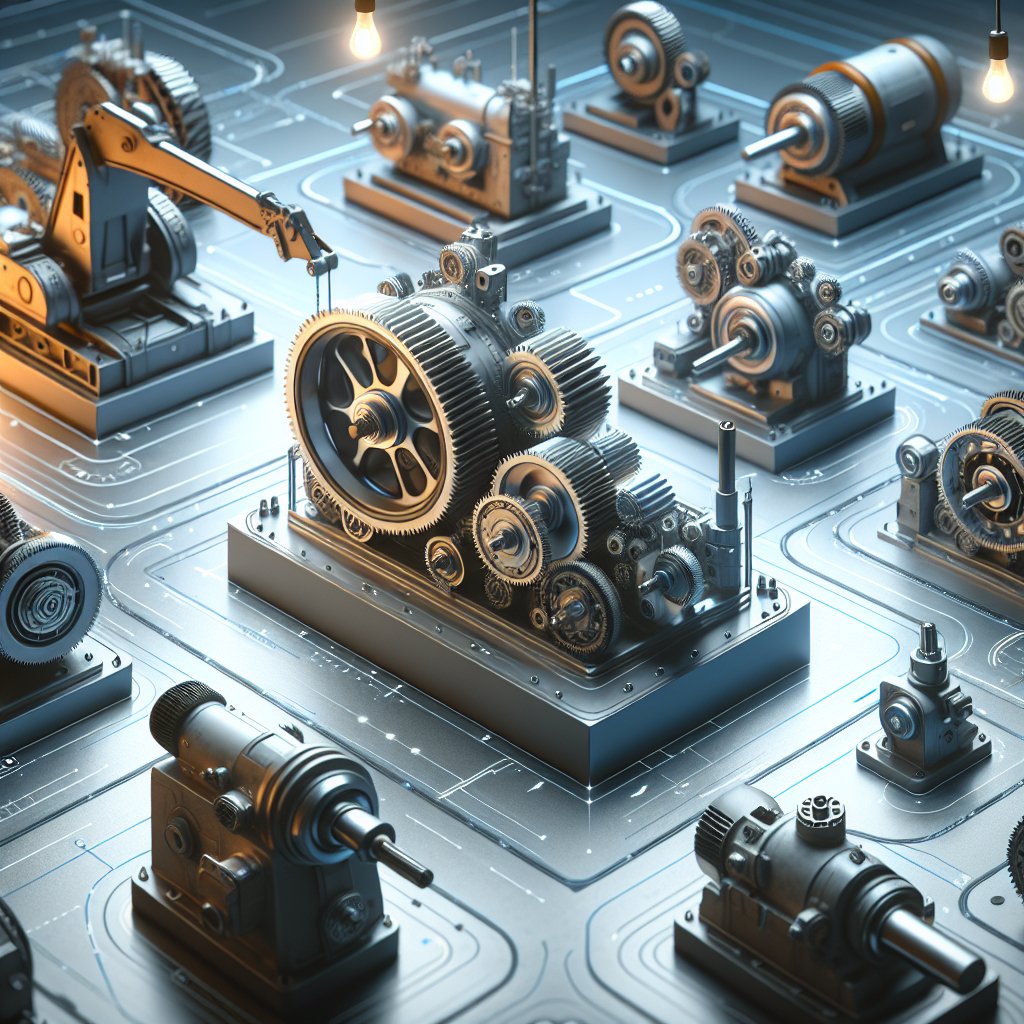
Choosing the right gearbox for industrial applications is a critical decision that can significantly impact the efficiency and longevity of machinery. Gearboxes are essential components in various industrial settings, providing the necessary torque and speed conversion to drive equipment effectively. This article delves into the key considerations and types of gearboxes available, helping you make an informed choice for your specific needs.
Understanding Gearbox Basics
Before diving into the selection process, it’s essential to understand the basic function and components of a gearbox. A gearbox, also known as a transmission, is a mechanical device that transfers power from an engine or motor to the output device, such as a conveyor belt or a pump. It adjusts the speed and torque of the motor to meet the operational requirements of the machinery.
Components of a Gearbox
A typical gearbox consists of several key components:
- Gears: These are the primary components that transmit power. They come in various types, including spur, helical, bevel, and worm gears, each offering different advantages and applications.
- Shafts: Shafts support the gears and transmit the rotational force. They are usually made of high-strength materials to withstand the stresses of operation.
- Bearings: Bearings reduce friction between moving parts, ensuring smooth operation and prolonging the life of the gearbox.
- Housing: The housing encloses the gears and other components, providing protection and support. It also helps in dissipating heat generated during operation.
Types of Gearboxes
There are several types of gearboxes, each suited for different applications:
- Helical Gearbox: Known for its efficiency and smooth operation, the helical gearbox is ideal for high-speed applications. Its angled teeth provide better contact and load distribution.
- Bevel Gearbox: This type is used when the direction of a shaft’s rotation needs to be changed. Bevel gearboxes are commonly found in automotive differentials.
- Worm Gearbox: Offering high torque reduction, worm gearboxes are suitable for applications requiring significant speed reduction and torque multiplication.
- Planetary Gearbox: Known for its compact size and high efficiency, the planetary gearbox is used in applications requiring high torque and precision.
Factors to Consider When Choosing a Gearbox
Selecting the right gearbox involves evaluating several factors to ensure optimal performance and longevity. Here are some critical considerations:
Load Requirements
Understanding the load requirements of your application is crucial. Consider both the maximum and average loads the gearbox will need to handle. Overloading a gearbox can lead to premature failure, while underloading can result in inefficiencies.
Speed and Torque
Determine the required output speed and torque for your application. The gearbox should be capable of converting the input speed and torque from the motor to the desired output levels. This involves selecting the appropriate gear ratio.
Environmental Conditions
The operating environment can significantly impact the performance and lifespan of a gearbox. Consider factors such as temperature, humidity, dust, and exposure to chemicals. Choose a gearbox with suitable materials and protection ratings to withstand these conditions.
Space and Weight Constraints
In some applications, space and weight are critical factors. Compact gearboxes, such as planetary gearboxes, are ideal for applications with limited space. Additionally, consider the weight of the gearbox, especially in mobile or portable applications.
Efficiency and Maintenance
Efficiency is a key consideration, as it affects energy consumption and operational costs. Look for gearboxes with high efficiency ratings to minimize energy loss. Additionally, consider the maintenance requirements and ease of access for servicing the gearbox.
Conclusion
Choosing the right gearbox for industrial applications requires a thorough understanding of the specific needs and constraints of your operation. By considering factors such as load requirements, speed and torque, environmental conditions, and efficiency, you can select a gearbox that will enhance the performance and reliability of your machinery. With the right gearbox, you can ensure smooth and efficient operation, reducing downtime and maintenance costs in the long run.