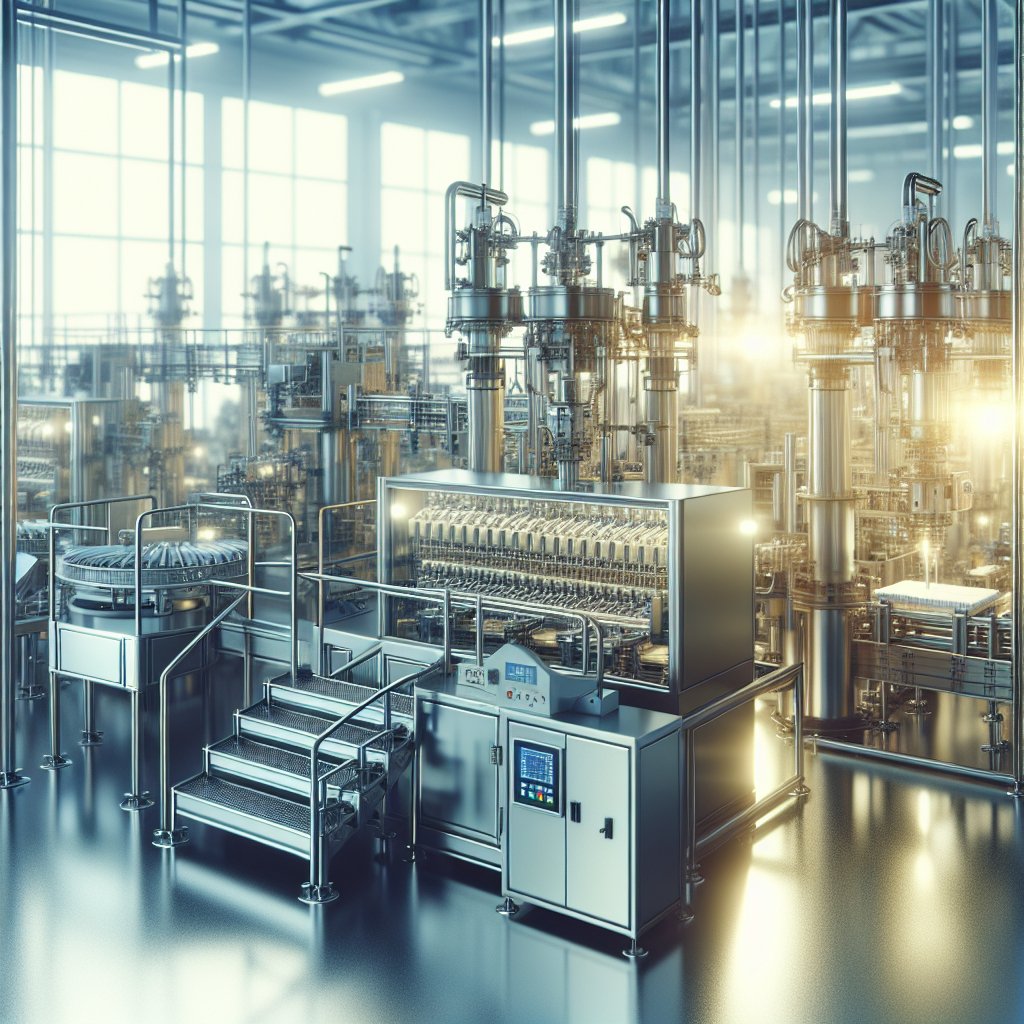
Industrial automation has revolutionized the food and beverage industry, enhancing efficiency, safety, and product quality. As technology continues to advance, the integration of automated systems in food production processes has become increasingly prevalent, offering numerous benefits to manufacturers and consumers alike. This article delves into the various aspects of industrial automation within the food and beverage sector, exploring its impact on production, quality control, and sustainability.
The Role of Automation in Food Production
Automation in food production encompasses a wide range of technologies and systems designed to streamline operations, reduce human error, and increase output. From robotic arms handling packaging to automated sorting systems, the implementation of these technologies has transformed traditional manufacturing processes.
Enhancing Efficiency and Productivity
One of the primary advantages of industrial automation is the significant boost in efficiency and productivity. Automated systems can operate continuously without the need for breaks, unlike human workers. This constant operation allows for higher production rates and the ability to meet increasing consumer demands. Additionally, automation reduces the likelihood of errors that can occur with manual labor, ensuring consistent product quality.
