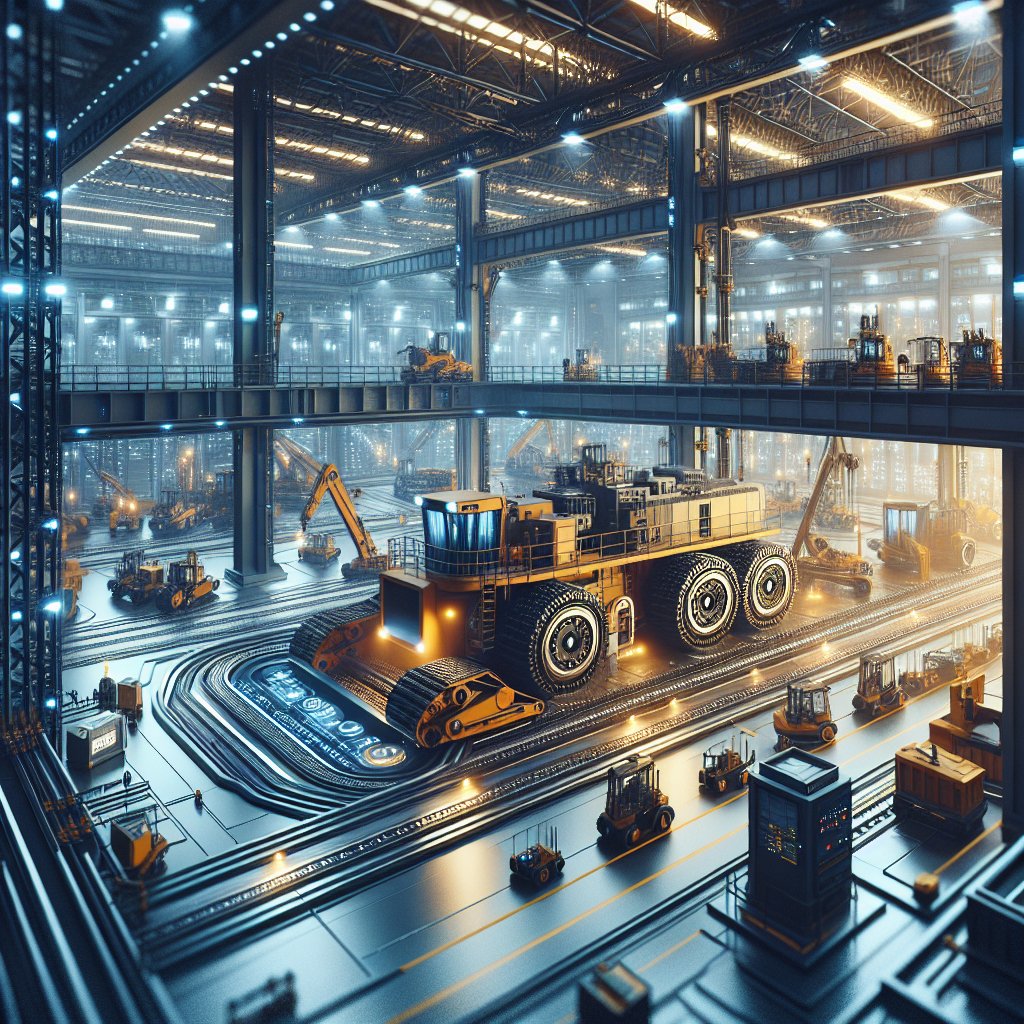
Preventive maintenance for heavy machinery is a critical aspect of ensuring operational efficiency and longevity in industrial settings. This approach not only helps in minimizing unexpected breakdowns but also plays a significant role in optimizing the performance of the equipment. In this article, we will explore key strategies for implementing effective preventive maintenance programs, focusing on the benefits and best practices that can be adopted by industries relying heavily on machinery.
Understanding Preventive Maintenance
Preventive maintenance refers to the routine maintenance activities performed on equipment to prevent unexpected failures and extend its lifespan. Unlike reactive maintenance, which addresses issues after they occur, preventive maintenance is proactive, aiming to identify and resolve potential problems before they lead to costly downtimes. This approach is particularly crucial for heavy machinery, which often operates under demanding conditions and is integral to production processes.
