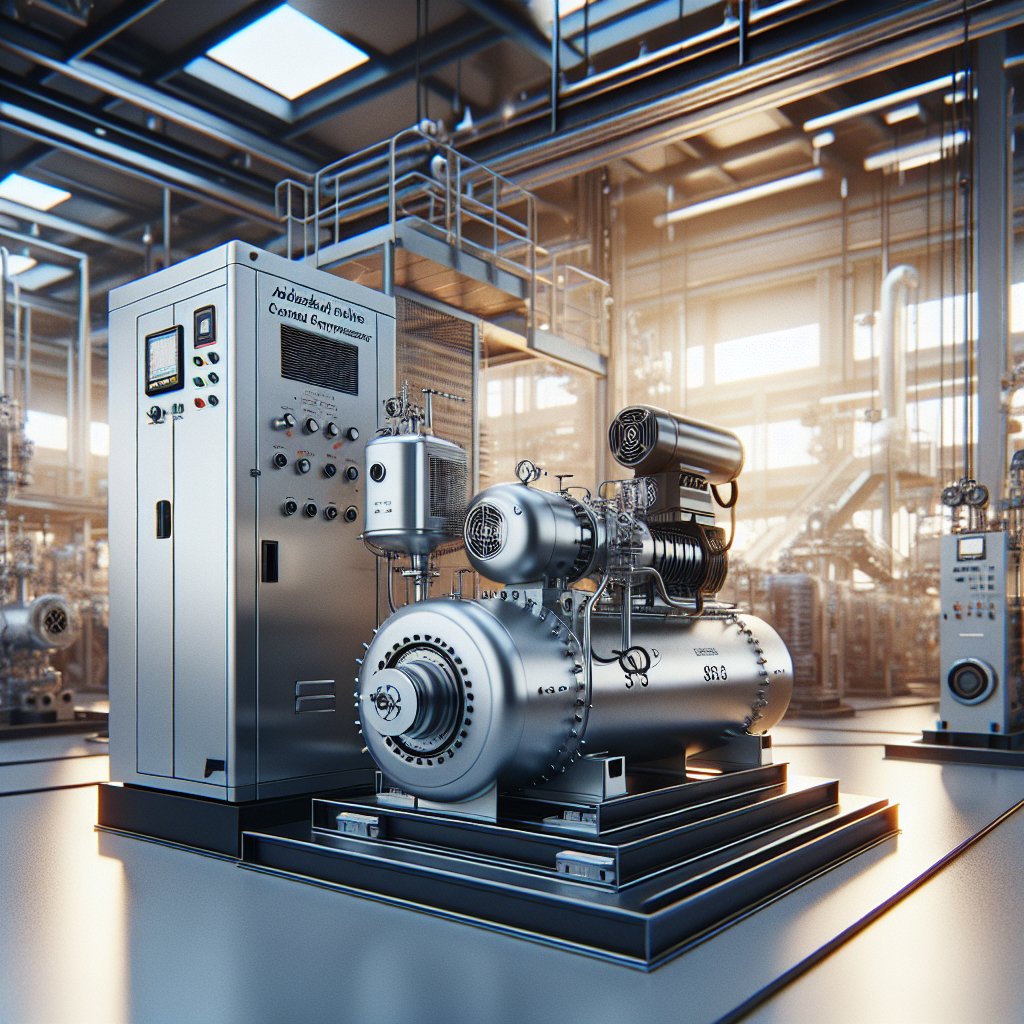
Choosing the right industrial compressor for your application is a critical decision that can significantly impact the efficiency and cost-effectiveness of your operations. Industrial compressors are essential components in various industries, providing the necessary power to drive machinery, tools, and processes. With a wide range of compressor types and specifications available, selecting the most suitable one requires careful consideration of several factors. This article will guide you through the key aspects to consider when choosing an industrial compressor, ensuring that you make an informed decision that meets your specific needs.
Understanding Different Types of Industrial Compressors
Industrial compressors come in various types, each designed to meet specific operational requirements. Understanding the differences between these types is crucial in selecting the right compressor for your application. The most common types of industrial compressors include reciprocating compressors, rotary screw compressors, and centrifugal compressors.
Reciprocating Compressors
Reciprocating compressors, also known as piston compressors, are widely used in industries that require high-pressure air. These compressors operate by using pistons driven by a crankshaft to compress air. They are known for their durability and ability to deliver high-pressure output, making them ideal for applications such as automotive repair, construction, and manufacturing.
