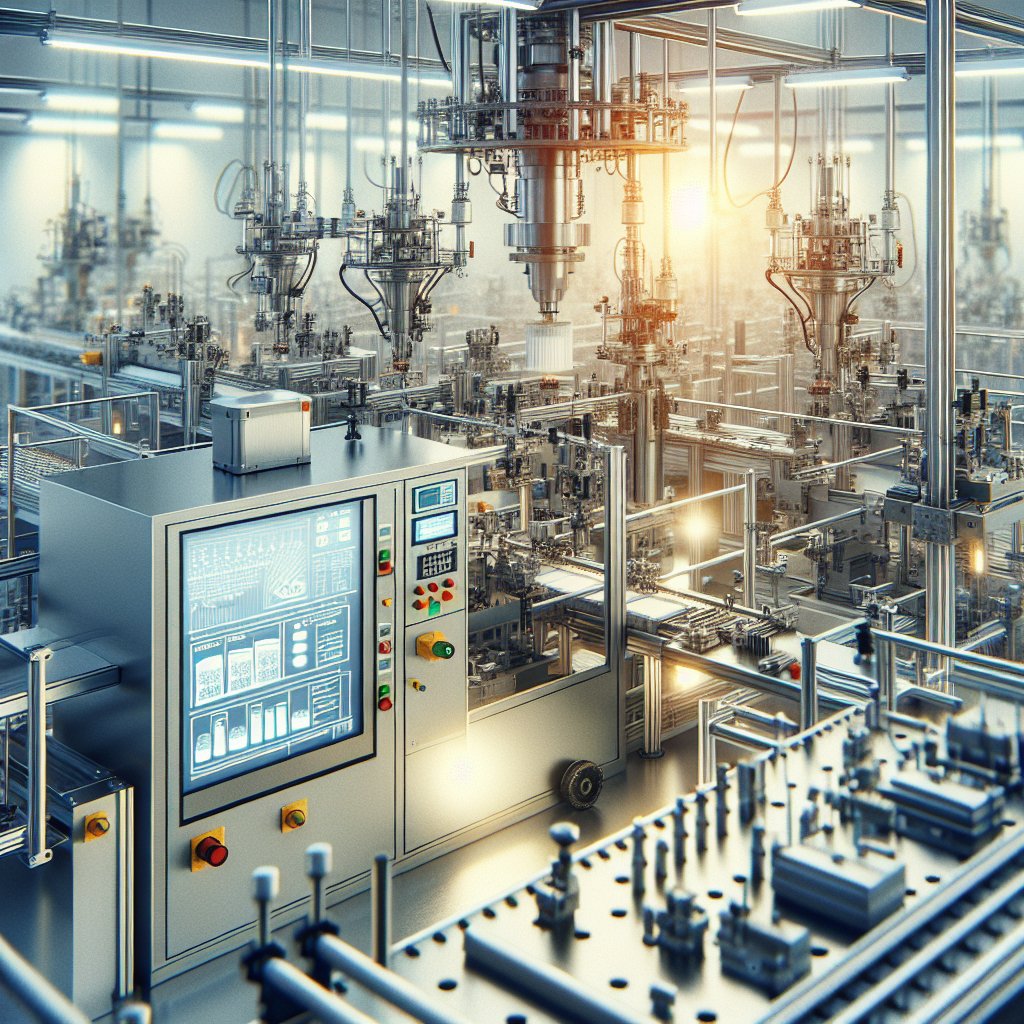
Automated packaging systems have revolutionized the manufacturing industry, offering a range of benefits that enhance efficiency, reduce costs, and improve product quality. As businesses strive to meet increasing consumer demands and maintain a competitive edge, the integration of automated solutions in packaging processes has become a critical component of modern manufacturing strategies.
Enhancing Efficiency and Productivity
One of the primary advantages of automated packaging systems is their ability to significantly enhance efficiency and productivity within manufacturing operations. By automating repetitive and time-consuming tasks, these systems allow human workers to focus on more complex and value-added activities. This shift not only increases the overall output but also reduces the likelihood of human error, leading to more consistent and reliable packaging processes.
Automated systems are designed to operate at high speeds, often surpassing the capabilities of manual labor. This increased speed translates to faster production cycles, enabling manufacturers to meet tight deadlines and respond swiftly to market demands. Additionally, automated packaging systems can operate continuously, without the need for breaks or shift changes, further maximizing productivity and ensuring a steady flow of packaged products.
Cost Reduction and Resource Optimization
Implementing automated packaging systems can lead to significant cost savings for manufacturers. By reducing the reliance on manual labor, companies can lower labor costs and minimize the expenses associated with training and managing a large workforce. Moreover, automated systems are designed to optimize the use of materials, reducing waste and ensuring that packaging resources are utilized efficiently.
These systems also contribute to energy savings, as they are often equipped with energy-efficient technologies that minimize power consumption. This not only reduces operational costs but also aligns with sustainability goals, helping manufacturers reduce their environmental footprint. Furthermore, the precision and accuracy of automated systems minimize the risk of product damage during packaging, reducing the costs associated with returns and rework.
Improving Product Quality and Consistency
Automated packaging systems play a crucial role in maintaining high product quality and consistency. By standardizing packaging processes, these systems ensure that each product is packaged uniformly, meeting the required specifications and quality standards. This consistency is particularly important for industries where precise packaging is essential, such as pharmaceuticals and food and beverage.
The advanced technology used in automated systems allows for real-time monitoring and quality control, enabling manufacturers to detect and address any issues promptly. This proactive approach to quality management reduces the risk of defects and enhances customer satisfaction by delivering products that consistently meet or exceed expectations.
Flexibility and Scalability
Modern automated packaging systems are designed with flexibility and scalability in mind, allowing manufacturers to adapt to changing production needs and market demands. These systems can be easily reconfigured to accommodate different product sizes, shapes, and packaging materials, providing manufacturers with the versatility needed to diversify their product offerings.
Scalability is another key benefit, as automated systems can be expanded or modified to handle increased production volumes. This adaptability ensures that manufacturers can grow their operations without the need for significant investments in new equipment or infrastructure, making automated packaging systems a cost-effective solution for long-term business growth.
Enhancing Safety and Ergonomics
Automated packaging systems contribute to a safer and more ergonomic work environment by reducing the physical demands placed on human workers. By automating tasks that involve heavy lifting, repetitive motions, or exposure to hazardous materials, these systems help minimize the risk of workplace injuries and improve overall employee well-being.
Furthermore, the integration of advanced safety features in automated systems, such as sensors and emergency stop mechanisms, ensures that operations can be conducted safely and efficiently. This focus on safety not only protects workers but also reduces the potential for costly accidents and downtime, further enhancing the overall efficiency of manufacturing processes.
Conclusion
In conclusion, the adoption of automated packaging systems in manufacturing offers a multitude of benefits that extend beyond mere cost savings. By enhancing efficiency, improving product quality, and providing flexibility and scalability, these systems empower manufacturers to meet the challenges of a dynamic market environment. As technology continues to advance, the role of automation in packaging will undoubtedly become even more integral to the success of manufacturing operations worldwide.