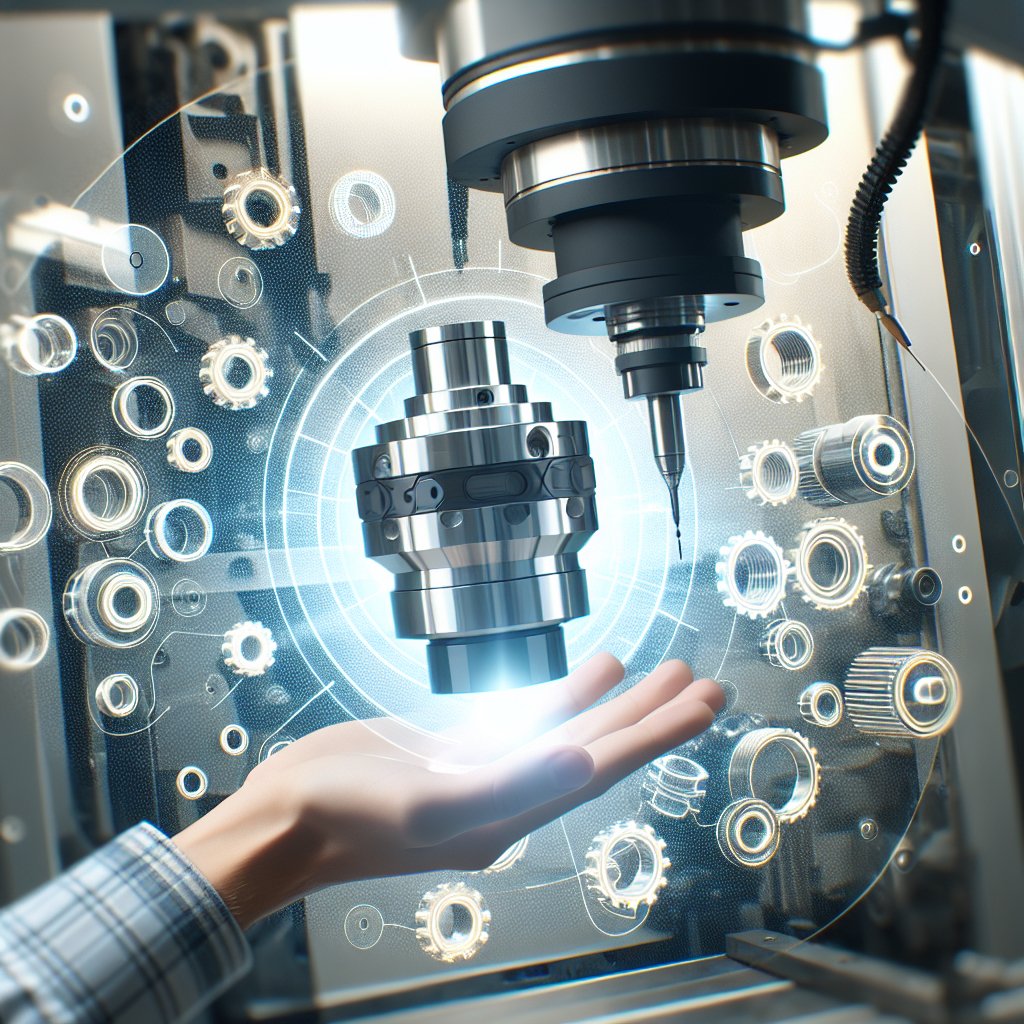
Advancements in CNC machine tools have revolutionized precision manufacturing, offering unprecedented levels of accuracy, efficiency, and versatility. As industries continue to demand higher quality and more complex components, CNC technology has evolved to meet these challenges, providing solutions that were once thought impossible. This article delves into the latest developments in CNC machine tools, exploring how these innovations are shaping the future of manufacturing.
Evolution of CNC Technology
The journey of CNC (Computer Numerical Control) technology began in the mid-20th century, transforming traditional machining processes by introducing automation and computer control. Initially, CNC machines were limited in their capabilities, primarily used for simple tasks such as drilling and milling. However, as computer technology advanced, so did the capabilities of CNC machines.
Today, CNC machines are integral to modern manufacturing, capable of producing intricate designs with remarkable precision. The integration of advanced software and hardware has enabled these machines to perform complex operations, such as multi-axis machining, which allows for the creation of complex geometries that were previously unattainable. This evolution has been driven by the need for higher precision, faster production times, and reduced human error.
Key Technological Developments
Several key technological advancements have propelled CNC machine tools to the forefront of precision manufacturing. One of the most significant developments is the integration of high-speed machining capabilities. High-speed CNC machines can operate at much higher spindle speeds, allowing for faster material removal rates and reduced cycle times. This not only increases productivity but also enhances the surface finish of the machined parts.
Another critical advancement is the implementation of multi-axis machining. Traditional CNC machines typically operate on three axes (X, Y, and Z), but modern machines can operate on five or more axes. This capability allows for the machining of complex shapes and contours in a single setup, reducing the need for multiple fixtures and setups. As a result, manufacturers can produce parts with greater accuracy and consistency.
Additionally, the integration of advanced software solutions has played a crucial role in the evolution of CNC technology. Modern CNC machines are equipped with sophisticated CAD/CAM software that enables seamless design and manufacturing processes. These software solutions allow for the simulation and optimization of machining operations, ensuring that the final product meets the desired specifications.
Impact on Precision Manufacturing
The advancements in CNC machine tools have had a profound impact on precision manufacturing, enabling industries to produce high-quality components with exceptional accuracy. One of the most significant benefits of CNC technology is its ability to produce parts with tight tolerances, which is essential in industries such as aerospace, automotive, and medical device manufacturing.
In the aerospace industry, for example, the demand for lightweight and high-strength components has driven the need for precision machining. CNC machines are capable of producing complex components with minimal material waste, ensuring that the final product meets the stringent requirements of the industry. Similarly, in the medical device industry, CNC technology is used to manufacture intricate components such as surgical instruments and implants, where precision is critical to ensure patient safety and efficacy.
Challenges and Future Prospects
Despite the numerous advantages of CNC technology, there are still challenges that need to be addressed. One of the primary challenges is the high cost of CNC machines and the associated software. While the initial investment can be substantial, the long-term benefits in terms of productivity and quality often outweigh the costs. However, for small and medium-sized enterprises, the financial barrier can be significant.
Another challenge is the need for skilled operators and programmers. As CNC machines become more sophisticated, the demand for skilled personnel who can operate and program these machines increases. This has led to a growing emphasis on education and training programs to ensure that the workforce is equipped with the necessary skills to meet the demands of modern manufacturing.
Looking to the future, the prospects for CNC technology are promising. The continued integration of artificial intelligence and machine learning is expected to further enhance the capabilities of CNC machines, enabling them to perform more complex tasks with greater efficiency. Additionally, the development of new materials and manufacturing techniques, such as additive manufacturing, is likely to complement CNC technology, offering new possibilities for precision manufacturing.
In conclusion, the advancements in CNC machine tools have transformed precision manufacturing, offering unprecedented levels of accuracy and efficiency. As technology continues to evolve, CNC machines will play an increasingly vital role in meeting the demands of modern industries, paving the way for new innovations and opportunities in the manufacturing sector.