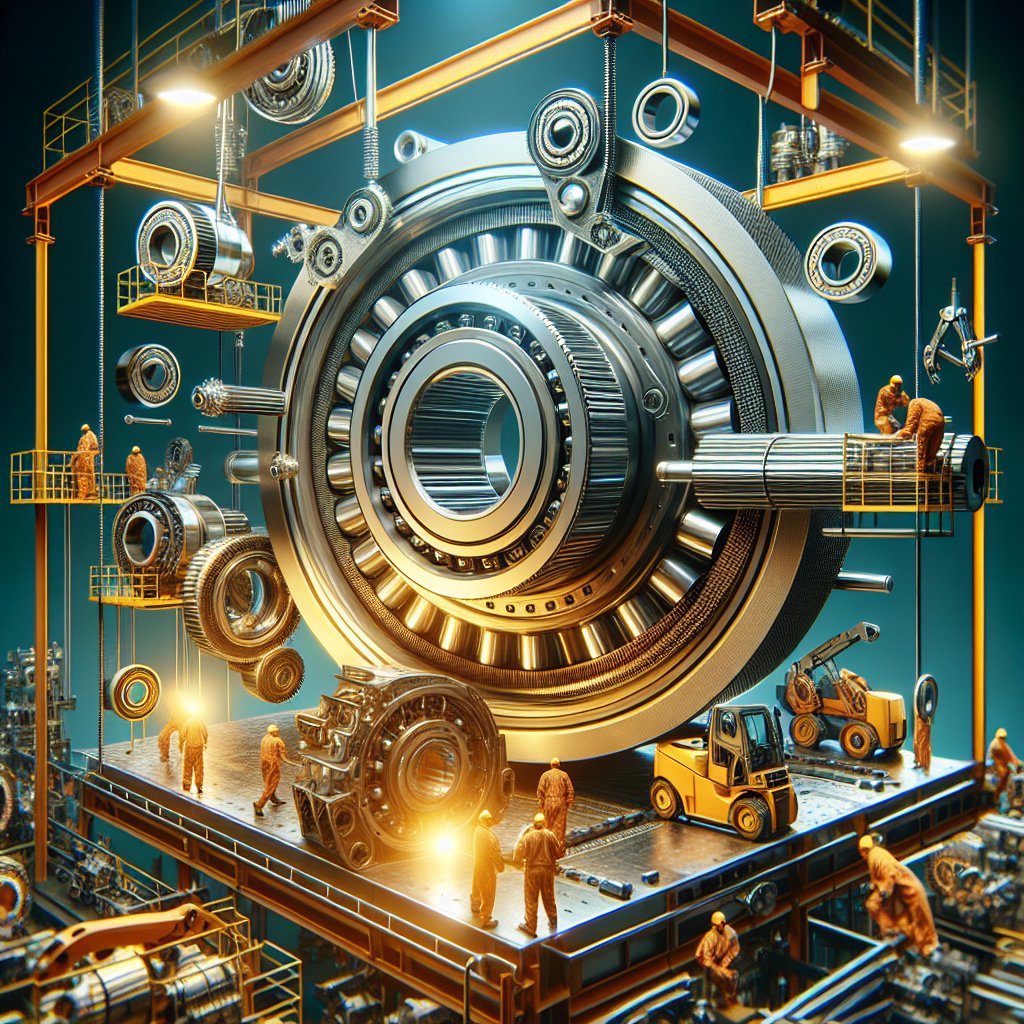
Industrial bearings are crucial components in machinery, playing a vital role in reducing friction between moving parts and supporting loads. Their selection and maintenance are essential for ensuring the efficiency and longevity of industrial equipment. This guide delves into the various types of industrial bearings, their applications, and the best practices for maintaining them.
Types of Industrial Bearings
Understanding the different types of industrial bearings is fundamental to selecting the right one for a specific application. Each type has unique characteristics that make it suitable for particular conditions and requirements.
Ball Bearings
Ball bearings are among the most common types of bearings used in industrial applications. They consist of balls that reduce friction between the bearing races. Ball bearings are versatile and can handle both radial and axial loads, making them suitable for a wide range of applications, from electric motors to automotive wheels.
- Deep Groove Ball Bearings: These are the most widely used ball bearings, known for their ability to handle high speeds and radial loads. They are commonly found in household appliances, electric motors, and gearboxes.
- Angular Contact Ball Bearings: Designed to handle both radial and axial loads, these bearings are ideal for applications requiring high precision and speed, such as machine tool spindles.
- Self-Aligning Ball Bearings: These bearings can accommodate misalignment between the shaft and housing, making them suitable for applications where alignment is challenging, such as in agricultural machinery.
Roller Bearings
Roller bearings use cylindrical, spherical, or tapered rollers instead of balls to reduce friction. They are designed to handle heavier loads than ball bearings and are often used in heavy-duty applications.
- Cylindrical Roller Bearings: These bearings are ideal for applications with high radial loads and moderate speeds, such as in conveyor belt systems and large electric motors.
- Spherical Roller Bearings: Known for their ability to handle both radial and axial loads, these bearings are used in applications with heavy loads and misalignment, such as in mining and construction equipment.
- Tapered Roller Bearings: These bearings can handle high radial and axial loads, making them suitable for automotive and industrial machinery applications, such as in wheel hubs and gearboxes.
Factors to Consider When Selecting Bearings
Choosing the right bearing for an application involves considering several factors to ensure optimal performance and longevity. Here are some key considerations:
Load Capacity
The load capacity of a bearing is a critical factor in its selection. It is essential to determine the type and magnitude of loads the bearing will encounter, including radial, axial, and combined loads. Bearings must be chosen based on their ability to handle these loads without compromising performance or lifespan.
Speed Requirements
The speed at which a bearing operates can significantly impact its performance. High-speed applications require bearings designed to minimize friction and heat generation. Ball bearings are generally preferred for high-speed applications, while roller bearings are better suited for lower-speed, high-load scenarios.
Environmental Conditions
The operating environment can affect bearing performance and longevity. Factors such as temperature, humidity, and exposure to contaminants like dust and chemicals must be considered. Bearings with appropriate seals and lubrication are essential for harsh environments to prevent premature wear and failure.
Alignment and Misalignment
Misalignment between the shaft and housing can lead to increased friction and wear. Bearings that can accommodate misalignment, such as self-aligning ball bearings or spherical roller bearings, are ideal for applications where perfect alignment is challenging to achieve.
Maintenance of Industrial Bearings
Proper maintenance is crucial for extending the life of industrial bearings and ensuring the reliability of machinery. Regular maintenance practices can prevent unexpected failures and costly downtime.
Lubrication
Lubrication is vital for reducing friction and wear in bearings. It is essential to use the correct type and amount of lubricant for the specific bearing and application. Regularly checking and replenishing lubricant levels can prevent overheating and extend bearing life.
Inspection and Monitoring
Regular inspection and monitoring of bearings can help identify potential issues before they lead to failure. Techniques such as vibration analysis, temperature monitoring, and visual inspections can detect signs of wear, misalignment, or lubrication problems.
Cleaning and Replacement
Keeping bearings clean and free from contaminants is essential for their longevity. In environments with high levels of dust or debris, regular cleaning may be necessary. Additionally, bearings should be replaced at the first sign of significant wear or damage to prevent further issues.
Conclusion
Industrial bearings are indispensable components in machinery, and their proper selection and maintenance are crucial for optimal performance and longevity. By understanding the different types of bearings, considering key factors during selection, and implementing regular maintenance practices, industries can ensure the reliability and efficiency of their equipment. Investing time and resources in bearing care can lead to significant cost savings and improved operational outcomes.