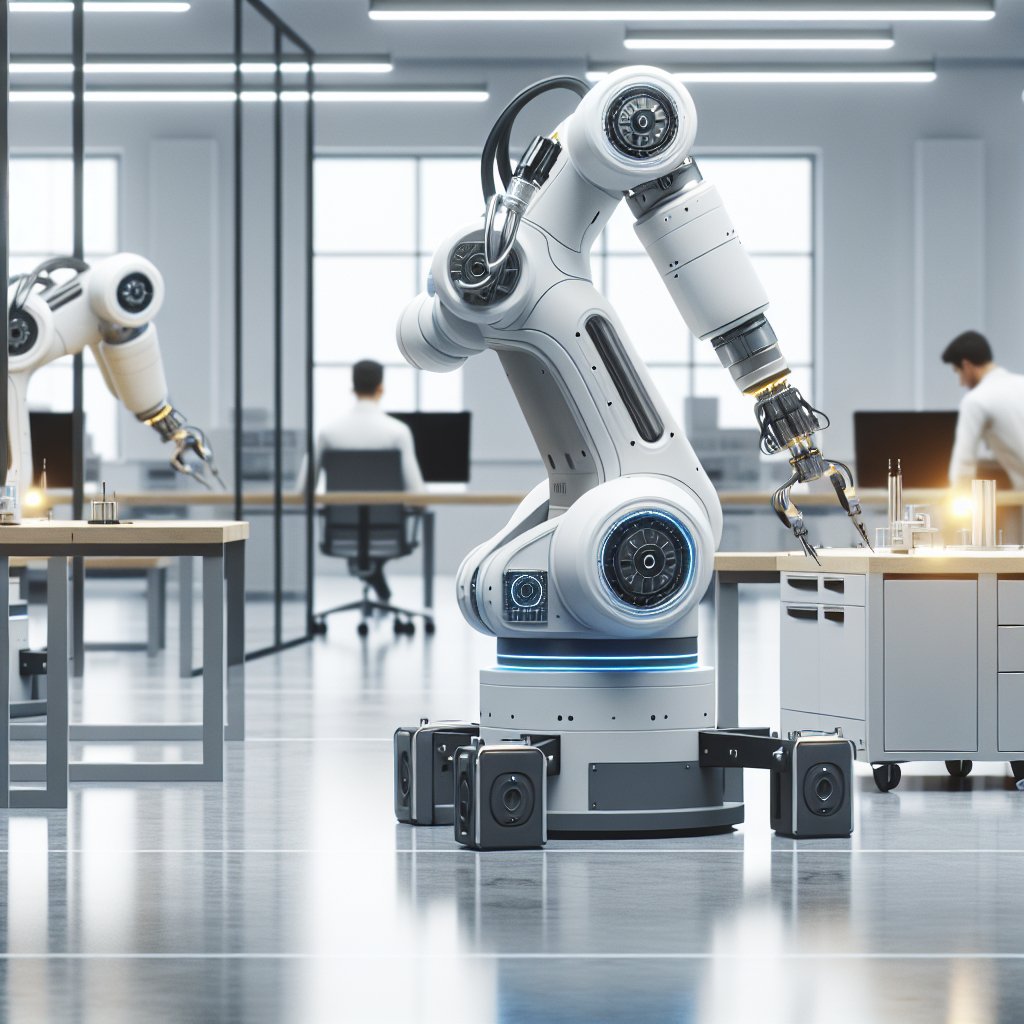
Collaborative robots, often referred to as cobots, are revolutionizing industries by enhancing worker safety and efficiency. These advanced machines are designed to work alongside humans, offering a new level of interaction and cooperation in various sectors. As technology continues to evolve, the integration of cobots into the workplace is becoming increasingly prevalent, providing numerous benefits and transforming traditional work environments.
The Rise of Collaborative Robots
The concept of collaborative robots emerged as a response to the limitations of traditional industrial robots, which were often isolated from human workers due to safety concerns. Unlike their predecessors, cobots are equipped with advanced sensors and software that allow them to operate safely in close proximity to humans. This innovation has opened up new possibilities for automation, enabling businesses to optimize their operations while maintaining a human touch.
One of the key factors driving the adoption of cobots is their ability to perform repetitive and physically demanding tasks with precision and consistency. This not only reduces the risk of human error but also minimizes the potential for workplace injuries. By taking on these tasks, cobots free up human workers to focus on more complex and creative aspects of their jobs, ultimately leading to increased productivity and job satisfaction.
