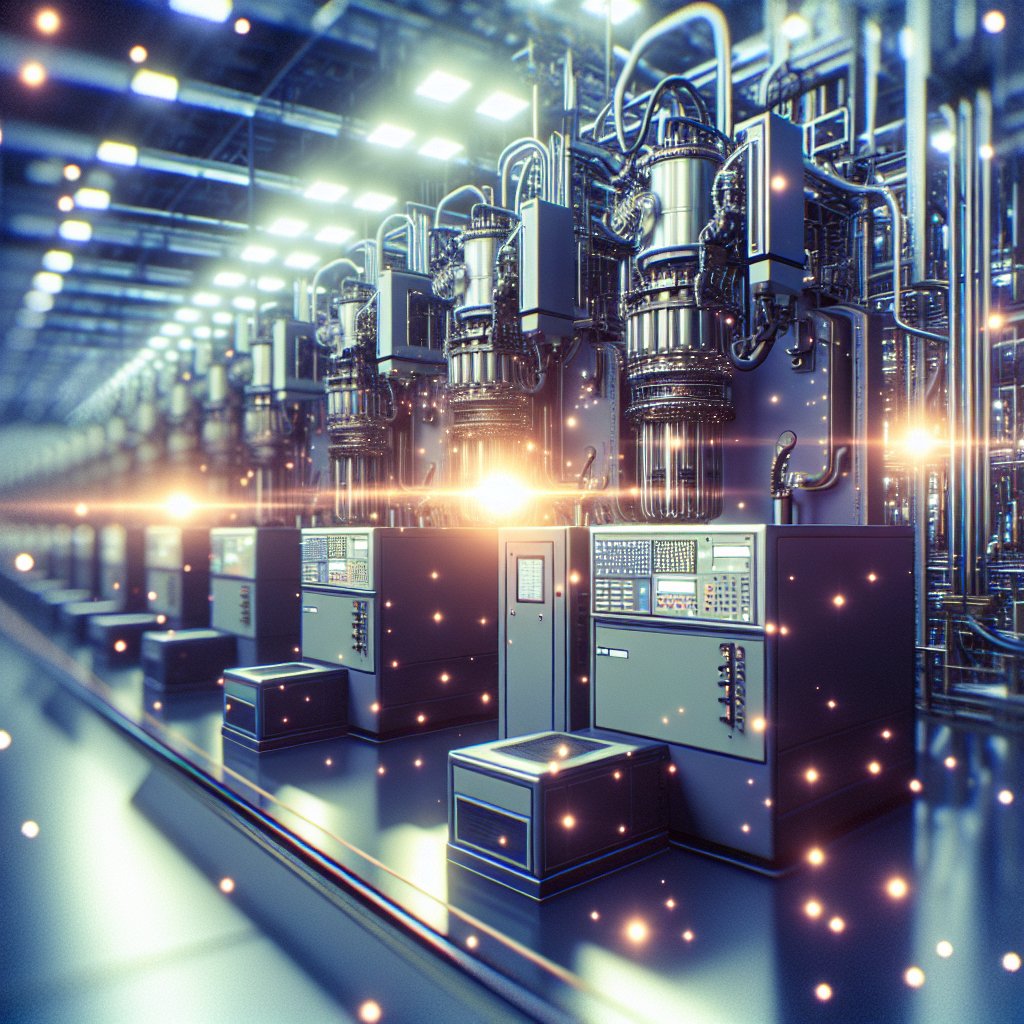
Machine learning has revolutionized various industries, and its applications in industrial equipment maintenance are no exception. By leveraging advanced algorithms and data analytics, companies can now predict equipment failures, optimize maintenance schedules, and reduce downtime, leading to significant cost savings and increased operational efficiency.
Understanding Machine Learning in Maintenance
Machine learning, a subset of artificial intelligence, involves the use of algorithms and statistical models to enable computers to perform tasks without explicit instructions. In the context of industrial equipment maintenance, machine learning can analyze vast amounts of data generated by machinery to identify patterns and predict potential failures. This predictive capability is crucial for industries that rely heavily on machinery, such as manufacturing, oil and gas, and transportation.
Traditionally, maintenance strategies have been reactive or preventive. Reactive maintenance involves repairing equipment after a failure has occurred, often leading to unexpected downtime and higher costs. Preventive maintenance, on the other hand, involves regular inspections and servicing based on a set schedule, regardless of the equipment’s actual condition. While preventive maintenance can reduce the likelihood of unexpected failures, it may still result in unnecessary maintenance activities and associated costs.
