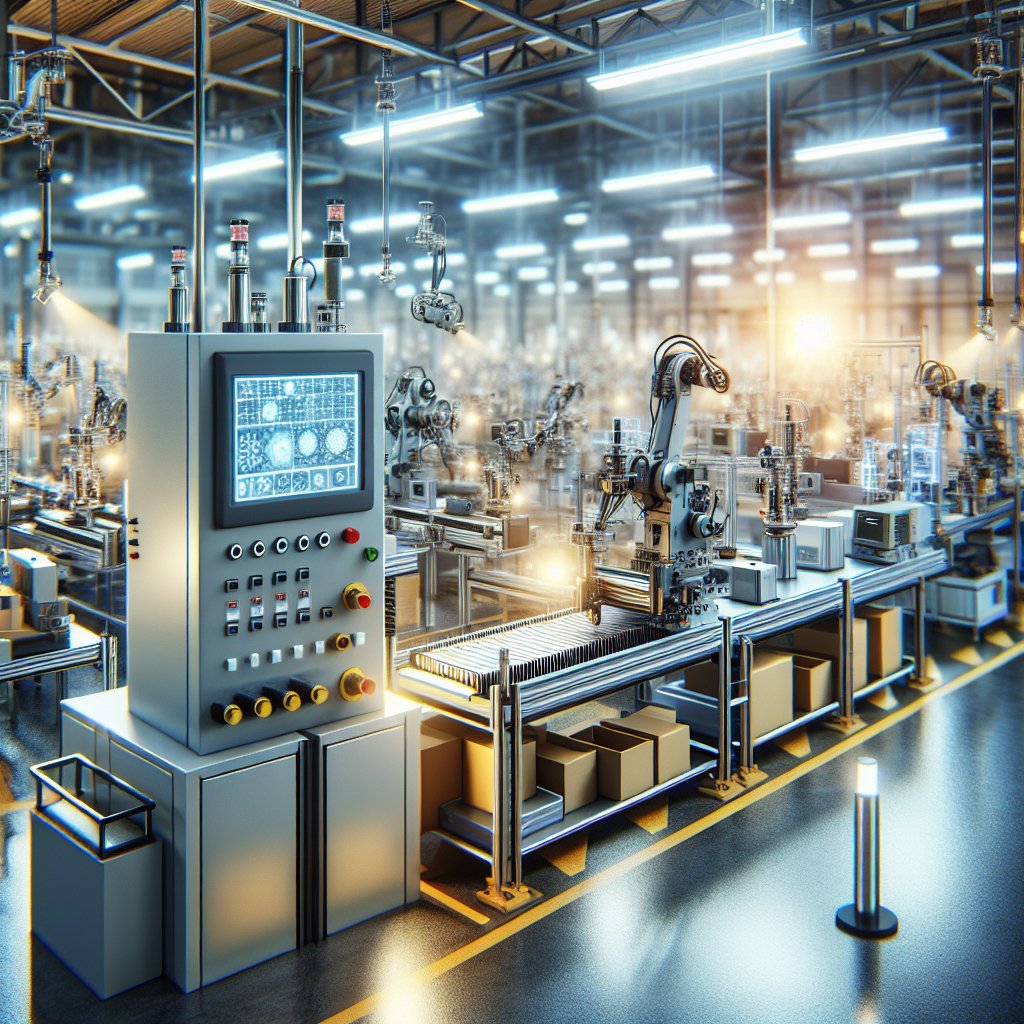
Industrial machine vision systems have become a cornerstone in the realm of quality control, revolutionizing the way industries ensure product excellence. These systems, which utilize advanced imaging technologies, are designed to inspect, analyze, and interpret visual data, providing unparalleled accuracy and efficiency in detecting defects and ensuring compliance with quality standards. As industries strive for higher precision and reduced error margins, the integration of machine vision systems has become indispensable.
