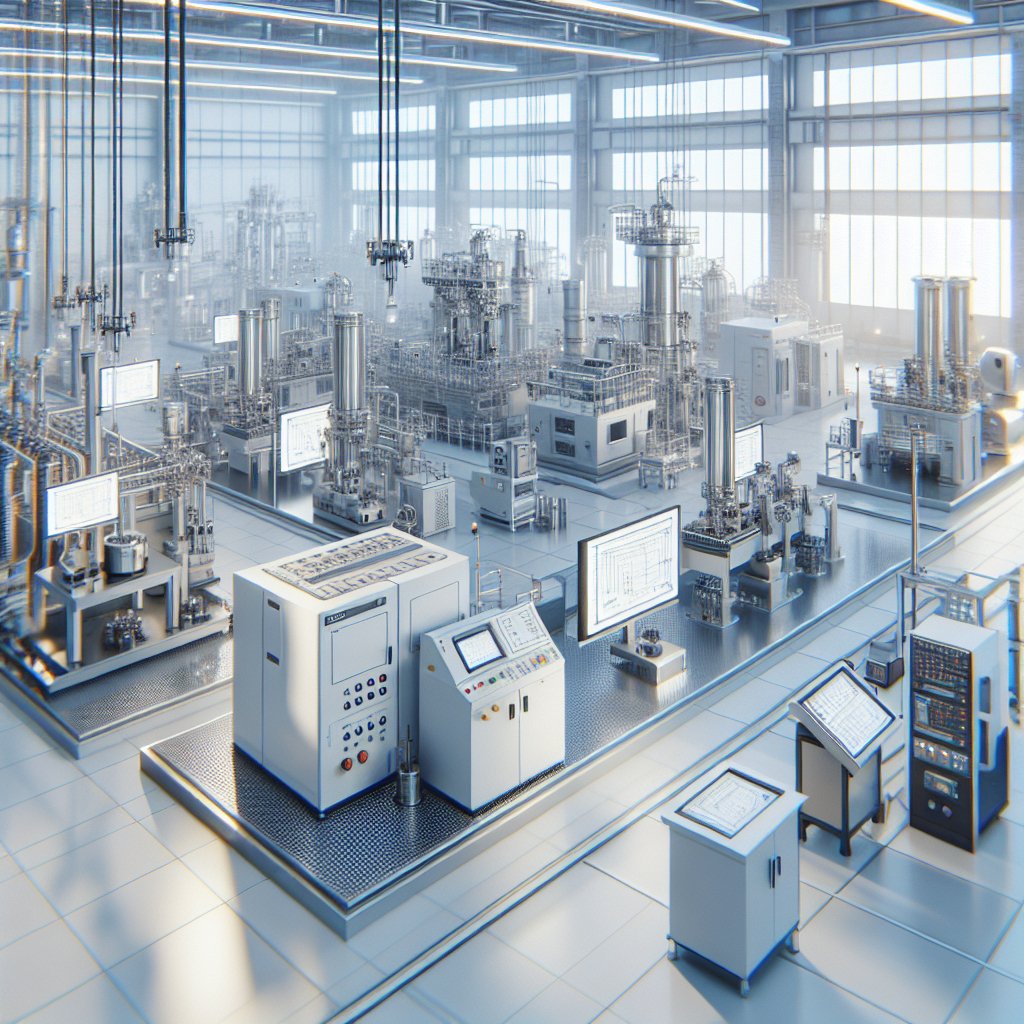
Calibration plays a crucial role in ensuring the accuracy and reliability of industrial equipment testing. In industries where precision is paramount, the process of calibration ensures that instruments and equipment are providing accurate measurements, which is essential for maintaining quality control, safety, and efficiency. This article delves into the significance of calibration, exploring its impact on various industrial sectors and the methodologies involved in the calibration process.