The primary goal of preventive maintenance is to ensure that machinery remains in optimal working condition, thereby reducing the likelihood of unexpected breakdowns. This involves regular inspections, servicing, and replacement of worn-out parts. By adhering to a well-structured maintenance schedule, companies can significantly reduce repair costs and improve the overall efficiency of their operations.
Key Strategies for Effective Preventive Maintenance
1. Develop a Comprehensive Maintenance Plan
Creating a detailed maintenance plan is the first step towards implementing an effective preventive maintenance program. This plan should outline the specific maintenance tasks required for each piece of equipment, along with the frequency of these tasks. It is essential to consider the manufacturer’s recommendations, as well as the operational demands placed on the machinery, when developing this plan.
Additionally, the maintenance plan should include a schedule for regular inspections, lubrication, cleaning, and calibration of equipment. By establishing a clear and comprehensive plan, companies can ensure that all necessary maintenance activities are performed consistently and on time.
2. Utilize Technology and Data Analytics
Advancements in technology have revolutionized the way preventive maintenance is conducted. By leveraging data analytics and predictive maintenance tools, companies can gain valuable insights into the condition of their machinery. These tools use sensors and data collection systems to monitor equipment performance in real-time, allowing for the early detection of potential issues.
Data analytics can help identify patterns and trends that may indicate impending failures, enabling maintenance teams to address problems before they escalate. This proactive approach not only reduces downtime but also extends the lifespan of the equipment, resulting in significant cost savings over time.
3. Train and Empower Maintenance Personnel
The success of a preventive maintenance program largely depends on the skills and expertise of the maintenance personnel. It is crucial to invest in training programs that equip maintenance teams with the knowledge and skills needed to perform their tasks effectively. This includes training on the latest maintenance techniques, safety protocols, and the use of advanced diagnostic tools.
Empowering maintenance personnel to take ownership of their roles and encouraging them to proactively identify and address potential issues can lead to more efficient and effective maintenance practices. By fostering a culture of continuous improvement, companies can enhance the overall performance of their preventive maintenance programs.
4. Implement a Robust Documentation System
Maintaining accurate and up-to-date records is essential for the success of any preventive maintenance program. A robust documentation system allows companies to track the maintenance history of each piece of equipment, including details of inspections, repairs, and replacements. This information is invaluable for identifying recurring issues and making informed decisions about future maintenance activities.
Furthermore, documentation provides a clear record of compliance with regulatory requirements and can be used to demonstrate due diligence in the event of an audit or inspection. By implementing a comprehensive documentation system, companies can ensure that their preventive maintenance efforts are well-organized and effective.
Benefits of Preventive Maintenance
Implementing a preventive maintenance program offers numerous benefits for companies that rely on heavy machinery. One of the most significant advantages is the reduction in unexpected breakdowns and associated downtime. By addressing potential issues before they lead to equipment failure, companies can maintain consistent production schedules and avoid costly disruptions.
Preventive maintenance also contributes to improved equipment performance and efficiency. Regular servicing and inspections help ensure that machinery operates at peak performance, reducing energy consumption and minimizing wear and tear. This not only extends the lifespan of the equipment but also results in cost savings through reduced energy bills and lower repair costs.
Moreover, preventive maintenance enhances workplace safety by identifying and addressing potential hazards before they pose a risk to employees. By maintaining equipment in optimal condition, companies can create a safer working environment and reduce the likelihood of accidents and injuries.
Conclusion
Preventive maintenance is a vital component of effective machinery management, offering numerous benefits in terms of operational efficiency, cost savings, and safety. By developing a comprehensive maintenance plan, utilizing technology and data analytics, training maintenance personnel, and implementing a robust documentation system, companies can optimize their preventive maintenance efforts and ensure the longevity and reliability of their heavy machinery.
In conclusion, adopting a proactive approach to maintenance not only minimizes the risk of unexpected breakdowns but also enhances the overall performance and efficiency of industrial operations. By prioritizing preventive maintenance, companies can achieve significant improvements in productivity and profitability, while also ensuring a safer and more sustainable working environment.