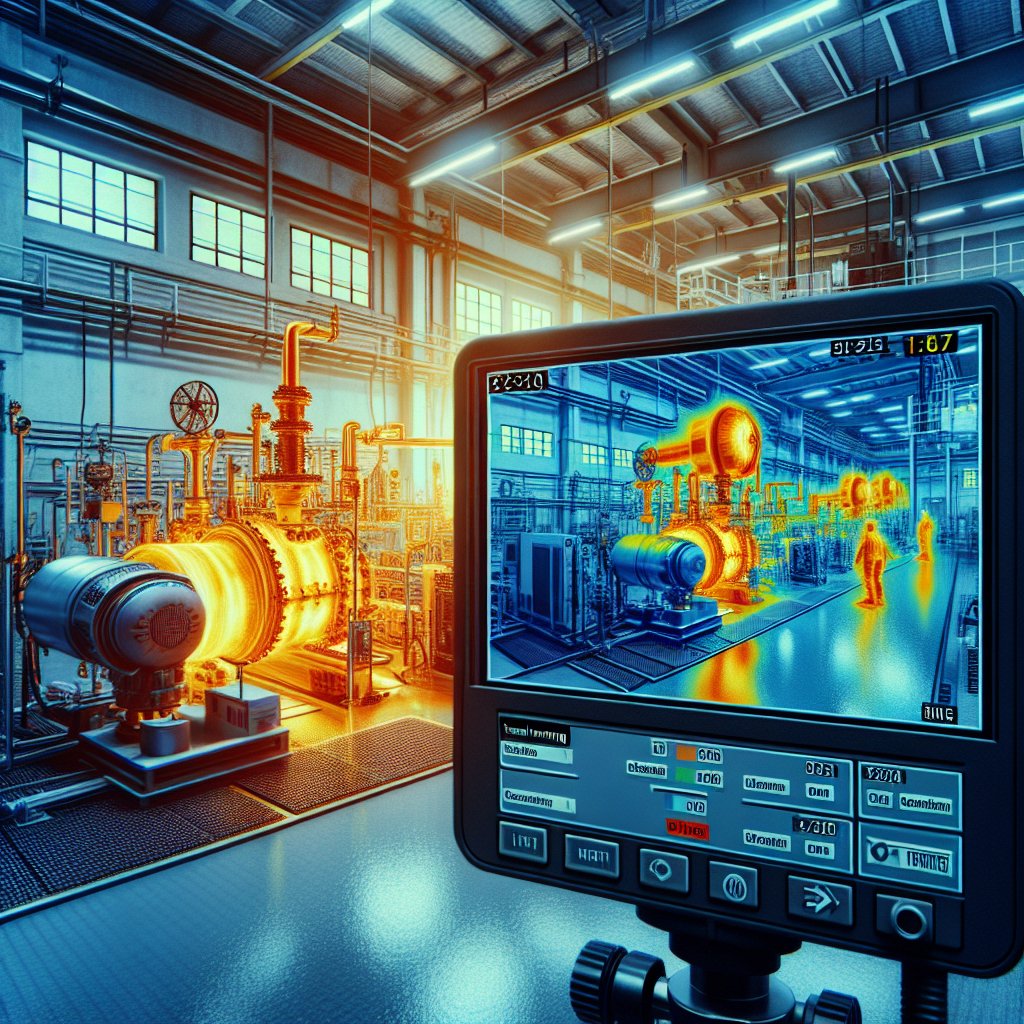
Thermal imaging technology has revolutionized the way industries monitor and maintain their equipment. By providing a non-invasive and highly accurate method of detecting temperature variations, thermal imaging allows for the early identification of potential issues, thereby preventing costly downtime and enhancing operational efficiency. This article delves into the application of thermal imaging in industrial equipment monitoring, exploring its benefits, challenges, and future prospects.
Understanding Thermal Imaging Technology
Thermal imaging, also known as thermography, is a technique that uses infrared cameras to detect heat emitted by objects. These cameras capture the infrared radiation and convert it into a visual image, known as a thermogram, which displays temperature variations across the surface of the object. This technology is particularly useful in industrial settings where equipment operates under high temperatures and any deviation from the norm can indicate a potential problem.
The Science Behind Thermal Imaging
At the core of thermal imaging technology is the principle that all objects emit infrared radiation as a function of their temperature. The amount of radiation emitted increases with temperature, allowing thermal cameras to detect even slight variations. These cameras are equipped with sensors that capture the infrared radiation and convert it into electronic signals, which are then processed to create a visual representation of the temperature distribution.
Thermal imaging cameras are designed to detect a wide range of temperatures, making them suitable for various industrial applications. They can be used to monitor equipment such as motors, pumps, electrical panels, and more, providing valuable insights into their operational status.
