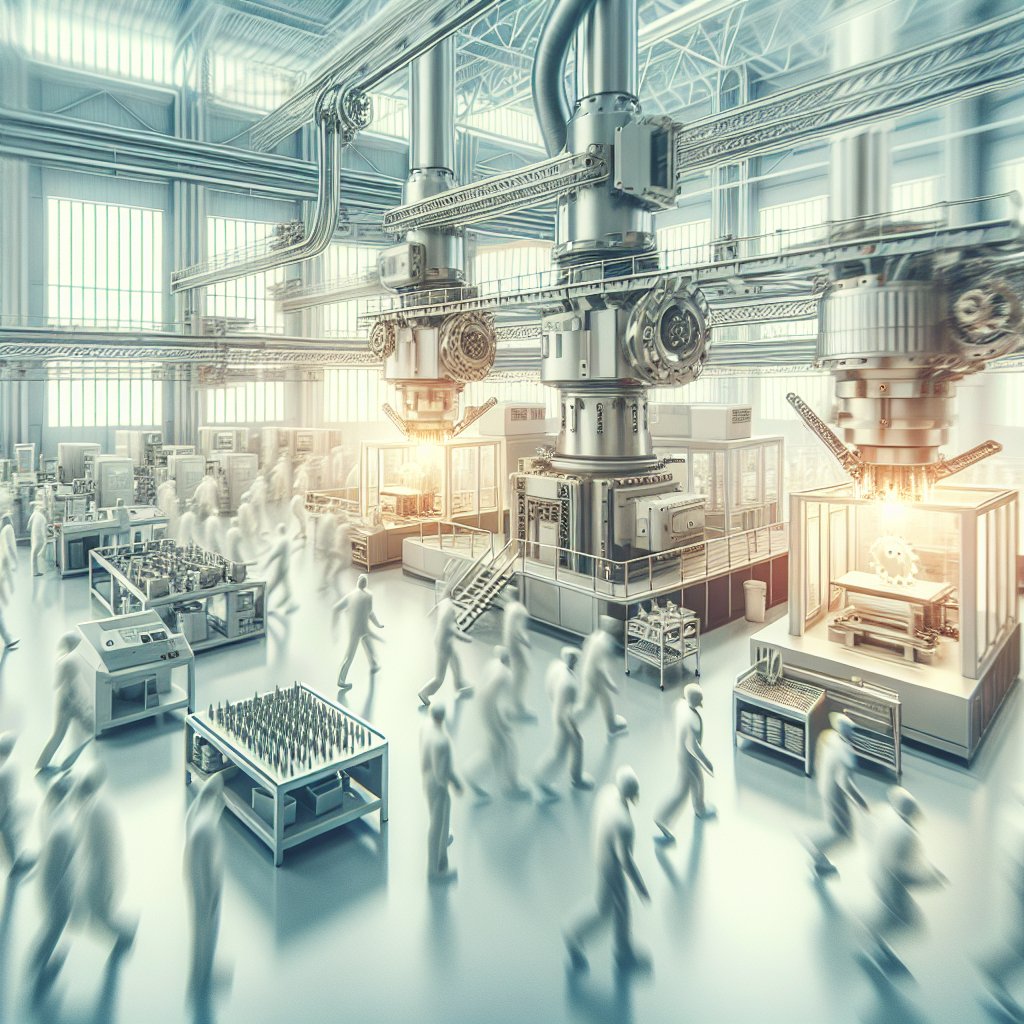
Additive manufacturing, commonly known as 3D printing, is revolutionizing the field of industrial prototyping by offering unprecedented flexibility, speed, and cost-effectiveness. This transformative technology is reshaping how industries approach the design and development of new products, enabling rapid prototyping and fostering innovation across various sectors.
The Evolution of Additive Manufacturing
The journey of additive manufacturing began in the 1980s with the advent of stereolithography, a process that laid the foundation for modern 3D printing technologies. Over the decades, advancements in materials, software, and hardware have propelled additive manufacturing from a niche technology to a mainstream industrial tool. Today, it encompasses a wide range of techniques, including selective laser sintering (SLS), fused deposition modeling (FDM), and direct metal laser sintering (DMLS), each offering unique advantages for prototyping and production.
One of the key drivers behind the adoption of additive manufacturing in industrial prototyping is its ability to create complex geometries that are difficult or impossible to achieve with traditional manufacturing methods. This capability allows designers to explore innovative designs without the constraints of conventional fabrication techniques. As a result, industries such as aerospace, automotive, and healthcare are leveraging additive manufacturing to push the boundaries of what is possible in product development.
Benefits of Additive Manufacturing in Prototyping
Additive manufacturing offers several significant benefits that are transforming the prototyping process. One of the most notable advantages is the reduction in lead times. Traditional prototyping methods often involve multiple steps, including tooling and machining, which can be time-consuming and costly. In contrast, additive manufacturing allows for the direct creation of prototypes from digital models, significantly shortening the development cycle.
Moreover, additive manufacturing enables cost savings by eliminating the need for expensive tooling and reducing material waste. In traditional manufacturing, producing a prototype often requires the creation of molds or dies, which can be prohibitively expensive for small production runs. Additive manufacturing bypasses this requirement, allowing for the economical production of prototypes and small batches.
Another critical benefit is the ability to iterate designs quickly. With additive manufacturing, designers can make rapid adjustments to prototypes based on testing and feedback, facilitating a more agile development process. This flexibility is particularly valuable in industries where time-to-market is a crucial factor, enabling companies to respond swiftly to market demands and technological advancements.
Challenges and Future Prospects
Despite its numerous advantages, additive manufacturing also presents certain challenges that need to be addressed. One of the primary concerns is the limited range of materials available for 3D printing compared to traditional manufacturing. While significant progress has been made in developing new materials, including metals, ceramics, and composites, the selection is still not as extensive as conventional options.
Additionally, the quality and consistency of 3D-printed parts can vary depending on the technology and materials used. Ensuring that prototypes meet the required standards for strength, durability, and precision remains a challenge, particularly for industries with stringent regulatory requirements.
Looking ahead, the future of additive manufacturing in industrial prototyping is promising. Ongoing research and development efforts are focused on expanding the range of printable materials, improving the speed and accuracy of 3D printers, and integrating additive manufacturing with other digital technologies such as artificial intelligence and the Internet of Things. These advancements are expected to further enhance the capabilities of additive manufacturing, making it an even more integral part of the industrial prototyping landscape.
In conclusion, additive manufacturing is reshaping the way industries approach prototyping, offering a host of benefits that are driving innovation and efficiency. As the technology continues to evolve, it is poised to play an increasingly vital role in the development of new products, paving the way for a future where rapid, cost-effective prototyping is the norm rather than the exception.