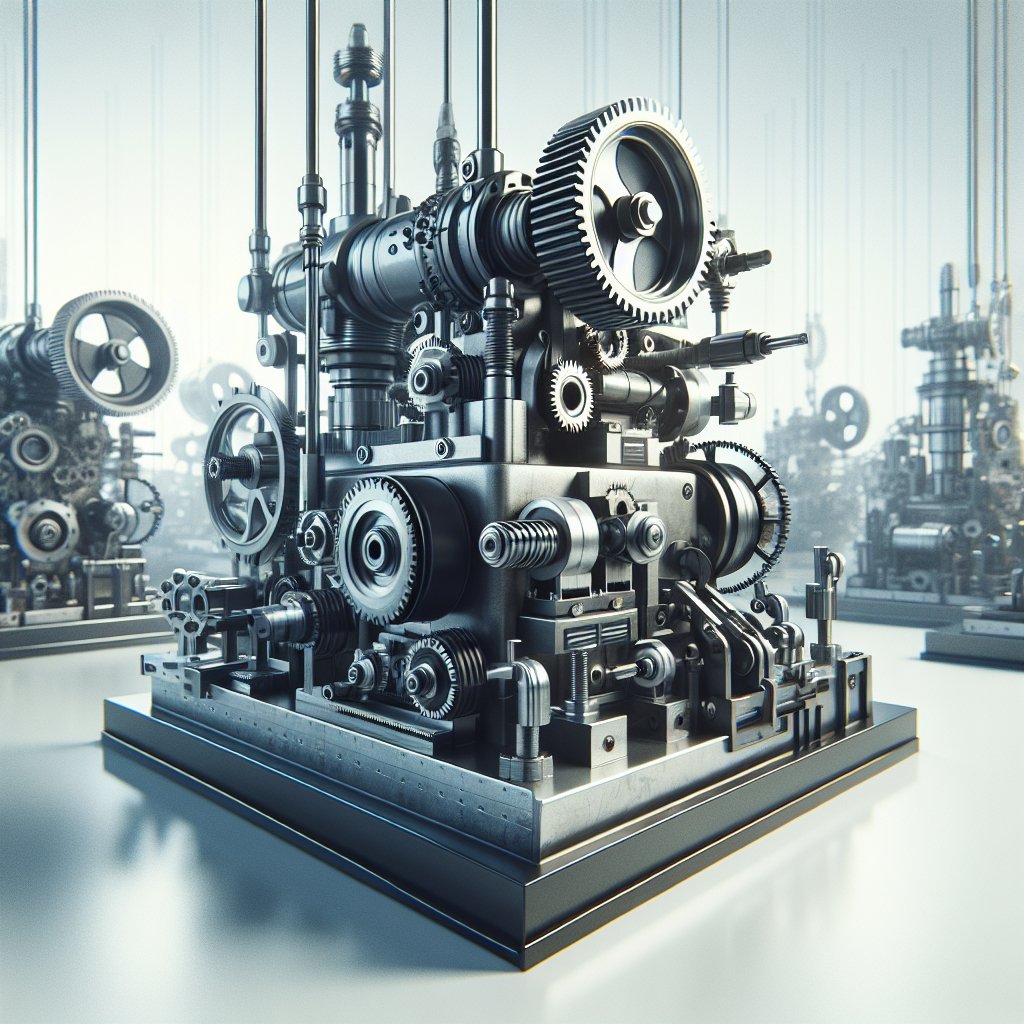
Torque measurement plays a crucial role in the efficient operation and maintenance of industrial machinery. Understanding the importance of torque and its accurate measurement can lead to improved performance, reduced downtime, and enhanced safety in various industrial applications. This article delves into the significance of torque measurement, exploring its applications, benefits, and the technologies involved.
Understanding Torque and Its Relevance
Torque, often referred to as the rotational equivalent of linear force, is a measure of the force that can cause an object to rotate about an axis. In industrial machinery, torque is a critical parameter that influences the performance and efficiency of equipment. It is essential to understand the concept of torque to appreciate its impact on machinery and the importance of its measurement.
In simple terms, torque is the product of the force applied and the distance from the point of application to the axis of rotation. It is typically measured in units such as Newton-meters (Nm) or foot-pounds (ft-lb). Torque is a fundamental aspect of mechanical systems, as it determines the ability of a machine to perform work, such as lifting, turning, or driving components.
In industrial settings, torque measurement is vital for several reasons. It helps in ensuring that machinery operates within its designed parameters, preventing overloading and potential damage. Accurate torque measurement also aids in quality control, ensuring that products meet specified standards and tolerances. Furthermore, it plays a significant role in predictive maintenance, allowing for the early detection of issues that could lead to costly downtime.
Applications of Torque Measurement in Industry
The applications of torque measurement in industrial machinery are diverse and span across various sectors. From manufacturing and automotive to aerospace and energy, torque measurement is integral to the efficient functioning of machinery and equipment.
Manufacturing
In the manufacturing industry, torque measurement is crucial for assembly processes, where precise torque application ensures the integrity and reliability of assembled components. For instance, in the automotive sector, accurate torque measurement is essential for tightening bolts and fasteners to the correct specifications, preventing issues such as loose connections or component failure.
