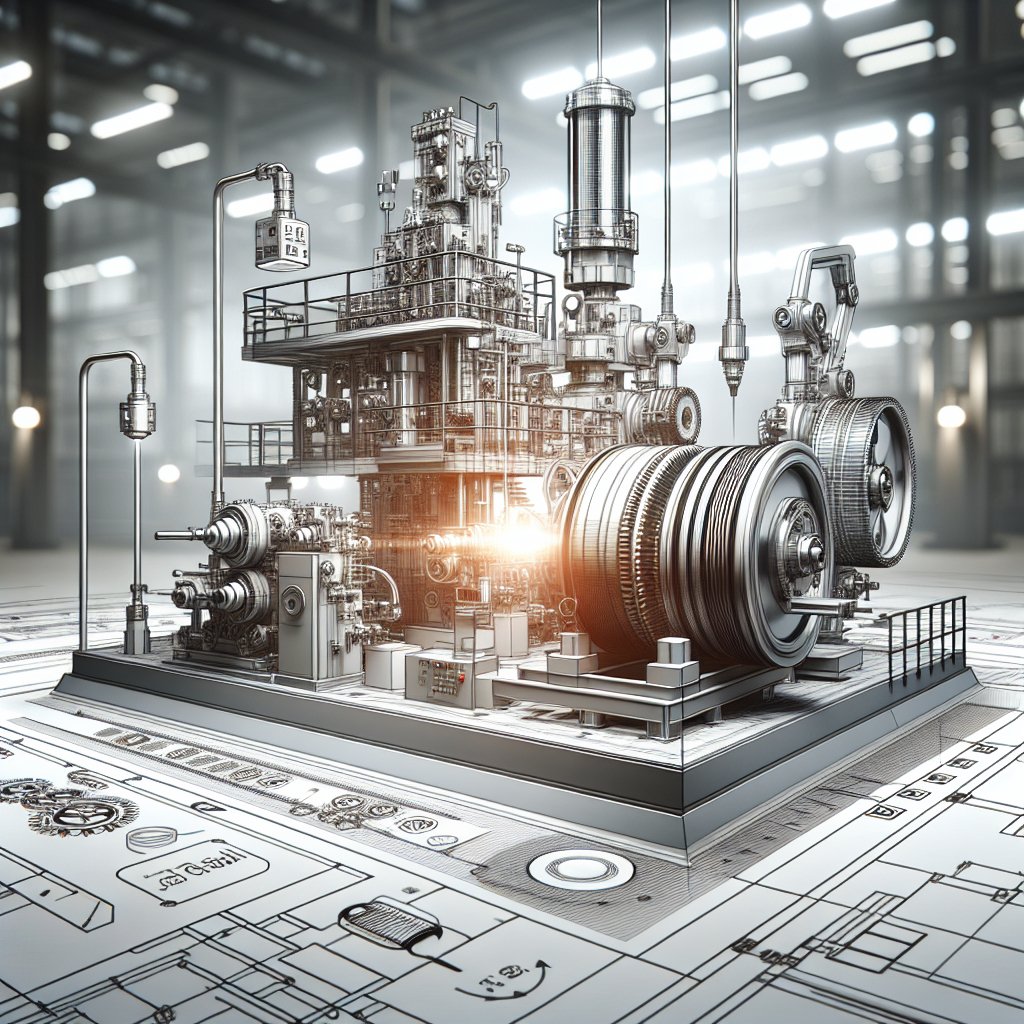
Lubrication systems play a crucial role in the efficient operation and longevity of industrial machinery. These systems are designed to reduce friction between moving parts, minimize wear and tear, and prevent overheating, thereby ensuring that machines run smoothly and efficiently. In this article, we will explore the importance of lubrication systems in industrial machinery, examining their components, types, and the benefits they offer to various industries.
Understanding Lubrication Systems
Lubrication systems are integral to the maintenance and operation of industrial machinery. They are engineered to deliver the right amount of lubricant to the right place at the right time. This section will delve into the components and types of lubrication systems commonly used in industrial settings.
Components of Lubrication Systems
A typical lubrication system consists of several key components, each playing a vital role in the process of reducing friction and wear. These components include:
- Pumps: Responsible for moving the lubricant through the system, pumps ensure that the lubricant reaches all necessary parts of the machinery.
- Reservoirs: These are storage tanks that hold the lubricant until it is needed. They are designed to keep the lubricant clean and free from contaminants.
- Filters: Filters are used to remove impurities from the lubricant, ensuring that only clean lubricant is circulated through the machinery.
- Valves: Valves control the flow of lubricant, allowing for precise delivery to specific areas of the machinery.
- Distribution Lines: These are the pathways through which the lubricant travels to reach various parts of the machinery.
Types of Lubrication Systems
There are several types of lubrication systems used in industrial machinery, each suited to different applications and machinery types. Some of the most common types include:
- Manual Lubrication Systems: These systems require human intervention to apply lubricant to machinery parts. While simple and cost-effective, they are labor-intensive and may not provide consistent lubrication.
- Automatic Lubrication Systems: These systems automatically deliver lubricant to machinery parts at predetermined intervals. They are more efficient and reliable than manual systems, reducing the risk of human error.
- Centralized Lubrication Systems: In these systems, a central pump supplies lubricant to multiple points in the machinery. This type of system is ideal for large, complex machinery with numerous lubrication points.
- Oil Mist Lubrication Systems: These systems use a fine mist of oil to lubricate machinery parts. They are particularly effective in high-speed applications where traditional lubrication methods may not suffice.
The Benefits of Lubrication Systems
Implementing an effective lubrication system in industrial machinery offers numerous benefits, ranging from improved efficiency to extended equipment lifespan. This section will highlight some of the key advantages of using lubrication systems in industrial settings.
Reduced Friction and Wear
One of the primary functions of a lubrication system is to reduce friction between moving parts. By creating a thin film of lubricant between surfaces, these systems minimize direct contact, thereby reducing wear and tear. This not only extends the lifespan of machinery components but also enhances their performance.
Improved Efficiency
Lubrication systems contribute to the overall efficiency of industrial machinery by ensuring that all moving parts operate smoothly. Reduced friction means less energy is required to move parts, leading to lower energy consumption and operational costs. This improved efficiency can have a significant impact on a company’s bottom line.
Prevention of Overheating
Friction generates heat, which can lead to overheating and potential damage to machinery components. Lubrication systems help dissipate this heat, maintaining optimal operating temperatures and preventing costly breakdowns. By keeping machinery cool, these systems also enhance safety in the workplace.
Extended Equipment Lifespan
Regular and effective lubrication is essential for prolonging the life of industrial machinery. By reducing wear and preventing overheating, lubrication systems help maintain the integrity of machinery components, reducing the need for frequent repairs and replacements. This not only saves money but also minimizes downtime, ensuring that production schedules are met.
Environmental Benefits
Modern lubrication systems are designed with environmental considerations in mind. By reducing energy consumption and minimizing waste, these systems contribute to a company’s sustainability efforts. Additionally, many lubrication systems use biodegradable lubricants, further reducing their environmental impact.
Conclusion
In conclusion, lubrication systems are vital to the efficient operation and maintenance of industrial machinery. By reducing friction, preventing overheating, and extending equipment lifespan, these systems offer numerous benefits to industries worldwide. As technology continues to advance, lubrication systems will undoubtedly play an increasingly important role in the future of industrial machinery, driving efficiency, sustainability, and cost-effectiveness.