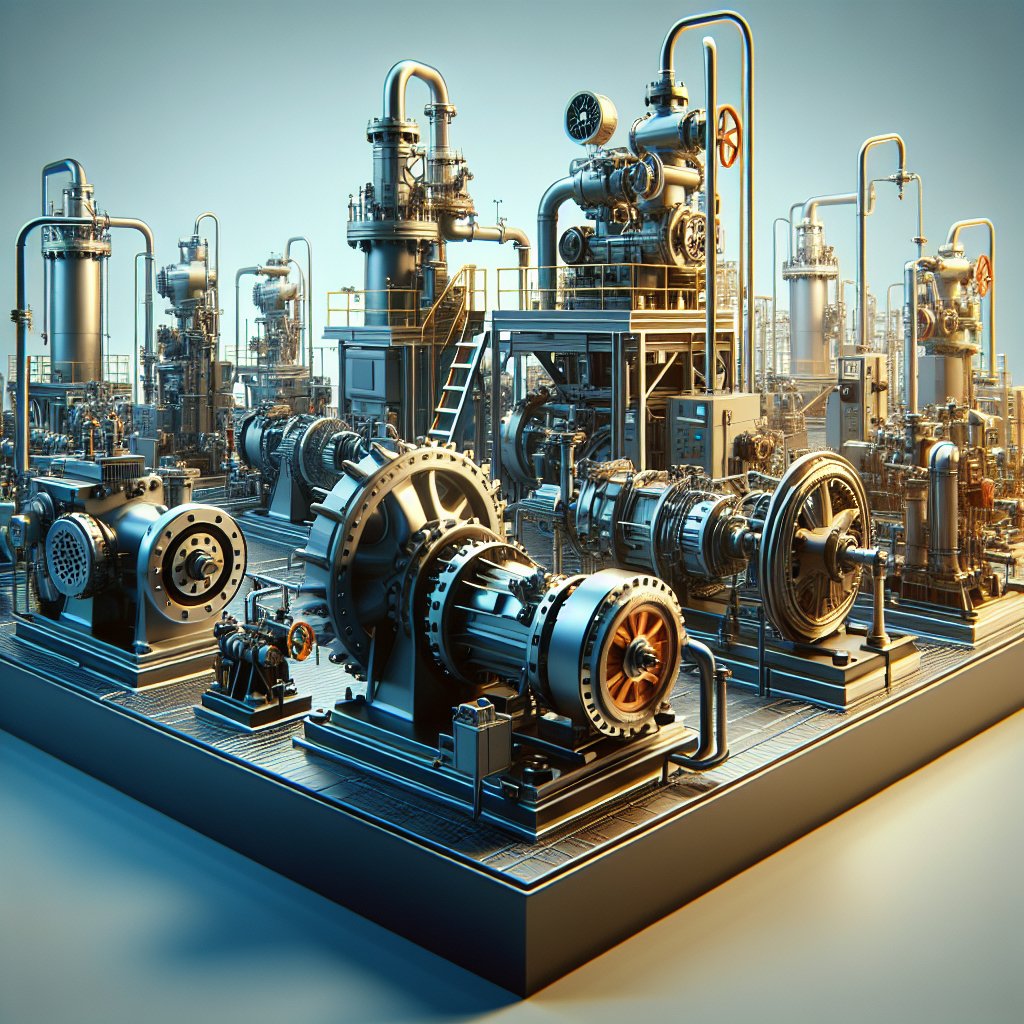
Choosing the right industrial pump for your application is a critical decision that can significantly impact the efficiency and cost-effectiveness of your operations. With a wide variety of pumps available on the market, each designed for specific purposes, understanding the key factors that influence pump selection is essential. This article will guide you through the process of selecting the most suitable pump for your needs, considering factors such as fluid properties, pump types, and operational requirements.
Understanding Fluid Properties
Before selecting an industrial pump, it is crucial to have a comprehensive understanding of the fluid properties involved in your application. The characteristics of the fluid will directly influence the type of pump that is most suitable. Here are some key fluid properties to consider:
Viscosity
Viscosity refers to the thickness or resistance to flow of a fluid. Fluids with high viscosity, such as oils or syrups, require pumps that can handle thicker substances without losing efficiency. Positive displacement pumps, such as gear pumps or diaphragm pumps, are often suitable for high-viscosity fluids due to their ability to move fluid in a controlled manner.