Understanding Calibration and Its Importance
Calibration is the process of configuring an instrument to provide a result for a sample within an acceptable range. It involves comparing the measurements of an instrument or equipment against a standard of known accuracy. The primary goal of calibration is to minimize any measurement uncertainty by ensuring the accuracy of the test equipment. This is vital in industrial settings where even the smallest measurement error can lead to significant issues, including product defects, safety hazards, and financial losses.
In industries such as manufacturing, pharmaceuticals, aerospace, and automotive, precise measurements are critical. For instance, in the pharmaceutical industry, incorrect measurements can lead to incorrect dosages, which can have severe health implications. Similarly, in the aerospace sector, inaccurate measurements can compromise the safety and performance of aircraft. Therefore, regular calibration of equipment is not just a regulatory requirement but a fundamental practice to ensure operational excellence.
Calibration Methods and Techniques
There are several methods and techniques used in the calibration of industrial equipment, each suited to different types of instruments and measurement requirements. The choice of method depends on factors such as the type of instrument, the required accuracy, and the industry standards. Some common calibration methods include:
- Direct Comparison: This method involves comparing the instrument directly with a standard. It is often used for simple instruments like thermometers and pressure gauges.
- Substitution Method: In this technique, the instrument under test is replaced with a standard instrument, and the output is compared. This method is commonly used for electrical instruments.
- Null Method: This involves adjusting the instrument until its output is zero when compared to a standard. It is often used for high-precision measurements.
- Transfer Method: This method uses an intermediate standard to transfer the calibration from a primary standard to the instrument under test. It is useful when direct comparison is not feasible.
Each of these methods has its advantages and limitations, and the choice of method depends on the specific requirements of the calibration task. Regardless of the method used, the calibration process must be carried out by trained professionals using certified standards to ensure accuracy and reliability.
The Impact of Calibration on Quality Control
Calibration is integral to quality control processes in industrial settings. By ensuring that instruments are providing accurate measurements, calibration helps maintain the quality of products and services. This is particularly important in industries where products must meet stringent quality standards and regulatory requirements.
For example, in the automotive industry, precise measurements are essential for ensuring the safety and performance of vehicles. Calibration ensures that components such as engines, brakes, and suspension systems are manufactured to exact specifications. Similarly, in the food and beverage industry, accurate measurements are crucial for maintaining product consistency and safety. Calibration helps ensure that ingredients are measured correctly, and that production processes are operating within specified parameters.
Moreover, calibration contributes to cost savings by reducing waste and minimizing the risk of product recalls. By ensuring that equipment is operating accurately, companies can avoid the costs associated with defective products and rework. This not only improves profitability but also enhances customer satisfaction and brand reputation.
Challenges and Best Practices in Calibration
Despite its importance, calibration can present several challenges for industrial organizations. One of the main challenges is the need to balance accuracy with cost and time. Calibration can be a time-consuming and expensive process, particularly for complex instruments and systems. However, neglecting calibration can lead to even greater costs in terms of product defects, safety incidents, and regulatory penalties.
To overcome these challenges, organizations should adopt best practices in calibration. This includes developing a comprehensive calibration program that outlines the frequency and methods of calibration for each piece of equipment. It is also important to maintain detailed records of calibration activities, including the results and any adjustments made. This documentation is essential for demonstrating compliance with industry standards and regulations.
Another best practice is to invest in training for personnel involved in calibration activities. This ensures that they have the necessary skills and knowledge to perform calibration accurately and efficiently. Additionally, organizations should consider using automated calibration systems, which can improve accuracy and reduce the time and cost associated with manual calibration.
Conclusion
Calibration is a critical component of industrial equipment testing, ensuring the accuracy and reliability of measurements. By minimizing measurement uncertainty, calibration helps maintain quality control, safety, and efficiency in industrial operations. While calibration can present challenges, adopting best practices and investing in training and technology can help organizations overcome these challenges and reap the benefits of accurate and reliable measurements. Ultimately, calibration is not just a regulatory requirement but a fundamental practice for achieving operational excellence and maintaining a competitive edge in the industrial sector.