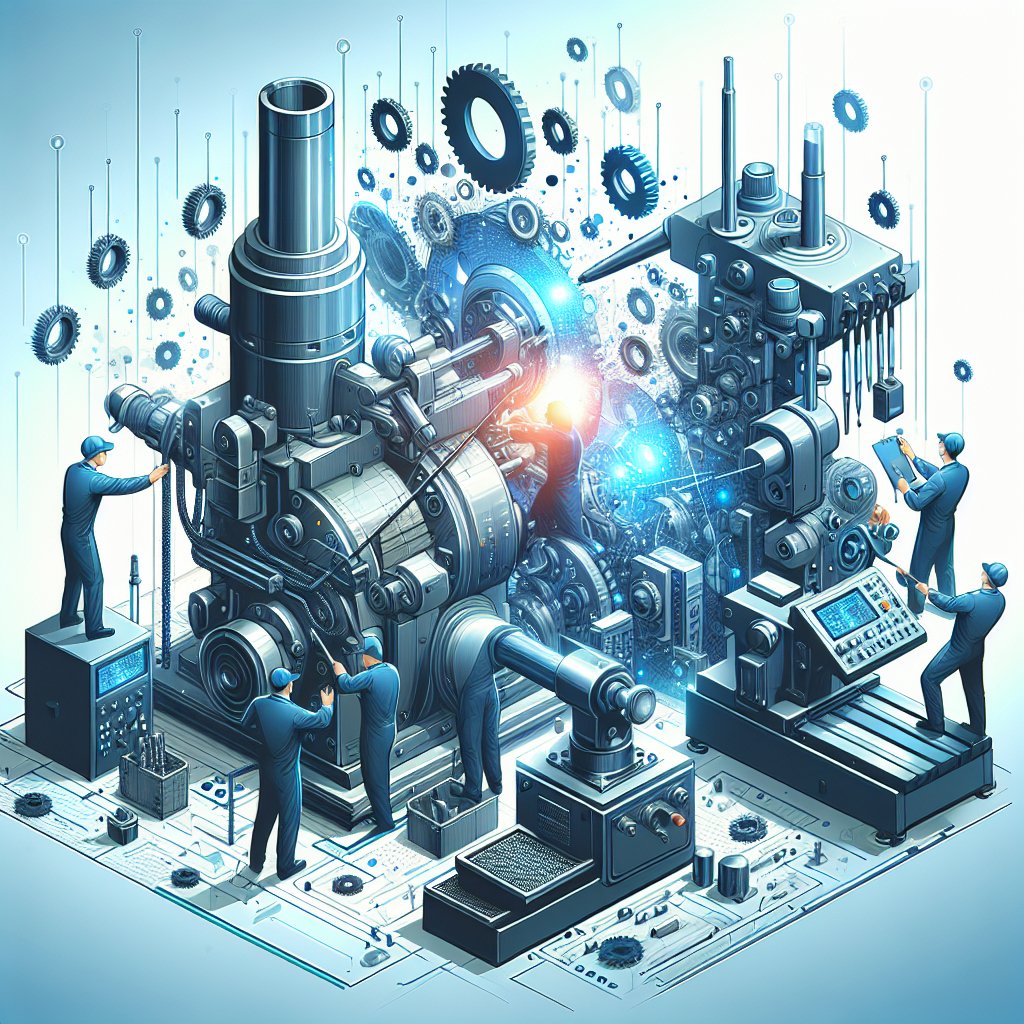
Machine tool maintenance is a critical aspect of ensuring maximum uptime and efficiency in manufacturing operations. Proper maintenance practices not only extend the lifespan of machinery but also enhance productivity and reduce the risk of unexpected breakdowns. In this article, we will explore essential maintenance practices that can help keep machine tools in optimal condition, ensuring they perform at their best.
Understanding the Importance of Machine Tool Maintenance
Machine tools are the backbone of manufacturing industries, playing a vital role in shaping, cutting, and forming materials into finished products. Given their importance, maintaining these tools is crucial for several reasons. Firstly, regular maintenance helps in identifying potential issues before they escalate into major problems, thereby preventing costly downtime. Secondly, well-maintained machines operate more efficiently, leading to higher quality outputs and reduced waste. Lastly, a robust maintenance program can significantly extend the lifespan of machine tools, providing a better return on investment.
One of the primary goals of machine tool maintenance is to ensure that the equipment operates within its specified parameters. This involves regular inspections, cleaning, lubrication, and calibration. By adhering to a structured maintenance schedule, manufacturers can minimize the risk of unexpected failures and maintain a consistent production flow.
Key Maintenance Practices for Machine Tools
Regular Inspections
Conducting regular inspections is a fundamental aspect of machine tool maintenance. These inspections should be carried out by trained personnel who can identify signs of wear and tear, misalignment, or other potential issues. Inspections should cover all critical components, including bearings, spindles, belts, and electrical systems. By catching problems early, manufacturers can address them before they lead to more significant issues.
Cleaning and Lubrication
Keeping machine tools clean and well-lubricated is essential for their smooth operation. Accumulated dirt, dust, and debris can cause components to wear out faster and lead to malfunctions. Regular cleaning helps prevent these issues, while proper lubrication reduces friction and wear on moving parts. It’s important to use the right type of lubricant for each machine and to follow the manufacturer’s recommendations for application frequency.
Calibration and Alignment
Calibration and alignment are critical for ensuring that machine tools produce accurate and precise outputs. Over time, machines can drift out of alignment due to regular use, leading to errors in production. Regular calibration checks help maintain the accuracy of the equipment, ensuring that it meets the required specifications. This is particularly important for industries where precision is paramount, such as aerospace and medical device manufacturing.
Replacement of Worn Parts
Even with the best maintenance practices, some machine components will inevitably wear out over time. It’s crucial to replace these parts promptly to prevent them from causing further damage to the machine. Manufacturers should keep an inventory of commonly used spare parts and establish a system for tracking the condition of critical components. This proactive approach helps minimize downtime and ensures that machines are always ready for production.
Implementing a Preventive Maintenance Program
A preventive maintenance program is a structured approach to maintaining machine tools, focusing on regular, scheduled maintenance activities rather than reactive repairs. Implementing such a program involves several key steps:
- Develop a Maintenance Schedule: Create a detailed schedule outlining when each maintenance task should be performed. This schedule should be based on the manufacturer’s recommendations and the specific needs of the equipment.
- Train Maintenance Personnel: Ensure that maintenance staff are properly trained and equipped to carry out their tasks. This includes understanding the operation of the machines, recognizing signs of wear, and knowing how to perform basic repairs.
- Document Maintenance Activities: Keep detailed records of all maintenance activities, including inspections, repairs, and part replacements. This documentation helps track the history of each machine and can be invaluable for troubleshooting future issues.
- Monitor Machine Performance: Use performance data to identify trends and potential issues. This can involve tracking metrics such as production output, energy consumption, and downtime. Analyzing this data can help refine the maintenance program and improve overall efficiency.
Conclusion
Machine tool maintenance is an essential practice for maximizing uptime and ensuring the efficient operation of manufacturing equipment. By implementing a comprehensive maintenance program that includes regular inspections, cleaning, lubrication, calibration, and part replacement, manufacturers can significantly reduce the risk of unexpected breakdowns and extend the lifespan of their machinery. Ultimately, a well-maintained machine tool not only enhances productivity but also contributes to the overall success of the manufacturing operation.