Moreover, torque measurement is used in quality control processes to verify that products meet the required standards. By measuring the torque required to operate or assemble a product, manufacturers can ensure consistency and quality, reducing the risk of defects and recalls.
Automotive
In the automotive industry, torque measurement is vital for engine testing and development. It helps engineers assess the performance of engines and drivetrains, ensuring that vehicles deliver the desired power and efficiency. Torque measurement is also used in the testing of components such as transmissions, differentials, and axles, where precise torque application is critical for optimal performance.
Additionally, torque measurement is employed in the calibration of tools and equipment used in automotive assembly lines. By ensuring that tools apply the correct torque, manufacturers can maintain the quality and safety of their vehicles, reducing the risk of failures and accidents.
Aerospace
In the aerospace industry, torque measurement is essential for the assembly and maintenance of aircraft components. Accurate torque application is critical for ensuring the structural integrity and safety of aircraft, where even minor deviations can have significant consequences.
Torque measurement is also used in the testing and development of aerospace components, such as engines and landing gear. By measuring the torque required to operate these components, engineers can optimize their design and performance, enhancing the safety and efficiency of aircraft.
Energy
In the energy sector, torque measurement is crucial for the operation and maintenance of equipment such as wind turbines, generators, and pumps. Accurate torque measurement ensures that these machines operate within their designed parameters, preventing overloading and potential damage.
Torque measurement is also used in the testing and development of energy equipment, where precise torque application is critical for optimizing performance and efficiency. By measuring the torque required to operate these machines, engineers can identify areas for improvement and enhance their design and functionality.
Benefits of Accurate Torque Measurement
Accurate torque measurement offers several benefits for industrial machinery, contributing to improved performance, reduced downtime, and enhanced safety. By understanding the importance of torque measurement, industries can leverage these benefits to optimize their operations and achieve greater efficiency.
Improved Performance
Accurate torque measurement ensures that machinery operates within its designed parameters, optimizing performance and efficiency. By applying the correct torque, industries can prevent issues such as overloading, excessive wear, and component failure, enhancing the reliability and longevity of their equipment.
Moreover, accurate torque measurement allows for the fine-tuning of machinery, enabling industries to achieve the desired performance and output. By measuring and adjusting torque, industries can optimize their processes, reducing waste and improving productivity.
Reduced Downtime
Torque measurement plays a significant role in predictive maintenance, allowing for the early detection of issues that could lead to costly downtime. By monitoring torque levels, industries can identify potential problems before they escalate, enabling timely maintenance and repairs.
Furthermore, accurate torque measurement helps prevent overloading and damage to machinery, reducing the risk of unexpected breakdowns and downtime. By ensuring that equipment operates within its designed parameters, industries can minimize disruptions and maintain continuous operations.
Enhanced Safety
Accurate torque measurement is critical for ensuring the safety of industrial machinery and equipment. By applying the correct torque, industries can prevent issues such as loose connections, component failure, and structural damage, reducing the risk of accidents and injuries.
Moreover, torque measurement is essential for compliance with safety standards and regulations, ensuring that machinery meets the required specifications and tolerances. By adhering to these standards, industries can enhance the safety of their operations and protect their workforce.
Technologies for Torque Measurement
Several technologies are available for torque measurement, each offering unique advantages and capabilities. By understanding these technologies, industries can select the most suitable solution for their specific applications and requirements.
Strain Gauge Torque Sensors
Strain gauge torque sensors are one of the most common technologies used for torque measurement. These sensors use strain gauges, which are bonded to a shaft or component, to measure the deformation caused by applied torque. The deformation is converted into an electrical signal, which is proportional to the torque applied.
Strain gauge torque sensors offer high accuracy and reliability, making them suitable for a wide range of industrial applications. They are available in various configurations, including rotary and reaction types, allowing for flexibility in measurement and installation.
Magnetoelastic Torque Sensors
Magnetoelastic torque sensors use the principle of magnetoelasticity, where the magnetic properties of a material change in response to applied stress or strain. These sensors measure the change in magnetic properties caused by applied torque, providing a non-contact and robust solution for torque measurement.
Magnetoelastic torque sensors offer several advantages, including high accuracy, durability, and resistance to environmental factors such as temperature and humidity. They are suitable for applications where non-contact measurement is required, such as in harsh or challenging environments.
Optical Torque Sensors
Optical torque sensors use light-based technologies, such as fiber optics or laser interferometry, to measure torque. These sensors detect changes in light properties, such as intensity or phase, caused by applied torque, providing a high-precision and non-contact solution for torque measurement.
Optical torque sensors offer several benefits, including high accuracy, immunity to electromagnetic interference, and the ability to measure torque in challenging environments. They are suitable for applications where precision and reliability are critical, such as in aerospace and research settings.
Conclusion
Torque measurement is a vital aspect of industrial machinery, influencing performance, efficiency, and safety. By understanding the importance of torque and its accurate measurement, industries can optimize their operations, reduce downtime, and enhance safety. With various technologies available for torque measurement, industries can select the most suitable solution for their specific applications, ensuring the reliable and efficient operation of their machinery.