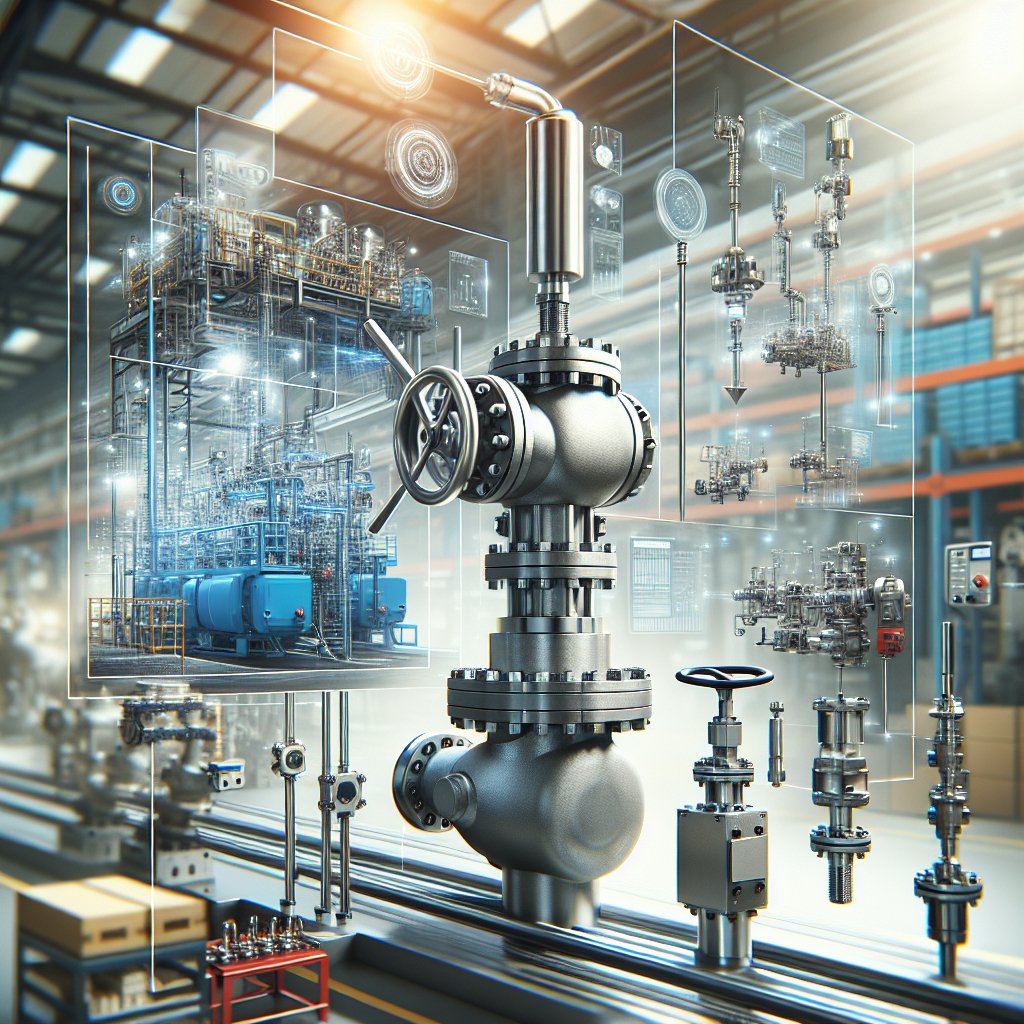
Industrial valves play a crucial role in manufacturing processes, serving as essential components that control the flow and pressure of liquids, gases, and slurries within a system. Selecting the right valve for a specific application is vital to ensure efficiency, safety, and cost-effectiveness. This comprehensive guide aims to provide insights into the various types of industrial valves, their applications, and key considerations for selecting the most suitable valve for your manufacturing needs.
Understanding Different Types of Industrial Valves
Industrial valves come in a variety of types, each designed to meet specific operational requirements. Understanding the differences between these valves is the first step in making an informed selection. Below, we explore some of the most common types of industrial valves used in manufacturing.
Gate Valves
Gate valves are primarily used to start or stop the flow of a fluid. They operate by lifting a gate out of the path of the fluid. These valves are ideal for applications where a straight-line flow of fluid and minimum restriction is desired. However, they are not suitable for throttling purposes as they can cause damage to the gate and seat.
Globe Valves
Globe valves are used for regulating flow in a pipeline. They offer good throttling capabilities and are commonly used in applications where flow control is required. The design of a globe valve allows for a more precise control of flow compared to gate valves, making them suitable for applications where flow rate needs to be adjusted frequently.
Ball Valves
Ball valves are known for their durability and excellent shut-off capabilities. They use a spherical disc to control the flow of fluid and are ideal for applications requiring a tight seal. Ball valves are easy to operate and maintain, making them a popular choice in many industrial settings.
Butterfly Valves
Butterfly valves are used for isolating or regulating flow. They are lightweight, cost-effective, and provide quick shut-off capabilities. These valves are suitable for applications with limited space and are often used in large diameter pipelines due to their compact design.
Check Valves
Check valves, also known as non-return valves, allow fluid to flow in one direction only. They are used to prevent backflow in a system, which can cause damage to equipment or disrupt processes. Check valves are essential in applications where maintaining a unidirectional flow is critical.
Key Considerations for Selecting Industrial Valves
Choosing the right industrial valve involves considering several factors to ensure optimal performance and longevity. Below are some key considerations to keep in mind when selecting a valve for your manufacturing process.
Material Compatibility
The material of the valve must be compatible with the fluid it will handle. Consider factors such as temperature, pressure, and chemical properties of the fluid to select a valve material that will withstand the operating conditions without corroding or degrading.
Pressure and Temperature Ratings
Valves are designed to operate within specific pressure and temperature ranges. Ensure that the valve you select can handle the maximum pressure and temperature of your application to prevent failure and ensure safety.
Flow Characteristics
Understanding the flow characteristics of a valve is crucial for selecting the right type. Consider whether the application requires full flow, throttling, or a specific flow pattern, and choose a valve that meets these requirements.
Maintenance and Accessibility
Consider the ease of maintenance and accessibility of the valve. Valves that are difficult to access or require complex maintenance procedures can lead to increased downtime and operational costs.
Cost and Budget
While cost should not be the sole determining factor, it is important to consider the budget for your project. Evaluate the total cost of ownership, including installation, maintenance, and potential downtime, to make a cost-effective decision.
Conclusion
Selecting the right industrial valve is a critical decision that can impact the efficiency, safety, and cost-effectiveness of your manufacturing process. By understanding the different types of valves and considering key factors such as material compatibility, pressure and temperature ratings, flow characteristics, maintenance, and cost, you can make an informed choice that meets your specific needs. Investing time in selecting the appropriate valve will pay off in the long run by ensuring reliable and efficient operation of your manufacturing system.