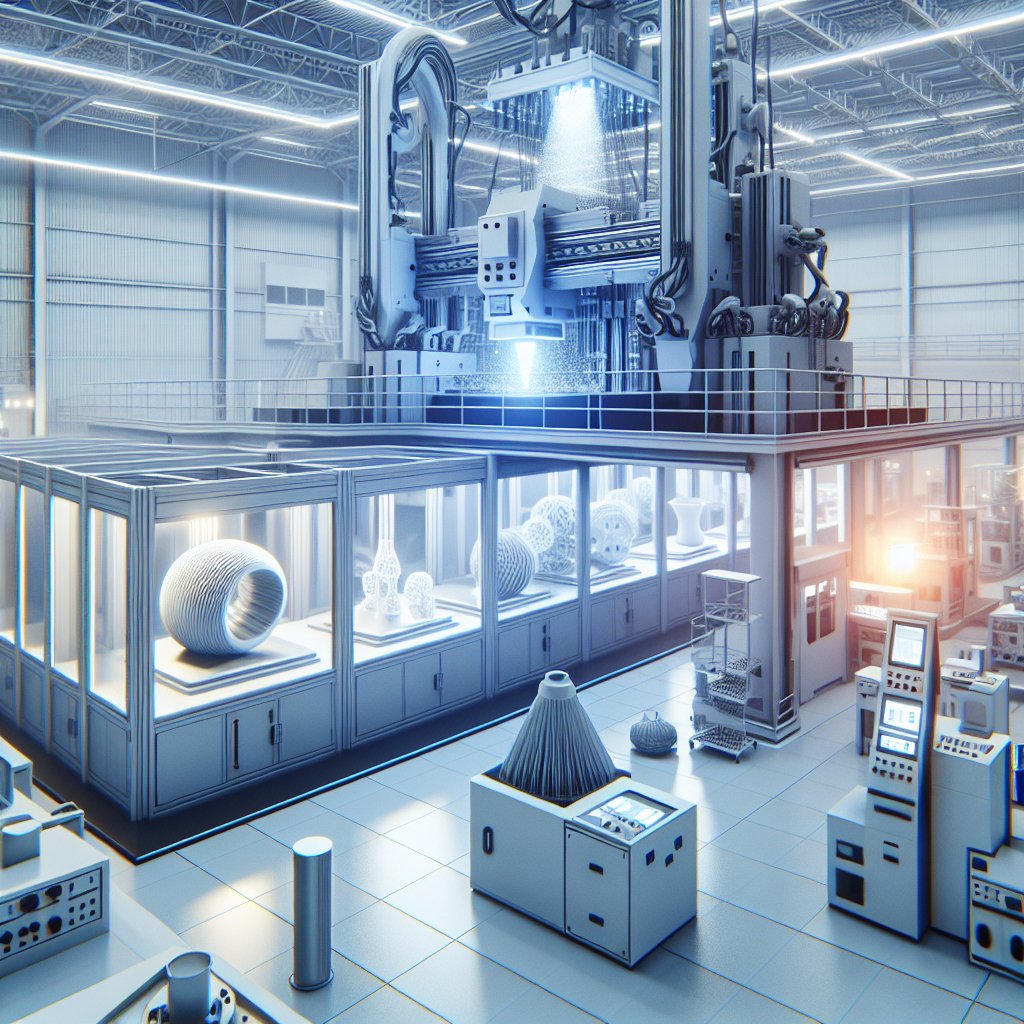
Additive manufacturing, commonly known as 3D printing, is transforming the landscape of industrial production by offering unprecedented flexibility, efficiency, and customization. This innovative technology is not only reshaping how products are designed and manufactured but also redefining the very nature of production processes across various industries. From aerospace to healthcare, additive manufacturing is paving the way for a new era of industrial capabilities.
The Fundamentals of Additive Manufacturing
Additive manufacturing is a process that creates objects by adding material layer by layer, based on digital models. Unlike traditional manufacturing methods, which often involve subtracting material from a larger block, additive manufacturing builds objects from the ground up. This approach allows for greater design freedom, reduced material waste, and the ability to produce complex geometries that would be difficult or impossible to achieve with conventional techniques.
The process begins with a digital 3D model, which is typically created using computer-aided design (CAD) software. This model is then sliced into thin horizontal layers, and the additive manufacturing machine follows these instructions to deposit material layer by layer. The materials used in additive manufacturing can vary widely, including plastics, metals, ceramics, and even biological materials, depending on the application and desired properties of the final product.
One of the key advantages of additive manufacturing is its ability to produce highly customized products. Because the process is driven by digital models, it is relatively easy to modify designs and create unique items tailored to specific needs. This capability is particularly valuable in industries such as healthcare, where personalized medical devices and implants can significantly improve patient outcomes.
Applications and Impact Across Industries
Additive manufacturing is making a significant impact across a wide range of industries, each benefiting from the unique advantages this technology offers. In the aerospace sector, for example, additive manufacturing is used to produce lightweight, high-strength components that contribute to fuel efficiency and performance improvements. The ability to create complex geometries also allows for the integration of multiple parts into a single component, reducing assembly time and costs.
In the automotive industry, additive manufacturing is being used to produce prototypes, tooling, and even end-use parts. The technology enables rapid prototyping, allowing designers and engineers to iterate quickly and bring new products to market faster. Additionally, the ability to produce parts on-demand reduces the need for large inventories and can lead to more efficient supply chains.
The healthcare industry is another area where additive manufacturing is having a profound impact. The technology is used to create custom prosthetics, dental implants, and even bioprinted tissues and organs. These applications not only improve patient care but also open up new possibilities for medical research and treatment.
Beyond these industries, additive manufacturing is also being explored in fields such as construction, fashion, and consumer goods. In construction, 3D printing is being used to create building components and even entire structures, offering the potential for more sustainable and efficient building practices. In fashion, designers are experimenting with 3D-printed garments and accessories, pushing the boundaries of creativity and personalization.
Challenges and Future Prospects
Despite its many advantages, additive manufacturing also faces several challenges that must be addressed to fully realize its potential. One of the primary challenges is the speed of production. While additive manufacturing is well-suited for producing small batches and customized items, it can be slower than traditional methods for mass production. Researchers and companies are actively working on developing faster printing technologies and optimizing processes to overcome this limitation.
Another challenge is the cost of materials and equipment. While the cost of 3D printers has decreased over the years, high-quality machines and materials can still be expensive. As the technology continues to mature, it is expected that these costs will decrease, making additive manufacturing more accessible to a wider range of businesses and industries.
Quality control and standardization are also important considerations. Ensuring consistent quality and performance of 3D-printed parts is crucial, especially in industries with strict regulatory requirements, such as aerospace and healthcare. Efforts are underway to develop industry standards and certification processes to address these concerns.
Looking to the future, additive manufacturing holds immense potential to revolutionize industrial production even further. Advances in materials science, machine learning, and automation are expected to enhance the capabilities of 3D printing, enabling the production of even more complex and functional parts. As the technology continues to evolve, it is likely to play an increasingly important role in sustainable manufacturing practices, reducing waste and energy consumption.
In conclusion, additive manufacturing is a transformative technology that is reshaping the industrial landscape. Its ability to offer customization, reduce waste, and create complex geometries is driving innovation across multiple sectors. While challenges remain, the ongoing advancements in this field promise to unlock new possibilities and redefine the future of manufacturing.