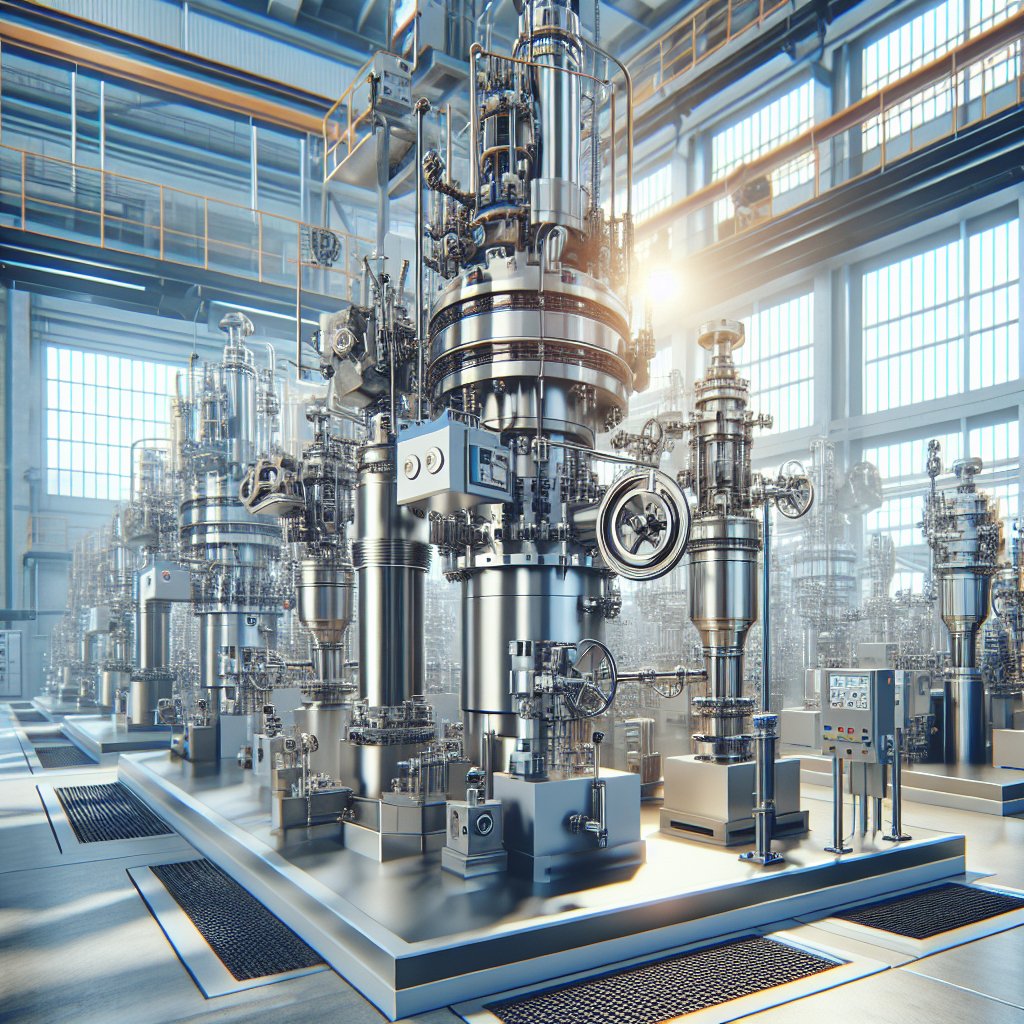
Correct sealing in industrial equipment is a critical aspect that ensures the efficiency, safety, and longevity of machinery used across various sectors. From preventing leaks to maintaining pressure and protecting against contamination, the role of proper sealing cannot be overstated. This article delves into the significance of sealing in industrial applications, exploring the types of seals, their functions, and the consequences of inadequate sealing.
Understanding Industrial Seals
Industrial seals are components designed to prevent the escape of fluids, gases, or other substances from machinery, as well as to keep contaminants from entering. They are essential in maintaining the integrity of equipment and ensuring optimal performance. Seals are used in a wide range of applications, from automotive engines to hydraulic systems, and their design and material composition can vary significantly depending on the specific requirements of the application.
Types of Industrial Seals
There are several types of industrial seals, each serving a unique purpose and suited to different environments and conditions. Some of the most common types include:
- O-Rings: These are circular seals used in static and dynamic applications. They are known for their simplicity and effectiveness in preventing leaks.