Understanding Machine Vision Systems
Machine vision systems are sophisticated assemblies that combine hardware and software to emulate human vision capabilities. At their core, these systems consist of cameras, lighting, processors, and software algorithms that work in tandem to capture and analyze images. The primary objective is to automate the inspection process, reducing human error and increasing throughput.
The hardware components, such as cameras and lighting, are crucial for capturing high-quality images. Cameras are selected based on the resolution and speed required for specific applications, while lighting is tailored to enhance image clarity and highlight defects. The software component, on the other hand, is responsible for processing the captured images. It employs algorithms to identify patterns, measure dimensions, and detect anomalies, ensuring that only products meeting the desired specifications proceed to the next stage of production.
One of the key advantages of machine vision systems is their ability to operate continuously and consistently, without the fatigue or variability associated with human inspectors. This reliability is particularly beneficial in high-volume production environments, where even minor defects can lead to significant financial losses or safety hazards.
Applications in Quality Control
Machine vision systems are employed across a wide range of industries, each with unique quality control requirements. In the automotive industry, for example, these systems are used to inspect components such as engine parts, ensuring they meet stringent safety and performance standards. By detecting defects early in the production process, manufacturers can prevent costly recalls and maintain their reputation for quality.
In the electronics industry, machine vision systems play a critical role in inspecting printed circuit boards (PCBs). These systems can identify issues such as misaligned components, soldering defects, and surface blemishes, which could otherwise lead to device malfunctions. The precision offered by machine vision systems ensures that only flawless products reach consumers, enhancing brand trust and customer satisfaction.
The food and beverage industry also benefits significantly from machine vision technology. Here, systems are used to inspect packaging, check fill levels, and verify labels, ensuring compliance with regulatory standards and preventing contamination. By automating these processes, companies can maintain high levels of hygiene and quality, safeguarding consumer health.
Technological Advancements and Future Trends
The field of machine vision is continuously evolving, driven by advancements in technology and increasing demands for quality assurance. One of the most significant developments is the integration of artificial intelligence (AI) and machine learning (ML) into vision systems. These technologies enable systems to learn from data, improving their accuracy and adaptability over time. AI-powered vision systems can identify complex patterns and make decisions based on historical data, offering a level of insight that was previously unattainable.
Another trend is the miniaturization of components, which allows for the development of compact and portable vision systems. This is particularly beneficial for industries with space constraints or those requiring mobile inspection solutions. Additionally, the rise of the Internet of Things (IoT) has facilitated the connectivity of machine vision systems, enabling real-time data sharing and remote monitoring. This connectivity enhances decision-making processes and allows for predictive maintenance, reducing downtime and improving overall efficiency.
As these technologies continue to advance, the potential applications of machine vision systems in quality control are expected to expand. Industries will increasingly rely on these systems to meet the growing demands for precision, speed, and reliability, ensuring that they remain competitive in a rapidly changing market.
Challenges and Considerations
Despite their numerous advantages, implementing machine vision systems in quality control is not without challenges. One of the primary considerations is the initial cost of installation and integration. High-quality cameras, lighting, and processing units can be expensive, and the complexity of the systems may require specialized training for operators. However, the long-term benefits, such as reduced labor costs and improved product quality, often justify the investment.
Another challenge is the need for customization. Each industry and application may require specific configurations and algorithms to address unique inspection requirements. This necessitates a thorough understanding of the production process and close collaboration with system providers to develop tailored solutions.
Moreover, maintaining and updating machine vision systems can be complex. As technology evolves, companies must ensure that their systems remain up-to-date to leverage the latest advancements. This may involve regular software updates, hardware upgrades, and ongoing training for personnel.
Conclusion
Industrial machine vision systems have transformed quality control processes across various industries, offering unparalleled accuracy, efficiency, and reliability. As technology continues to advance, these systems will become even more integral to production lines, helping companies meet the ever-increasing demands for quality and precision. While challenges exist, the benefits of machine vision systems far outweigh the drawbacks, making them a vital component of modern manufacturing and quality assurance strategies.