Machine learning introduces a more sophisticated approach known as predictive maintenance. By analyzing historical and real-time data from sensors and other sources, machine learning models can predict when a piece of equipment is likely to fail. This allows maintenance teams to perform targeted interventions only when necessary, optimizing resource allocation and minimizing downtime.
Key Machine Learning Techniques in Maintenance
Several machine learning techniques are commonly used in industrial equipment maintenance, each with its unique strengths and applications. Understanding these techniques is essential for implementing effective predictive maintenance strategies.
Supervised Learning
Supervised learning involves training a model on a labeled dataset, where the input data is paired with the correct output. In maintenance, this could involve using historical data on equipment failures to train a model to predict future failures. Techniques such as regression analysis and classification are commonly used in supervised learning for maintenance applications.
For example, regression models can predict the remaining useful life (RUL) of a component based on various input features, such as temperature, vibration, and pressure readings. Classification models, on the other hand, can categorize equipment into different health states, such as “normal,” “degraded,” or “failure imminent.”
Unsupervised Learning
Unsupervised learning does not rely on labeled data, making it suitable for discovering hidden patterns or anomalies in data. Clustering and anomaly detection are two popular unsupervised learning techniques used in maintenance.
Clustering can group similar data points together, helping identify patterns or trends in equipment behavior. For instance, clustering algorithms can segment equipment operating conditions into different clusters, allowing maintenance teams to identify which conditions are associated with higher failure rates.
Anomaly detection, on the other hand, focuses on identifying data points that deviate significantly from the norm. In maintenance, this can help detect unusual patterns that may indicate an impending failure, allowing for timely intervention.
Reinforcement Learning
Reinforcement learning involves training a model to make decisions by rewarding desired outcomes and penalizing undesired ones. While less commonly used in maintenance compared to supervised and unsupervised learning, reinforcement learning can optimize maintenance schedules and resource allocation.
For example, a reinforcement learning model can learn to balance the trade-off between maintenance costs and equipment reliability by simulating different maintenance strategies and selecting the one that maximizes overall performance.
Challenges and Considerations
While machine learning offers significant benefits for industrial equipment maintenance, several challenges and considerations must be addressed to ensure successful implementation.
Data Quality and Availability
High-quality data is essential for training accurate machine learning models. However, industrial environments often face challenges related to data quality and availability. Sensor data may be noisy or incomplete, and historical maintenance records may be inconsistent or lacking in detail. Ensuring data quality and addressing gaps in data collection are critical steps in developing effective predictive maintenance models.
Integration with Existing Systems
Integrating machine learning solutions with existing maintenance management systems can be complex. Organizations must ensure that machine learning models can seamlessly interact with existing data sources and maintenance workflows. This may require investments in IT infrastructure and collaboration between data scientists, engineers, and maintenance personnel.
Scalability and Adaptability
Machine learning models must be scalable and adaptable to different types of equipment and operating conditions. A model that works well for one type of machinery may not be suitable for another, requiring customization and continuous updates. Organizations must be prepared to invest in ongoing model development and maintenance to ensure long-term success.
Future Trends and Opportunities
The future of machine learning in industrial equipment maintenance is promising, with several emerging trends and opportunities on the horizon.
Integration with IoT and Edge Computing
The integration of machine learning with the Internet of Things (IoT) and edge computing is set to transform maintenance practices. IoT devices can collect real-time data from equipment, while edge computing allows for data processing closer to the source, reducing latency and enabling faster decision-making. This combination can enhance the accuracy and timeliness of predictive maintenance models.
Advanced Analytics and Visualization
Advanced analytics and visualization tools are becoming increasingly important for interpreting machine learning outputs and making data-driven decisions. Interactive dashboards and visualizations can help maintenance teams understand complex data patterns and prioritize maintenance activities effectively.
Collaboration and Knowledge Sharing
Collaboration and knowledge sharing among industry stakeholders, including manufacturers, maintenance providers, and technology vendors, will be crucial for advancing machine learning applications in maintenance. Sharing best practices, data, and insights can accelerate innovation and drive the adoption of predictive maintenance solutions across industries.
In conclusion, machine learning is poised to play a transformative role in industrial equipment maintenance, offering significant benefits in terms of cost savings, operational efficiency, and equipment reliability. By understanding the key techniques, challenges, and future trends, organizations can harness the power of machine learning to optimize their maintenance strategies and stay competitive in an increasingly data-driven world.