- Gaskets: Typically used to fill the space between two or more mating surfaces, gaskets prevent leakage from or into the joined objects while under compression.
- Mechanical Seals: Used in rotating equipment such as pumps and compressors, mechanical seals prevent fluid leakage by creating a seal between the rotating shaft and the stationary pump casing.
- Lip Seals: These are used to retain lubricants and exclude contaminants in rotary shaft applications.
Materials Used in Seals
The choice of material for a seal is crucial, as it must withstand the specific conditions of the application, such as temperature, pressure, and chemical exposure. Common materials include:
- Rubber: Known for its flexibility and resilience, rubber is often used in O-rings and gaskets.
- PTFE (Polytetrafluoroethylene): This material is highly resistant to chemicals and extreme temperatures, making it ideal for harsh environments.
- Metal: Metal seals are used in high-pressure and high-temperature applications where rubber or plastic seals would fail.
- Composite Materials: These combine the properties of different materials to provide enhanced performance in specific applications.
The Role of Sealing in Industrial Equipment
Sealing plays a vital role in the operation and maintenance of industrial equipment. Proper sealing ensures that machinery operates efficiently, safely, and with minimal downtime. Here are some key functions of sealing in industrial applications:
Leak Prevention
One of the primary functions of seals is to prevent leaks. Leaks can lead to significant losses in terms of both materials and energy, and they can also pose safety hazards. For example, in hydraulic systems, leaks can result in a loss of pressure, leading to reduced performance and potential system failure. In chemical processing plants, leaks can lead to hazardous spills, endangering workers and the environment.
Contamination Control
Seals also play a crucial role in preventing contamination. In many industrial processes, it is essential to keep contaminants out to ensure product quality and equipment longevity. For instance, in food and pharmaceutical industries, seals prevent the ingress of dust, dirt, and other contaminants that could compromise product safety and quality.
Pressure Maintenance
In systems where maintaining pressure is critical, such as in gas compressors or hydraulic systems, seals ensure that the pressure is contained within the system. This is essential for the efficient operation of the equipment and to prevent potential hazards associated with pressure loss.
Protection Against Environmental Factors
Seals protect equipment from environmental factors such as moisture, dust, and extreme temperatures. This protection is vital for the longevity and reliability of machinery, especially in outdoor or harsh environments.
Consequences of Inadequate Sealing
Inadequate sealing can have severe consequences for industrial equipment and operations. Some of the potential issues include:
Increased Maintenance and Downtime
Poor sealing can lead to frequent maintenance requirements and unexpected downtime. Leaks and contamination can cause equipment to malfunction, necessitating repairs and leading to production delays.
Reduced Equipment Lifespan
Without proper sealing, equipment is more susceptible to wear and tear, leading to a reduced lifespan. Contaminants can cause corrosion and damage to components, while leaks can result in overheating and mechanical failure.
Safety Hazards
Inadequate sealing can pose significant safety risks. Leaks of hazardous substances can lead to fires, explosions, or exposure to toxic chemicals, endangering workers and the environment.
Increased Operational Costs
The costs associated with inadequate sealing can be substantial. These include the costs of lost materials, energy inefficiencies, increased maintenance, and potential fines or liabilities resulting from safety incidents.
Ensuring Proper Sealing in Industrial Equipment
To ensure proper sealing in industrial equipment, it is essential to consider several factors during the design, installation, and maintenance phases. Here are some best practices:
Material Selection
Choosing the right material for the seal is crucial. Consider the operating conditions, such as temperature, pressure, and chemical exposure, to select a material that will perform effectively and last longer.
Regular Maintenance and Inspection
Regular maintenance and inspection of seals are essential to identify wear and tear early and prevent potential failures. This includes checking for signs of leaks, cracks, or other damage and replacing seals as needed.
Proper Installation
Ensuring that seals are installed correctly is vital for their effectiveness. This includes following manufacturer guidelines and using the appropriate tools and techniques to avoid damaging the seal during installation.
Continuous Monitoring
Implementing continuous monitoring systems can help detect leaks or pressure changes early, allowing for prompt corrective action. This can prevent minor issues from escalating into major problems.
In conclusion, correct sealing in industrial equipment is a fundamental aspect of ensuring efficient, safe, and reliable operations. By understanding the types of seals, their functions, and the consequences of inadequate sealing, industries can take proactive measures to maintain their equipment and optimize their processes.