One of the main advantages of reciprocating compressors is their ability to handle intermittent duty cycles, which means they can operate efficiently even when not in continuous use. However, they tend to be noisier and require more maintenance compared to other types of compressors. It’s essential to consider these factors when deciding if a reciprocating compressor is suitable for your application.
Rotary Screw Compressors
Rotary screw compressors are known for their efficiency and reliability, making them a popular choice in industries that require continuous operation. These compressors use two interlocking helical rotors to compress air, providing a steady flow of compressed air with minimal pulsation. This makes them ideal for applications such as food and beverage production, pharmaceuticals, and chemical processing.
One of the key benefits of rotary screw compressors is their ability to operate quietly and with minimal vibration, which can be advantageous in environments where noise reduction is a priority. Additionally, they require less maintenance compared to reciprocating compressors, making them a cost-effective option for long-term use. However, they may not be suitable for applications that require extremely high-pressure output.
Centrifugal Compressors
Centrifugal compressors are designed for high-capacity applications, providing large volumes of compressed air at relatively low pressures. These compressors use a rotating impeller to accelerate and compress air, making them ideal for industries such as oil and gas, petrochemicals, and power generation.
One of the main advantages of centrifugal compressors is their ability to deliver a continuous flow of compressed air with high efficiency. They are also known for their low maintenance requirements and long lifespan, making them a reliable choice for large-scale operations. However, they tend to be more expensive and complex to install compared to other types of compressors, which may be a consideration for smaller businesses or applications with limited budgets.
Factors to Consider When Choosing an Industrial Compressor
When selecting an industrial compressor, it’s essential to consider several factors to ensure that you choose the right one for your specific application. These factors include the required pressure and flow rate, the type of application, energy efficiency, and maintenance requirements.
Pressure and Flow Rate Requirements
The pressure and flow rate requirements of your application are critical factors in determining the type and size of the compressor you need. It’s essential to assess the maximum pressure and flow rate required by your equipment and processes to ensure that the compressor can meet these demands. Choosing a compressor with insufficient capacity can lead to operational inefficiencies and increased wear and tear on the equipment.
Conversely, selecting a compressor with excessive capacity can result in higher energy consumption and increased operational costs. It’s important to strike a balance between meeting your application’s requirements and optimizing energy efficiency.
Type of Application
The type of application for which the compressor will be used is another crucial consideration. Different applications have varying demands in terms of pressure, flow rate, and duty cycle. For example, applications that require continuous operation, such as manufacturing or chemical processing, may benefit from the reliability and efficiency of rotary screw compressors.
On the other hand, applications that require high-pressure output for short periods, such as automotive repair or construction, may be better suited to reciprocating compressors. Understanding the specific needs of your application will help you choose the most appropriate compressor type.
Energy Efficiency
Energy efficiency is a significant consideration when selecting an industrial compressor, as it can have a substantial impact on operational costs. Compressors are energy-intensive machines, and choosing an energy-efficient model can lead to significant cost savings over time. Look for compressors with high energy efficiency ratings and features such as variable speed drives, which can help optimize energy consumption based on demand.
Additionally, consider the overall lifecycle cost of the compressor, including initial purchase price, energy consumption, and maintenance expenses. An energy-efficient compressor may have a higher upfront cost but can provide long-term savings through reduced energy bills and maintenance costs.
Maintenance Requirements
Maintenance requirements are another important factor to consider when choosing an industrial compressor. Regular maintenance is essential to ensure the reliable and efficient operation of the compressor, and different types of compressors have varying maintenance needs.
Reciprocating compressors typically require more frequent maintenance due to their complex mechanical components, while rotary screw compressors and centrifugal compressors tend to have lower maintenance requirements. Consider the availability of maintenance resources and the cost of spare parts when evaluating the maintenance needs of different compressor types.
Conclusion
Choosing the right industrial compressor for your application is a critical decision that requires careful consideration of various factors, including the type of compressor, pressure and flow rate requirements, application type, energy efficiency, and maintenance needs. By understanding the differences between reciprocating, rotary screw, and centrifugal compressors, and evaluating your specific operational requirements, you can make an informed decision that ensures the efficiency and cost-effectiveness of your operations.
Ultimately, the right compressor will not only meet your current needs but also provide the flexibility and reliability to support your business’s growth and evolving demands. Investing time and effort in selecting the most suitable industrial compressor will pay off in the long run, contributing to the success and sustainability of your operations.