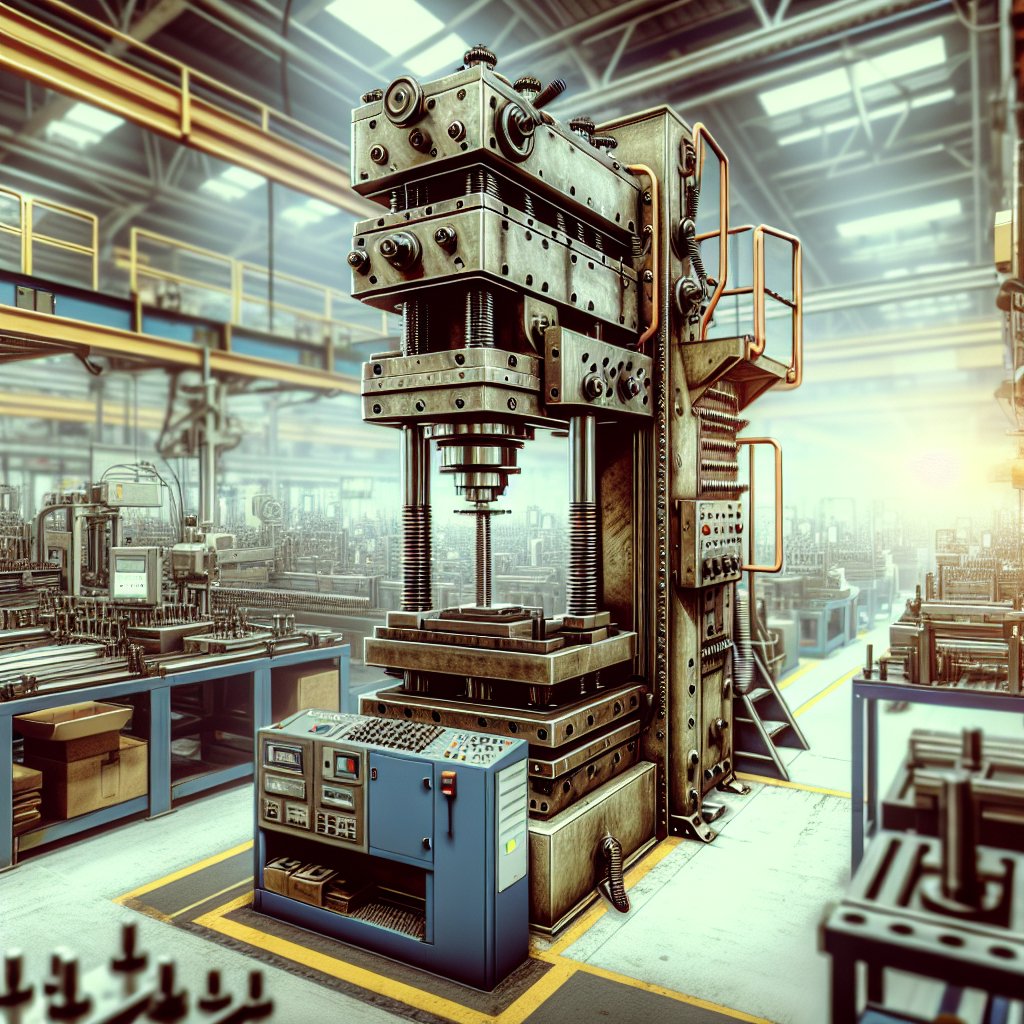
Hydraulic presses are a cornerstone in the manufacturing industry, offering unparalleled power and precision for a variety of applications. These machines utilize the principles of hydraulics to exert a significant amount of force, making them indispensable in processes such as metal forming, molding, and assembly. This article delves into the functionality of hydraulic presses, exploring their components, operation, and the diverse roles they play in modern manufacturing.
Components and Operation of Hydraulic Presses
At the heart of a hydraulic press is its ability to convert hydraulic energy into mechanical force. This is achieved through a series of components that work in harmony to deliver the desired output. The primary components of a hydraulic press include the hydraulic cylinder, pump, motor, valves, and the press frame. Each of these parts plays a crucial role in the operation of the press.
The hydraulic cylinder is the core component where the conversion of energy takes place. It consists of a piston that moves within a cylindrical chamber, driven by the pressure of hydraulic fluid. The pump is responsible for moving the hydraulic fluid from the reservoir into the cylinder, while the motor powers the pump. Valves control the flow and direction of the fluid, ensuring that the press operates smoothly and efficiently. The press frame provides the structural support necessary to withstand the immense forces generated during operation.
The operation of a hydraulic press begins with the activation of the motor, which drives the pump to move hydraulic fluid into the cylinder. As the fluid enters the cylinder, it pushes against the piston, creating a force that is transferred to the press plate. This force is then applied to the material being processed, whether it be metal, plastic, or another substance. The precision of hydraulic presses allows for exact control over the force and speed applied, making them ideal for tasks that require high accuracy.
Applications and Advantages in Manufacturing
Hydraulic presses are utilized in a wide range of manufacturing applications due to their versatility and efficiency. One of the most common uses is in metal forming, where they are employed to shape and mold metal parts. The ability to apply consistent pressure makes hydraulic presses ideal for tasks such as stamping, bending, and drawing. In addition to metal forming, hydraulic presses are also used in the production of plastic components, where they assist in molding and shaping materials into desired forms.
Another significant application of hydraulic presses is in the assembly of components. They are often used to press-fit parts together, ensuring a secure and precise fit. This is particularly important in industries such as automotive and aerospace, where the integrity of assembled components is critical. Hydraulic presses are also used in the compaction of materials, such as in the production of composite materials and the recycling of waste products.
The advantages of hydraulic presses in manufacturing are numerous. Their ability to exert a high level of force with precision makes them suitable for a variety of tasks. They are also highly adaptable, with the capability to be customized for specific applications. Additionally, hydraulic presses are known for their durability and reliability, often requiring less maintenance than other types of presses. This makes them a cost-effective solution for manufacturers looking to optimize their production processes.
Conclusion
In conclusion, hydraulic presses are an essential tool in the manufacturing industry, offering a combination of power, precision, and versatility. Their ability to perform a wide range of tasks with high accuracy makes them invaluable in the production of metal and plastic components, as well as in the assembly and compaction of materials. As technology continues to advance, the functionality and applications of hydraulic presses are likely to expand, further solidifying their role as a critical component in modern manufacturing.