ongoing training and education in the workforce. Additionally, as PLCs become more interconnected, cybersecurity becomes a critical concern, necessitating robust measures to protect sensitive data and prevent unauthorized access.
Despite these challenges, the opportunities presented by advanced PLC technology are immense. By embracing these innovations, manufacturers can achieve unprecedented levels of efficiency, flexibility, and competitiveness, positioning themselves for success in an increasingly automated world.
In conclusion, industrial PLCs are integral to the advancement of automated manufacturing systems, offering a myriad of benefits that enhance efficiency, safety, and reliability. As technology continues to evolve, the role of PLCs will undoubtedly expand, driving further innovation and transformation in the manufacturing industry.