Advantages of Thermal Imaging in Industry
One of the primary advantages of thermal imaging is its non-contact nature. This allows for the inspection of equipment while it is in operation, eliminating the need for shutdowns and minimizing disruptions. Additionally, thermal imaging provides real-time data, enabling quick decision-making and immediate action when necessary.
Another significant benefit is the ability to detect issues that are not visible to the naked eye. For instance, thermal imaging can identify overheating components, poor electrical connections, and insulation failures, all of which can lead to equipment failure if not addressed promptly. By identifying these issues early, maintenance teams can take corrective action before they escalate into more serious problems.
Applications of Thermal Imaging in Industrial Equipment Monitoring
Thermal imaging is employed across a wide range of industries, each with its unique set of challenges and requirements. Below are some of the most common applications of thermal imaging in industrial equipment monitoring.
Electrical Systems
In electrical systems, thermal imaging is used to detect hot spots that may indicate loose connections, overloaded circuits, or failing components. By identifying these issues early, companies can prevent electrical fires and equipment damage, ensuring the safety and reliability of their operations.
Regular thermal inspections of electrical panels, transformers, and switchgear can help maintain optimal performance and extend the lifespan of the equipment. This proactive approach to maintenance reduces the risk of unexpected failures and costly repairs.
Mechanical Systems
Thermal imaging is also valuable in monitoring mechanical systems, such as motors, bearings, and pumps. Overheating in these components can be a sign of excessive friction, misalignment, or lubrication issues. By detecting these problems early, maintenance teams can perform necessary adjustments or replacements, preventing further damage and ensuring smooth operation.
In addition to identifying potential issues, thermal imaging can be used to verify the effectiveness of repairs and maintenance activities. By comparing thermal images before and after maintenance, technicians can confirm that the problem has been resolved and the equipment is operating within normal temperature ranges.
Process Monitoring
In industries such as manufacturing and chemical processing, thermal imaging is used to monitor processes and ensure they are operating within specified temperature ranges. This is crucial for maintaining product quality and consistency, as well as ensuring the safety of the operation.
Thermal imaging can be used to monitor the temperature of materials as they move through production lines, detect blockages or leaks in pipelines, and ensure that heating and cooling systems are functioning correctly. By providing real-time data, thermal imaging enables operators to make informed decisions and take corrective action when necessary.
Challenges and Limitations of Thermal Imaging
While thermal imaging offers numerous benefits, it is not without its challenges and limitations. Understanding these can help industries make informed decisions about its implementation and use.
Environmental Factors
One of the primary challenges of thermal imaging is its sensitivity to environmental factors. Ambient temperature, humidity, and wind can all affect the accuracy of thermal readings. For instance, high humidity can cause thermal images to appear cooler than they actually are, while wind can dissipate heat and mask potential issues.
To mitigate these effects, it is important to conduct thermal inspections under controlled conditions and to account for environmental factors when interpreting the results. This may involve using additional sensors or software to compensate for variations in ambient conditions.
Interpretation of Data
Another challenge is the interpretation of thermal images. While thermal cameras provide a visual representation of temperature variations, it requires expertise to accurately interpret the data and identify potential issues. This can be particularly challenging in complex systems where multiple factors may contribute to temperature anomalies.
To address this, many companies invest in training for their maintenance teams, ensuring they have the skills and knowledge to effectively use thermal imaging technology. Additionally, advancements in software and artificial intelligence are helping to automate the analysis of thermal images, making it easier to identify patterns and anomalies.
The Future of Thermal Imaging in Industry
As technology continues to advance, the future of thermal imaging in industrial equipment monitoring looks promising. Innovations in camera design, data analysis, and integration with other technologies are set to enhance the capabilities and applications of thermal imaging.
Integration with IoT and AI
The integration of thermal imaging with the Internet of Things (IoT) and artificial intelligence (AI) is one of the most exciting developments in the field. By connecting thermal cameras to IoT networks, companies can collect and analyze data from multiple sources, providing a comprehensive view of their operations.
AI algorithms can be used to process large volumes of thermal data, identifying patterns and trends that may not be immediately apparent to human operators. This can lead to more accurate predictions of equipment failures and more effective maintenance strategies.
Advancements in Camera Technology
Advancements in camera technology are also driving the future of thermal imaging. Newer cameras offer higher resolution, greater sensitivity, and faster processing speeds, allowing for more detailed and accurate thermal images. Additionally, the development of portable and handheld thermal cameras is making the technology more accessible and versatile.
These advancements are expanding the range of applications for thermal imaging, enabling its use in more challenging environments and for more complex systems. As the technology continues to evolve, it is likely to become an even more integral part of industrial equipment monitoring.
In conclusion, thermal imaging is a powerful tool for industrial equipment monitoring, offering numerous benefits in terms of safety, efficiency, and cost savings. While there are challenges to its implementation, ongoing advancements in technology and data analysis are set to enhance its capabilities and applications. As industries continue to embrace thermal imaging, it is poised to play a critical role in the future of equipment maintenance and monitoring.