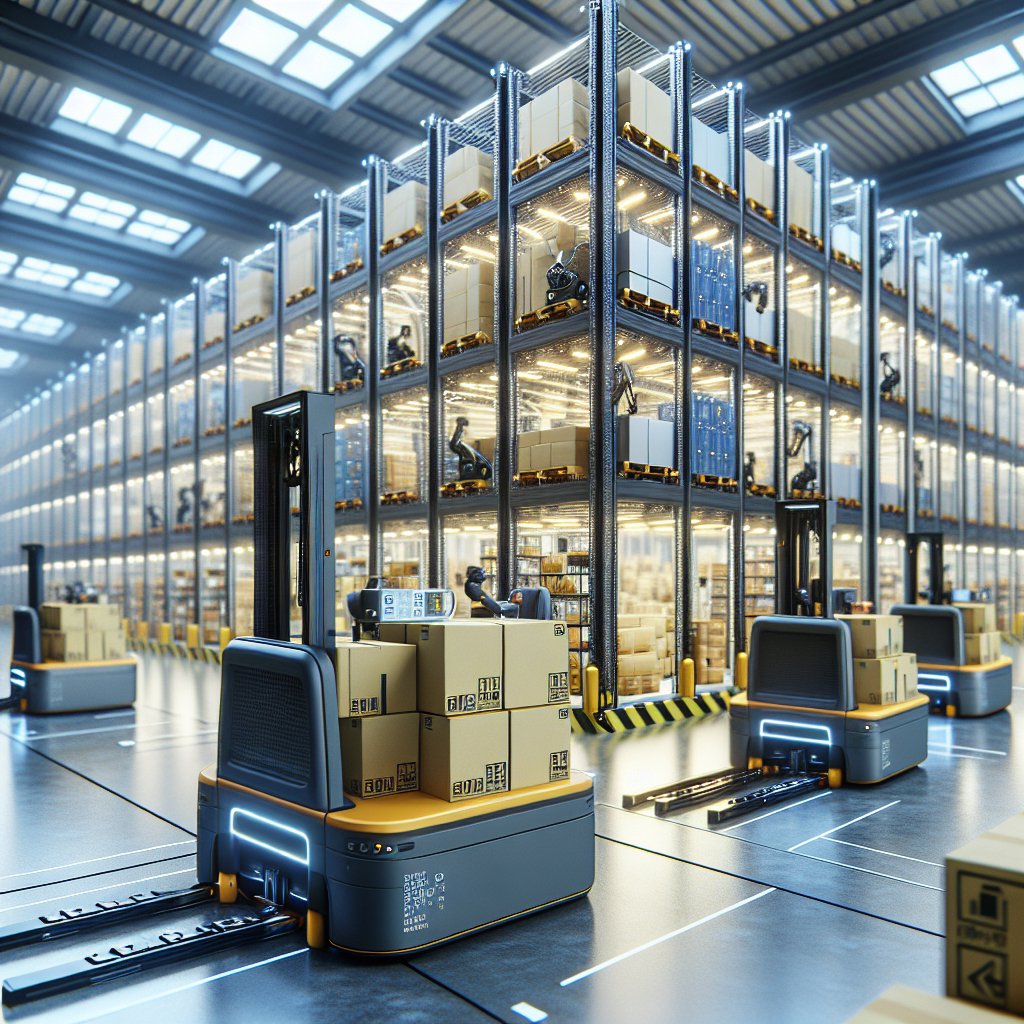
Automated Guided Vehicles (AGVs) have revolutionized the logistics and warehousing industry by offering a range of benefits that enhance efficiency, safety, and cost-effectiveness. As warehouses continue to evolve with technological advancements, AGVs play a crucial role in streamlining operations and optimizing workflows. This article delves into the various advantages of implementing AGVs in warehouse settings, exploring how they contribute to improved productivity and operational excellence.