Enhancing Worker Safety
Worker safety is a paramount concern in any industry, and collaborative robots play a crucial role in mitigating risks associated with manual labor. Traditional industrial robots often require safety barriers and extensive safety protocols to prevent accidents. In contrast, cobots are designed with built-in safety features that allow them to detect and respond to human presence, significantly reducing the likelihood of accidents.
For instance, cobots are equipped with force-limiting technology that enables them to stop or slow down when they come into contact with a human. This feature ensures that any unintended interaction between a cobot and a worker is gentle and unlikely to cause harm. Additionally, cobots can be programmed to operate at reduced speeds when working in close proximity to humans, further enhancing safety.
Moreover, the use of cobots can help prevent musculoskeletal disorders and other injuries associated with repetitive tasks. By automating these tasks, businesses can reduce the physical strain on workers, leading to a healthier and more sustainable workforce. This not only benefits employees but also reduces costs related to workplace injuries and absenteeism.
Boosting Efficiency and Productivity
In addition to improving safety, collaborative robots are instrumental in boosting efficiency and productivity across various industries. Their ability to work alongside humans allows for seamless integration into existing workflows, enhancing overall operational efficiency. Cobots can be easily programmed and reprogrammed to perform a wide range of tasks, making them highly adaptable to changing production needs.
One of the significant advantages of cobots is their ability to operate continuously without fatigue. This means that businesses can maintain high levels of productivity even during extended shifts or peak production periods. By taking on routine and time-consuming tasks, cobots enable human workers to focus on more strategic and value-added activities, such as problem-solving and innovation.
Furthermore, the precision and accuracy of cobots contribute to improved product quality and consistency. By minimizing human error, businesses can reduce waste and rework, leading to cost savings and increased customer satisfaction. The ability to maintain high-quality standards is particularly crucial in industries such as manufacturing, where even minor defects can have significant consequences.
Applications Across Industries
The versatility of collaborative robots makes them suitable for a wide range of applications across various industries. In manufacturing, cobots are used for tasks such as assembly, packaging, and quality inspection. Their ability to handle delicate components with precision makes them ideal for industries such as electronics and automotive manufacturing.
In the healthcare sector, cobots are being utilized to assist with tasks such as medication dispensing, patient monitoring, and even surgery. Their precision and reliability make them valuable assets in environments where accuracy is critical. Additionally, cobots can help alleviate the workload of healthcare professionals, allowing them to focus on patient care and other essential duties.
The logistics and warehousing industry is another area where cobots are making a significant impact. They are used for tasks such as picking, packing, and sorting, streamlining operations and reducing the time required to fulfill orders. This is particularly beneficial in e-commerce, where rapid order fulfillment is essential to meet customer expectations.
Challenges and Considerations
While the benefits of collaborative robots are undeniable, their integration into the workplace is not without challenges. One of the primary concerns is the potential impact on employment, as automation may lead to job displacement in certain sectors. However, it is essential to recognize that cobots are designed to complement human workers, not replace them. By taking on repetitive and mundane tasks, cobots allow workers to focus on more meaningful and fulfilling roles.
Another consideration is the initial cost of implementing cobots, which can be a barrier for some businesses. However, the long-term benefits, such as increased productivity, reduced labor costs, and improved safety, often outweigh the initial investment. Additionally, advancements in technology are making cobots more affordable and accessible to businesses of all sizes.
Training and upskilling are also crucial to ensure that workers can effectively collaborate with cobots. Businesses must invest in training programs to equip their workforce with the necessary skills to operate and interact with these advanced machines. This not only enhances the efficiency of cobot integration but also empowers workers to embrace new technologies and adapt to changing work environments.
The Future of Collaborative Robotics
The future of collaborative robotics is promising, with ongoing advancements in technology and increasing adoption across industries. As cobots become more sophisticated and capable, their applications will continue to expand, offering new opportunities for businesses to enhance their operations and remain competitive in a rapidly evolving market.
One area of development is the integration of artificial intelligence and machine learning into cobots, enabling them to learn and adapt to new tasks autonomously. This will further enhance their versatility and efficiency, allowing businesses to optimize their operations and respond to changing demands more effectively.
Additionally, the development of more intuitive and user-friendly interfaces will make it easier for workers to interact with cobots, reducing the learning curve and facilitating seamless integration into the workplace. This will empower businesses to harness the full potential of collaborative robotics and drive innovation across various sectors.
In conclusion, collaborative robots are transforming industries by enhancing worker safety and efficiency. Their ability to work alongside humans, coupled with their versatility and adaptability, makes them valuable assets in today’s dynamic work environments. As technology continues to advance, the role of cobots in the workplace will only grow, offering new possibilities for businesses to thrive in an increasingly competitive landscape.