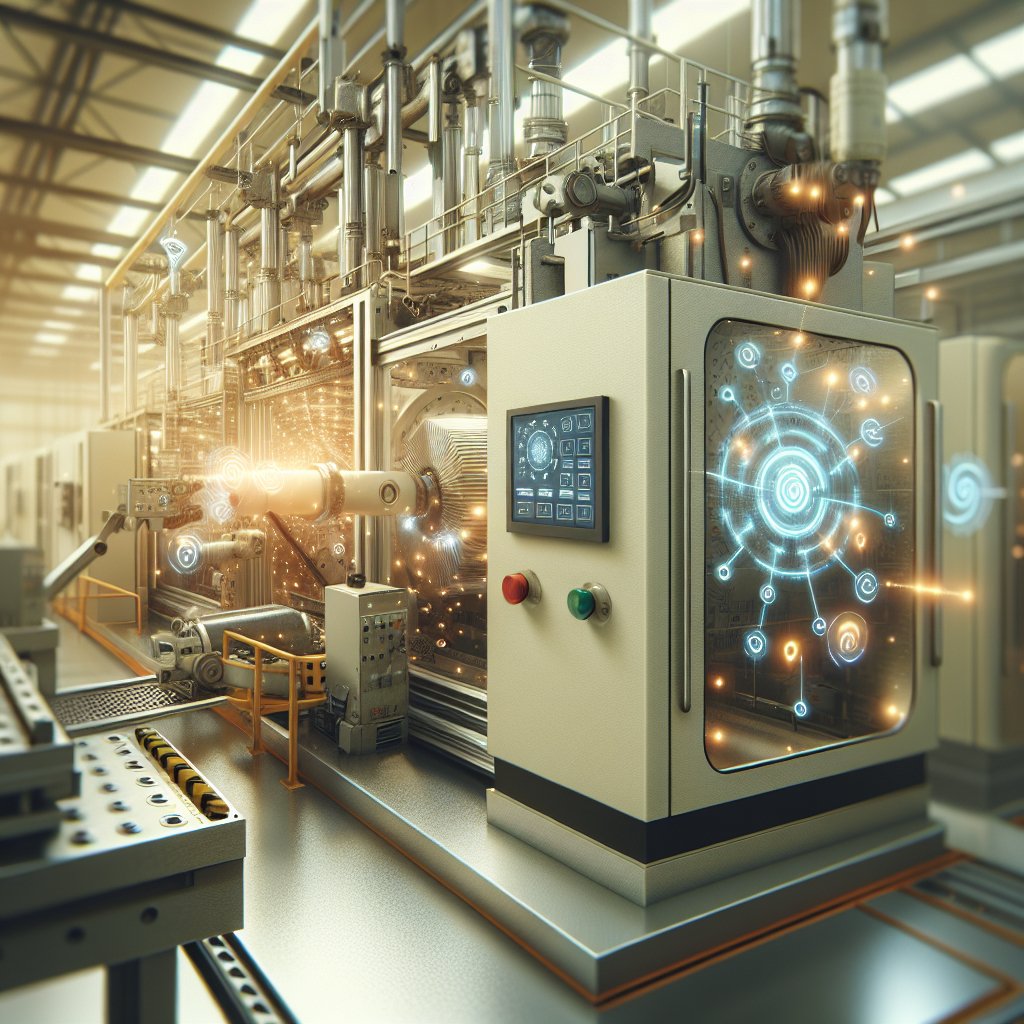
Wireless sensors have revolutionized the way industrial equipment is monitored and maintained, offering numerous benefits that enhance efficiency, safety, and cost-effectiveness. As industries continue to evolve, the integration of wireless technology into equipment monitoring systems has become increasingly prevalent, providing real-time data and insights that were previously unattainable. This article delves into the various advantages of using wireless sensors in industrial settings, exploring how they contribute to improved operational performance and decision-making.
Enhanced Monitoring and Data Collection
One of the primary benefits of wireless sensors in industrial equipment is the enhanced ability to monitor and collect data. Traditional wired systems often face limitations in terms of installation complexity and data transmission capabilities. Wireless sensors, on the other hand, offer a more flexible and scalable solution. They can be easily installed in hard-to-reach areas and can transmit data over long distances without the need for extensive cabling.