Enhanced Efficiency and Productivity
One of the primary benefits of using AGVs in warehouses is the significant boost in efficiency and productivity. AGVs are designed to perform repetitive tasks with precision and consistency, reducing the need for manual labor and minimizing human error. By automating the transportation of goods within the warehouse, AGVs allow human workers to focus on more complex and value-added tasks, thereby increasing overall productivity.
AGVs can operate around the clock without the need for breaks, ensuring continuous workflow and reducing downtime. This capability is particularly beneficial in high-demand environments where time is of the essence. With AGVs handling the transportation of materials, warehouses can achieve faster turnaround times and meet customer demands more effectively.
Optimized Workflow
AGVs contribute to optimized workflow by seamlessly integrating with warehouse management systems (WMS) and other automated technologies. This integration allows for real-time tracking and management of inventory, ensuring that goods are transported to the right location at the right time. The precision and reliability of AGVs help in maintaining a smooth flow of materials, reducing bottlenecks and improving overall operational efficiency.
Moreover, AGVs can be programmed to follow specific routes and schedules, ensuring that tasks are completed in a timely and organized manner. This level of automation not only enhances productivity but also improves the accuracy of inventory management, reducing the risk of stockouts or overstocking.
Improved Safety and Risk Reduction
Safety is a paramount concern in warehouse operations, and AGVs play a significant role in enhancing workplace safety. By automating the transportation of goods, AGVs reduce the need for human workers to perform potentially hazardous tasks, such as lifting heavy loads or operating forklifts. This reduction in manual handling minimizes the risk of workplace injuries and accidents.
AGVs are equipped with advanced sensors and navigation systems that allow them to detect obstacles and navigate safely within the warehouse environment. These systems enable AGVs to operate in close proximity to human workers and other equipment without compromising safety. In the event of an obstacle or unexpected situation, AGVs can stop or reroute themselves to prevent collisions, further enhancing safety measures.
Consistent and Predictable Operations
The use of AGVs ensures consistent and predictable operations, which is crucial for maintaining a safe working environment. Unlike human workers, AGVs do not experience fatigue or distractions, allowing them to perform tasks with a high level of consistency and reliability. This predictability reduces the likelihood of errors and accidents, contributing to a safer workplace.
Additionally, AGVs can be programmed to adhere to specific safety protocols and guidelines, ensuring compliance with industry standards and regulations. This adherence to safety measures not only protects workers but also minimizes the risk of damage to goods and equipment, further reducing operational risks.
Cost-Effectiveness and Return on Investment
Implementing AGVs in warehouses can lead to significant cost savings and a favorable return on investment (ROI). While the initial investment in AGV technology may be substantial, the long-term benefits often outweigh the costs. AGVs reduce labor costs by automating repetitive tasks, allowing warehouses to allocate human resources more efficiently.
Moreover, AGVs contribute to cost savings by minimizing errors and reducing the need for rework or corrections. The precision and accuracy of AGVs ensure that goods are transported and stored correctly, reducing the risk of damage or loss. This reduction in errors translates to lower operational costs and improved profitability.
Scalability and Flexibility
AGVs offer scalability and flexibility, making them a cost-effective solution for warehouses of all sizes. As business needs evolve, AGVs can be easily reprogrammed or reconfigured to accommodate changes in workflow or layout. This adaptability allows warehouses to scale their operations without the need for significant infrastructure changes or additional labor costs.
Furthermore, AGVs can be integrated with other automated systems, such as robotic picking and sorting technologies, to create a fully automated warehouse environment. This integration enhances the overall efficiency and cost-effectiveness of warehouse operations, providing a competitive edge in the logistics industry.
Conclusion
In conclusion, the benefits of using Automated Guided Vehicles in warehouses are manifold, ranging from enhanced efficiency and productivity to improved safety and cost-effectiveness. As warehouses continue to embrace automation and technological advancements, AGVs will play an increasingly vital role in optimizing operations and driving business success. By investing in AGV technology, warehouses can achieve greater operational excellence, meet customer demands more effectively, and maintain a competitive edge in the ever-evolving logistics landscape.