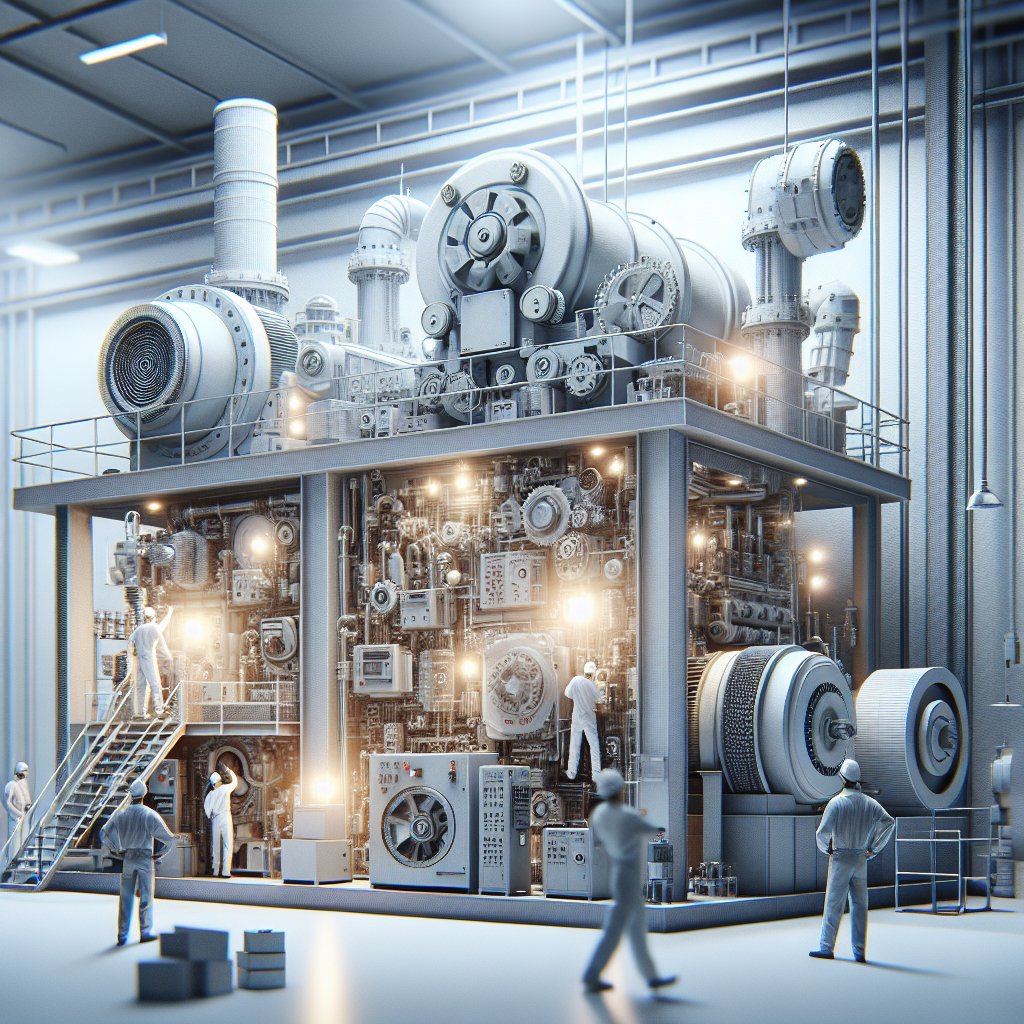
Condition monitoring has emerged as a pivotal strategy in reducing industrial equipment failure, offering a proactive approach to maintenance and operational efficiency. As industries strive to minimize downtime and optimize performance, the integration of condition monitoring systems has become increasingly essential. This article delves into the significance of condition monitoring, exploring its methodologies, benefits, and the transformative impact it has on industrial operations.
Understanding Condition Monitoring
Condition monitoring refers to the process of continuously observing and analyzing the state of machinery and equipment to detect signs of wear, malfunction, or potential failure. By employing various techniques and technologies, industries can gather real-time data on equipment performance, enabling timely interventions and maintenance actions. This proactive approach not only extends the lifespan of machinery but also enhances safety and productivity.
Techniques and Technologies
Several techniques are employed in condition monitoring, each tailored to specific types of equipment and operational requirements. Vibration analysis, for instance, is widely used to assess the mechanical condition of rotating machinery. By measuring and analyzing vibration patterns, technicians can identify imbalances, misalignments, or bearing failures before they escalate into major issues.
Another common technique is thermography, which involves using infrared cameras to detect temperature variations in equipment. Abnormal heat patterns can indicate electrical faults, friction, or lubrication issues, allowing for early intervention. Additionally, oil analysis is a valuable tool for monitoring the condition of lubricants and identifying contaminants or wear particles that may signal impending equipment failure.
Advancements in technology have further enhanced condition monitoring capabilities. The integration of Internet of Things (IoT) devices and sensors enables continuous data collection and remote monitoring. This real-time data is then analyzed using sophisticated algorithms and machine learning models, providing actionable insights and predictive maintenance recommendations.
Benefits of Condition Monitoring
The implementation of condition monitoring systems offers a multitude of benefits for industrial operations. One of the most significant advantages is the reduction in unplanned downtime. By identifying potential issues before they lead to equipment failure, industries can schedule maintenance activities during planned shutdowns, minimizing disruptions to production schedules.
Moreover, condition monitoring contributes to cost savings by optimizing maintenance practices. Traditional maintenance approaches often rely on fixed schedules, leading to unnecessary part replacements or repairs. In contrast, condition-based maintenance ensures that interventions are performed only when necessary, reducing material and labor costs.
Enhanced safety is another critical benefit of condition monitoring. By detecting anomalies and addressing them promptly, the risk of catastrophic equipment failures and associated accidents is significantly reduced. This not only protects the workforce but also safeguards the environment and surrounding communities.
Impact on Operational Efficiency
Condition monitoring plays a crucial role in improving overall operational efficiency. By maintaining equipment in optimal condition, industries can achieve higher levels of productivity and output quality. The ability to predict and prevent failures also enhances the reliability of production processes, fostering customer trust and satisfaction.
Furthermore, the data collected through condition monitoring provides valuable insights into equipment performance and operational trends. This information can be leveraged to optimize processes, identify areas for improvement, and drive innovation. As a result, industries can achieve greater competitiveness and sustainability in an ever-evolving market landscape.
Challenges and Future Directions
Despite its numerous benefits, the implementation of condition monitoring systems is not without challenges. One of the primary obstacles is the initial investment required for equipment and technology. However, the long-term cost savings and operational improvements often justify this expenditure.
Another challenge lies in the integration of condition monitoring systems with existing infrastructure and processes. Industries must ensure seamless data flow and compatibility with other systems to maximize the effectiveness of condition monitoring efforts. Additionally, the interpretation of data and the development of accurate predictive models require skilled personnel and advanced analytical tools.
Looking ahead, the future of condition monitoring is promising, with ongoing advancements in technology and data analytics. The integration of artificial intelligence and machine learning is expected to further enhance predictive capabilities, enabling even more precise maintenance strategies. As industries continue to embrace digital transformation, condition monitoring will play an increasingly vital role in achieving operational excellence and sustainability.
In conclusion, condition monitoring is a transformative approach that empowers industries to proactively manage equipment health and performance. By leveraging advanced techniques and technologies, businesses can reduce equipment failure, optimize maintenance practices, and enhance overall operational efficiency. As the industrial landscape evolves, the adoption of condition monitoring will be instrumental in driving innovation and competitiveness.