Wireless sensors provide continuous, real-time monitoring of various parameters such as temperature, pressure, vibration, and humidity. This constant stream of data allows for more accurate and timely analysis, enabling operators to detect anomalies and potential issues before they escalate into major problems. The ability to monitor equipment conditions in real-time also facilitates predictive maintenance strategies, reducing downtime and extending the lifespan of machinery.
Scalability and Flexibility
The scalability and flexibility of wireless sensor networks are significant advantages for industrial applications. As operations grow or change, additional sensors can be easily integrated into the existing network without the need for extensive reconfiguration. This adaptability is particularly beneficial in dynamic industrial environments where equipment and processes are frequently updated or expanded.
Moreover, wireless sensors can be deployed in a wide range of environments, from harsh outdoor conditions to confined indoor spaces. Their ability to operate in diverse settings makes them suitable for various industries, including manufacturing, oil and gas, agriculture, and logistics. This versatility ensures that businesses can tailor their monitoring systems to meet specific operational needs and challenges.
Improved Safety and Risk Management
Safety is a paramount concern in industrial settings, and wireless sensors play a crucial role in enhancing workplace safety and risk management. By providing real-time data on equipment conditions, these sensors enable operators to identify potential hazards and take corrective actions promptly. For instance, sensors can detect abnormal temperature rises in machinery, indicating overheating or potential fire risks, allowing for immediate intervention.
Wireless sensors also contribute to improved safety by reducing the need for manual inspections in hazardous areas. Workers can monitor equipment remotely, minimizing their exposure to dangerous environments and reducing the likelihood of accidents. This remote monitoring capability is particularly valuable in industries such as mining, chemical processing, and offshore drilling, where safety risks are inherently higher.
Compliance and Reporting
In addition to enhancing safety, wireless sensors assist in ensuring compliance with industry regulations and standards. Many industries are subject to stringent safety and environmental regulations that require regular monitoring and reporting of equipment conditions. Wireless sensors automate the data collection process, ensuring accurate and consistent reporting without the need for manual intervention.
The data collected by wireless sensors can be easily integrated into compliance management systems, streamlining the reporting process and reducing the risk of human error. This automation not only saves time and resources but also provides a reliable audit trail for regulatory inspections and assessments.
Cost-Effectiveness and Operational Efficiency
Implementing wireless sensors in industrial equipment can lead to significant cost savings and operational efficiencies. By enabling predictive maintenance strategies, these sensors help reduce unplanned downtime and maintenance costs. Predictive maintenance involves analyzing sensor data to identify patterns and trends that indicate potential equipment failures, allowing for timely maintenance interventions before breakdowns occur.
Wireless sensors also contribute to energy efficiency by monitoring and optimizing equipment performance. For example, sensors can track energy consumption patterns and identify areas where energy is being wasted, enabling operators to implement energy-saving measures. This optimization not only reduces operational costs but also supports sustainability initiatives by minimizing the environmental impact of industrial activities.
Reduced Installation and Maintenance Costs
The installation and maintenance of wireless sensor networks are generally more cost-effective compared to traditional wired systems. The absence of extensive cabling reduces installation time and labor costs, while the wireless nature of the sensors simplifies maintenance and troubleshooting. In the event of a sensor failure, replacement is straightforward and does not require complex rewiring.
Furthermore, wireless sensors often have lower power requirements and longer battery life, reducing the frequency of battery replacements and associated maintenance costs. Some sensors are equipped with energy-harvesting capabilities, further extending their operational lifespan and reducing the need for external power sources.
Conclusion
The integration of wireless sensors into industrial equipment offers a multitude of benefits that enhance monitoring, safety, and operational efficiency. By providing real-time data and insights, these sensors enable businesses to make informed decisions, optimize processes, and reduce costs. As technology continues to advance, the adoption of wireless sensors in industrial settings is expected to grow, driving further innovation and improvements in equipment monitoring and management.
In conclusion, wireless sensors represent a transformative technology that is reshaping the landscape of industrial operations. Their ability to provide continuous, accurate, and reliable data empowers businesses to achieve greater efficiency, safety, and sustainability, ultimately contributing to a more competitive and resilient industrial sector.