For instance, automated conveyor systems can transport raw materials and finished products throughout a facility with precision and speed. This not only minimizes the time required for transportation but also reduces the risk of contamination and damage to products. Furthermore, automated machinery can perform repetitive tasks with high accuracy, freeing up human workers to focus on more complex and value-added activities.
Improving Quality Control
Quality control is a critical aspect of the food and beverage industry, as it directly impacts consumer safety and satisfaction. Automation plays a vital role in maintaining high standards of quality by implementing advanced monitoring and inspection systems. These systems utilize sensors, cameras, and software to detect defects, contaminants, and inconsistencies in products.
For example, automated vision systems can inspect products for size, shape, and color, ensuring that only items meeting specific criteria proceed to the next stage of production. This level of scrutiny is difficult to achieve with manual inspection alone, as human inspectors may overlook subtle defects or become fatigued over time. By integrating automated quality control measures, manufacturers can reduce waste, minimize recalls, and enhance their brand reputation.
Sustainability and Environmental Impact
As the food and beverage industry faces increasing pressure to adopt sustainable practices, automation offers solutions to reduce environmental impact. Automated systems can optimize resource usage, minimize waste, and improve energy efficiency, contributing to a more sustainable production process.
Resource Optimization
Automation enables precise control over the use of raw materials, water, and energy, reducing waste and conserving resources. For instance, automated dosing systems can accurately measure and dispense ingredients, ensuring that only the necessary amounts are used. This not only reduces material waste but also enhances product consistency and quality.
Moreover, automated systems can monitor and adjust energy consumption in real-time, optimizing processes to minimize energy usage. This is particularly important in energy-intensive operations such as refrigeration and cooking, where even small improvements can lead to significant energy savings.
Reducing Waste and Emissions
By improving process efficiency and product quality, automation can significantly reduce waste generation. Automated sorting and grading systems can separate defective products early in the production process, preventing them from reaching the final stages and reducing the volume of waste. Additionally, automation can facilitate the recycling and reuse of by-products, further minimizing waste.
Furthermore, automation can help reduce greenhouse gas emissions by optimizing transportation and logistics. Automated systems can plan and execute efficient routes for the movement of goods, reducing fuel consumption and emissions. This is particularly relevant in the food and beverage industry, where the transportation of perishable goods requires careful planning to maintain product quality while minimizing environmental impact.
Challenges and Future Prospects
While the benefits of industrial automation in the food and beverage industry are substantial, there are also challenges that manufacturers must address. The initial investment in automated systems can be significant, and companies must carefully evaluate the return on investment. Additionally, the integration of automation requires skilled personnel to manage and maintain the systems, necessitating training and development programs.
Overcoming Implementation Barriers
To successfully implement automation, manufacturers must overcome several barriers, including cost, complexity, and resistance to change. The high upfront cost of automated systems can be a deterrent for small and medium-sized enterprises (SMEs). However, the long-term benefits of increased efficiency, reduced waste, and improved quality can outweigh the initial investment.
Complexity is another challenge, as integrating automation into existing processes requires careful planning and execution. Manufacturers must ensure that automated systems are compatible with current operations and that they do not disrupt production. This may involve redesigning workflows, updating infrastructure, and investing in new technologies.
Resistance to change is a common obstacle in the adoption of automation. Employees may fear job loss or feel uncertain about new technologies. To address these concerns, companies should focus on communication and training, highlighting the benefits of automation and providing opportunities for skill development. By involving employees in the transition process, manufacturers can foster a culture of innovation and collaboration.
The Future of Automation in the Industry
As technology continues to evolve, the future of industrial automation in the food and beverage industry looks promising. Advances in artificial intelligence, machine learning, and the Internet of Things (IoT) are expected to further enhance automation capabilities, enabling more sophisticated and adaptive systems.
AI and machine learning can improve decision-making processes by analyzing vast amounts of data and identifying patterns and trends. This can lead to more efficient production schedules, optimized resource allocation, and predictive maintenance, reducing downtime and increasing productivity.
The IoT can connect various components of the production process, allowing for real-time monitoring and control. This connectivity can enhance traceability, improve supply chain management, and enable more responsive and agile operations.
In conclusion, industrial automation is transforming the food and beverage industry, offering numerous benefits in terms of efficiency, quality, and sustainability. While challenges remain, the continued advancement of technology and the growing demand for sustainable practices are likely to drive further adoption of automation in the sector. By embracing these changes, manufacturers can enhance their competitiveness and meet the evolving needs of consumers.