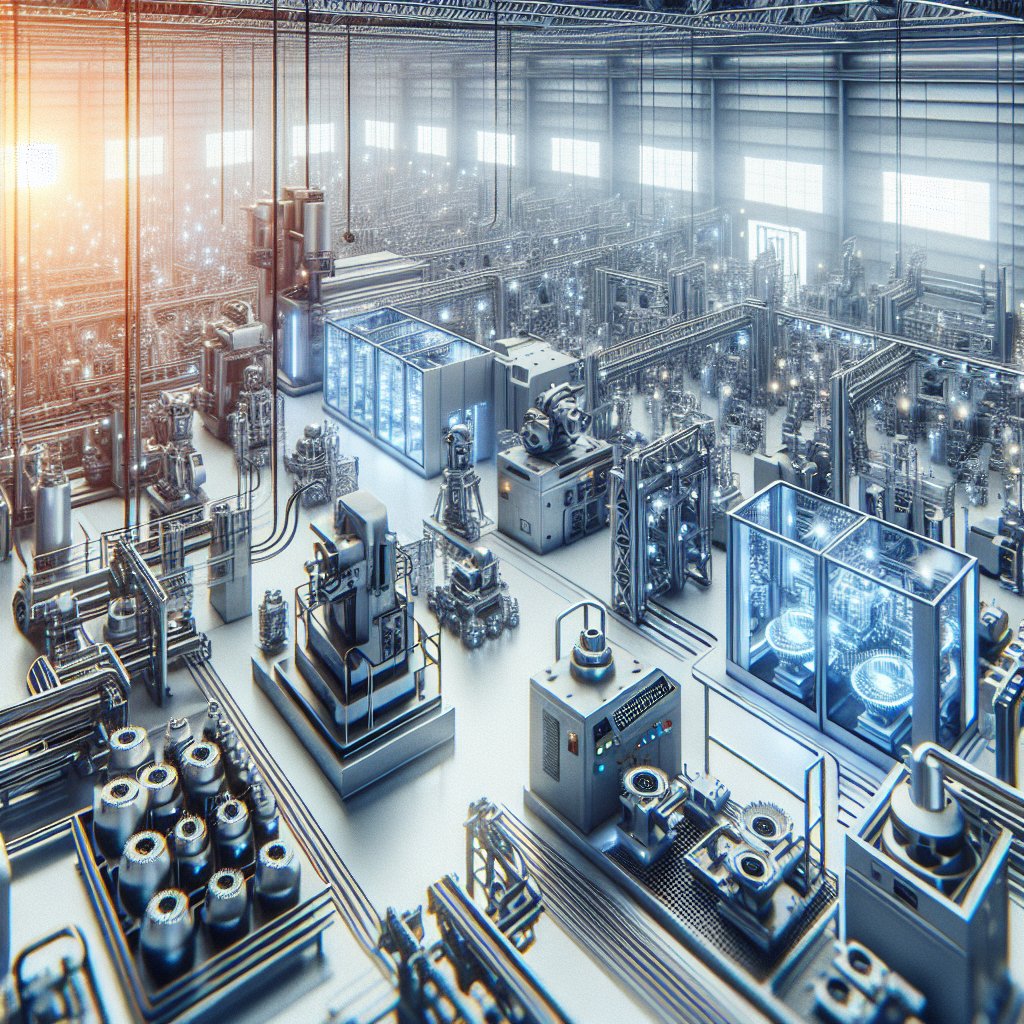
Additive manufacturing, commonly known as 3D printing, is revolutionizing the production of industrial tools, offering unprecedented flexibility, efficiency, and customization. As industries continue to evolve, the integration of additive manufacturing into the production process is becoming increasingly significant, promising a future where industrial tools are not only more efficient but also more sustainable and cost-effective.
Understanding Additive Manufacturing
Additive manufacturing is a process that creates objects by adding material layer by layer, which contrasts with traditional subtractive manufacturing methods that remove material to shape an object. This innovative approach allows for the creation of complex geometries that would be impossible or highly inefficient to achieve with conventional methods. The technology has been around for several decades, but recent advancements have significantly expanded its applications, particularly in the production of industrial tools.
The primary advantage of additive manufacturing is its ability to produce highly customized tools with minimal waste. Traditional manufacturing often involves significant material loss, especially when creating intricate designs. In contrast, additive manufacturing uses only the material necessary to build the object, reducing waste and lowering costs. This efficiency is particularly beneficial in industries where precision and customization are critical, such as aerospace, automotive, and healthcare.
Applications in Industrial Tool Production
One of the most promising applications of additive manufacturing is in the production of industrial tools. These tools, which include jigs, fixtures, molds, and dies, are essential for various manufacturing processes. Additive manufacturing allows for the rapid prototyping and production of these tools, significantly reducing lead times and costs.
For instance, in the automotive industry, additive manufacturing can be used to produce custom fixtures that hold parts in place during assembly. These fixtures can be designed and produced in a fraction of the time it would take using traditional methods, allowing manufacturers to quickly adapt to changes in production requirements. Similarly, in the aerospace industry, additive manufacturing enables the production of lightweight, high-strength tools that can withstand the demanding conditions of flight.
Moreover, additive manufacturing allows for the creation of tools with complex internal structures that enhance performance. For example, cooling channels can be integrated into molds and dies, improving heat dissipation and extending the lifespan of the tool. This level of customization is difficult, if not impossible, to achieve with traditional manufacturing techniques.
Challenges and Opportunities
Despite its many advantages, additive manufacturing in industrial tool production is not without challenges. One of the primary obstacles is the limited range of materials available for 3D printing. While significant progress has been made in developing new materials, the selection is still not as extensive as that available for traditional manufacturing methods. This limitation can restrict the applications of additive manufacturing in certain industries.
Another challenge is the need for specialized knowledge and skills to operate additive manufacturing equipment. As the technology continues to evolve, there is a growing demand for skilled professionals who can design and produce 3D-printed tools. This demand presents an opportunity for educational institutions and training programs to develop curricula that address the skills gap in the industry.
Despite these challenges, the future of additive manufacturing in industrial tool production is bright. As technology continues to advance, the range of materials and applications will expand, making additive manufacturing an increasingly viable option for a wide range of industries. Additionally, the environmental benefits of additive manufacturing, such as reduced waste and energy consumption, align with the growing emphasis on sustainability in manufacturing.
The Road Ahead
Looking ahead, the integration of additive manufacturing into the production of industrial tools is expected to accelerate. As industries continue to seek ways to improve efficiency and reduce costs, the advantages of additive manufacturing will become increasingly apparent. Companies that embrace this technology will be well-positioned to lead the way in innovation and competitiveness.
Furthermore, the continued development of new materials and technologies will open up new possibilities for additive manufacturing. For example, the emergence of metal 3D printing is already transforming the production of high-strength, durable tools. As these technologies become more accessible and affordable, their adoption will likely increase, further driving the growth of additive manufacturing in industrial tool production.
In conclusion, the future of additive manufacturing in the production of industrial tools is promising. With its ability to produce highly customized, efficient, and sustainable tools, additive manufacturing is set to play a crucial role in the evolution of manufacturing processes. As industries continue to adapt to changing demands and technologies, additive manufacturing will undoubtedly be at the forefront of this transformation, shaping the future of industrial tool production.