Density
The density of a fluid affects the energy required to move it. Denser fluids require more power to pump, which can influence the choice of pump type and size. Centrifugal pumps are commonly used for low to medium-density fluids, while positive displacement pumps may be more appropriate for denser substances.
Corrosiveness
Corrosive fluids can cause significant damage to pump components if not properly managed. When dealing with corrosive substances, it is essential to select pumps made from materials that can withstand chemical reactions. Stainless steel, plastic, and specialized alloys are often used in pump construction to resist corrosion.
Temperature
The temperature of the fluid can affect both the pump’s performance and its material compatibility. High temperatures may require pumps with specialized seals and materials to prevent damage and ensure efficient operation. Conversely, low temperatures might necessitate pumps with heating elements or insulation to maintain fluid flow.
Types of Industrial Pumps
Once you have a clear understanding of the fluid properties, the next step is to explore the different types of industrial pumps available. Each pump type has its own advantages and limitations, making it suitable for specific applications. Here are some common types of industrial pumps:
Centrifugal Pumps
Centrifugal pumps are one of the most widely used types of industrial pumps. They operate by converting rotational energy from a motor into kinetic energy, which moves the fluid through the pump. These pumps are ideal for low-viscosity fluids and applications requiring high flow rates. However, they may not be suitable for high-viscosity or high-pressure applications.
Positive Displacement Pumps
Positive displacement pumps move fluid by trapping a fixed amount and forcing it through the pump’s discharge. This type of pump is well-suited for high-viscosity fluids and applications requiring precise flow control. Examples include gear pumps, diaphragm pumps, and peristaltic pumps. They are often used in industries such as food processing, pharmaceuticals, and chemical manufacturing.
Peristaltic Pumps
Peristaltic pumps are a type of positive displacement pump that uses a rotating mechanism to compress a flexible tube, pushing the fluid through. These pumps are ideal for handling abrasive or shear-sensitive fluids, as the fluid only comes into contact with the tubing. They are commonly used in medical, laboratory, and chemical applications.
Diaphragm Pumps
Diaphragm pumps use a flexible diaphragm to move fluid in and out of a chamber. They are highly versatile and can handle a wide range of fluid types, including corrosive and viscous substances. Diaphragm pumps are often used in applications where leak prevention and chemical resistance are critical.
Operational Requirements and Considerations
In addition to fluid properties and pump types, several operational requirements and considerations must be taken into account when selecting an industrial pump. These factors will help ensure that the chosen pump meets the specific needs of your application:
Flow Rate and Pressure
The required flow rate and pressure are fundamental factors in pump selection. The flow rate determines how much fluid needs to be moved within a specific time frame, while pressure indicates the force required to move the fluid through the system. It is essential to choose a pump that can deliver the desired flow rate and pressure without compromising efficiency or reliability.
Energy Efficiency
Energy efficiency is a critical consideration for reducing operational costs and minimizing environmental impact. Selecting a pump with high energy efficiency can lead to significant savings over time. Look for pumps with energy-efficient motors and designs that minimize energy loss during operation.
Maintenance and Reliability
Regular maintenance is essential to ensure the longevity and reliability of industrial pumps. Consider the ease of maintenance and availability of spare parts when selecting a pump. Pumps with simple designs and readily available components can reduce downtime and maintenance costs.
Installation and Space Requirements
The installation process and space requirements should also be considered when choosing an industrial pump. Ensure that the pump can be easily integrated into your existing system and that there is sufficient space for installation and maintenance. Compact pump designs can be advantageous in facilities with limited space.
Conclusion
Choosing the right industrial pump for your application involves a thorough understanding of fluid properties, pump types, and operational requirements. By carefully considering these factors, you can select a pump that meets your specific needs, ensuring efficient and cost-effective operation. Whether you are dealing with high-viscosity fluids, corrosive substances, or require precise flow control, there is a pump solution available to suit your application. Investing time in selecting the right pump will pay off in terms of performance, reliability, and overall operational success.